Education Vs. Experience: Which Is More Important In GMP Operations?
By Joanna Gallant, Joanna Gallant Training Associates, LLC
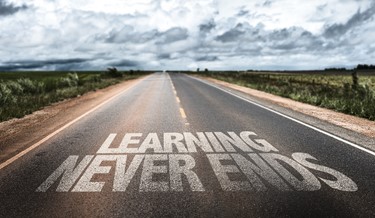
I’ve noticed recently that most job descriptions I’ve seen in GMP companies now require a college degree, which leads me to the question: Are we overvaluing educational degrees and undervaluing experience in our hiring practices and position expectations?
I live outside of Boston, an area where there are a number of world-class educational institutions and at least 350 GMP (those either working in or working toward commercial production of product, in a physical or virtual sense) bio/pharmaceutical or medical device companies in a fairly short radius. And I’ve recently had the opportunity to look at job descriptions of positions at some of these companies.
I’ve also worked in the realm of personnel qualification and training for 25+ years, determining how to effectively teach people what they need to know to perform tasks or trying to fill open positions with people who are a good fit. In that time, I’ve discovered that while you can teach many things, there are also things we only learn through experience.
I’m not sure sometimes that we consider that difference. But it’s why the GMPs define personnel qualification to perform job tasks as a combination of education, training, and experience.
Let’s start with two separate events — with more to follow:
First, for several years, I taught basic GMP in a local college program on the basics of biotechnology and production of biopharmaceuticals, intended to help individuals transition into manufacturing positions in local companies. One day, the program director asked to meet before my session. Apparently, a number of local companies had asked whether a similar program could be created that would produce qualified quality assurance (QA) people, because the companies were having a hard time filling open QA positions.
Second, after an FDA inspection, a company received a 483 observation that called into question the qualification of its personnel. In this case, the FDA investigators cited the personnel at the company who were performing and interpreting microbiological testing for not having appropriate education and experience in microbiology, because of issues seen in the process:
“Employees are not given training in the particular operations they perform as part of their function. Specifically, the firm failed to document the sterility test technicians and their supervisor were adequately trained for their job role to detect contaminated sterility test samples and media fill vials. The job description for a Sterility Test Technician requires a high school diploma or equivalent and 1-5 years of related experience. The job description is silent on minimal requirements for education and experience to interpret microbial contamination in sterility test samples and media fill units.
The job description reads in part, "The position requires 1-5 years of aseptic processing experience. Experience must include aseptic technique, cleanroom gowning practices, and cGMP-based documentation skills. Incumbent will perform the sterility test, read the sterility tests at set incubation periods (check for contamination) and enter results".”
“There is no written procedure for quality unit review and approval of job position qualification and job descriptions for personnel to ensure personnel will have the education and experience required to successfully perform GMP operations.”
The Value Of Education
In the latter situation, if the personnel in question had an education in microbiology, those inspecting the sterility tests would have recognized that cloudiness in growth media indicated contamination was likely present and could have been an early indication that bacteria was growing in the media — which would have indicated an issue with the sterility test and possibly the sterility of the product.
Further, having that background education in microbiology also provides time to develop a variety of skills. As a former microbiology major myself, I learned — in an academic laboratory, versus a GMP production environment — how to perform isolations, differential staining techniques, and identification of bacterial isolates, and I saw firsthand the impact that the quality of my handling, sterilization, and aseptic techniques had on my lab projects.
Learning those same lessons in a GMP production environment can be very costly to a company, triggering possible testing failures, investigations, and possible batch rejections. Further, if it couldn’t be proven — with evidence — in a failure investigation that poor technique caused the contamination found in a test sample, the company would be expected to make a conservative decision and fail the batch, because a batch of product — whether intended to be sterile or not — potentially contaminated with bacteria is a potential patient safety issue.
Education provides valuable background knowledge for GMP environments to build upon. Science and engineering degrees are of particular interest, but writing, education, computer science, business, and medical/veterinary degrees (among others) also play a large role in our operations today. Further, any degree provides some level of confirmation that the person who earned it has developed critical thinking skills, has the ability to communicate thoughts and ideas in a logical fashion, and has a battery of skills and practices that will enable learning things outside of their area of specialization.
But it’s not enough to just have the educational background — it’s simply the foundation to build upon. Here’s one example why:
I was asked to walk through a college program preparing people to work in bio/pharma environments. The question to me was, “What can we do to make this more like the real GMP manufacturing environment?” Now, I’m in no way an expert in manufacturing processes, but I said I’d try.
I was led through an open college lab, and the manufacturing activities performed in this area were ones industry would do in cleanrooms — but, among other differences:
- The students didn’t have to gown or follow aseptic practices
- Open product manipulations occurred on the lab bench, versus in laminar flow hoods or isolators
- There were no cleanroom-style controls like passthrough airlocks or sanitization of items prior to use, and
- Notebooks, scratch paper, and lab reports were used instead of batch records, and good documentation practices were not applied.
After the tour, I raised these as items that could be added to make the experience more realistic. Even if the environmental control wasn’t cleanroom quality, the practices that would be used in the environment could be factored in, with this being an area where technique could be learned and not pose a significant risk to GMP operations.
There were two responses. One was that the program didn’t have the resources to implement and supply these activities for the whole class for the length of the course. The other was that some had been used on occasion, but the students found them to be difficult or unpleasant working conditions, so they weren’t made regular practice so the learning environment could be more comfortable.
While this isn’t the case with every college program — some mimic and others actually replicate the environment and the controls we use — not all institutions are able to offer these elements. Making this happen requires a significant investment for the schools, consistent student interest and participation in the program (possibly with additional cost to the students), and faculty with industry experience who know what to do in these environments.
What About Experience?
While there are places in our companies where educational background provides a solid enough starting point for an employee to be successful, experience plays a significant role in others, and those without previous industry experience either may not have what it takes to be successful or could face a sharp learning curve to get there.
For example: After giving a GMP session in one of the programs I mentioned, to explain the controls industry must follow, one of the students approached me. She told me I had done a great job making GMP sound interesting, and she wanted to know how she could become a GMP trainer, too. She had a degree in elementary education and thought it would be a good fit for her.
Now, the best GMP training people I’ve seen have come from operational environments, where they have gained hands-on experience with GMP operations, and they also have a strong interest in helping others learn to do tasks well. Training skills can be taught — experience can’t.
So my answer was that if she wanted to be a good GMP trainer, she needed industry experience first — and the best place for that was manufacturing. I explained my background (which includes product development) and said that in retrospect, I felt I would be better at what I do had I worked in manufacturing as well. Without having GMP work experience, you don’t understand how and why we do what we do — and without that, you can’t teach people effectively because you can’t speak to what they’re doing and experiencing.
Her response? “I don’t want to do manufacturing — my interest is education.”
“Those who can’t do, teach” is a fallacy. You can’t teach what you don’t know. To put it bluntly, it’s dangerous to our operations to have people who lack experience providing guidance on what we need to do and why, because they can — and do — get it wrong.
Returning to the discussion about creating a program to teach QA: Can you create a program to teach QA? Sure. Will someone who completes that program be a better QA person than someone who hasn't? In certain ways, possibly. But I firmly believe it’s not enough.
Good QA requires experience with company processes, what can go wrong in these processes and environments, and an understanding of what does or can happen when it does go wrong. No matter how educated someone is, they’ll miss something if they lack experience with all of the elements that impact our company-specific processes — which means they can’t be an effective QA person without it.
The best QA people are the ones who come to those roles from the groups the QA function oversees. They’ve lived the process, so they know what has led to issues in the past, what types of problems to anticipate, and when or where in the process things can go wrong — and use this information to work to detect and eliminate future similar problems. Further, they’ve done this under QA oversight, so they know what types of things QA will look at or ask for, and they have received feedback from QA when those things didn’t meet expectations or requirements. When this person moves into QA, they have all this experience to draw on – which gives them a leg up on the person who simply completed the educational program.
The same applies in other areas as well. For a stark example of the difference experience brings, you needn’t look any further than the 2012 New England Compounding Center (NECC) disaster and the issues it highlighted with many of the compounding pharmacies that were making sterile medications at the time. (The following is not intended to comment on the current state of compounding pharmacies in general.)
An FDA investigator who performed some of the compounding pharmacy inspections triggered by the NECC disaster gave a talk at a past Good Manufacturing Practices Training & Education Association (GMP TEA, Inc.) conference. She explained that one of the consistent gaps investigators found was that the combination of education and experience was lacking in the personnel making product.
She described talking to one of the pharmacy personnel about their program for cleaning their cleanroom. They discussed the procedure and the frequency for the cleaning, and then she asked what they used to clean. The answer? “Swiffer.”
After the laughter in the room died down, the FDA investigator continued her story, saying that she then explained that, as your manufacturing area for sterile product, it needs to be sanitized and/or sterilized, to ensure microbes that could get into the product are removed. The person’s response? “We know that’s important — that’s why we use the antibacterial one.”
The takeaway? While personnel may have attended pharmacy school, they had not worked with or in sterile manufacturing operations — and sterile manufacturing processes weren’t taught in the pharmacy program. So when they set up their cleanrooms and defined their processes, while they thought they were doing the right things, they had no experience with industry standards for sterile manufacturing to draw from in terms of expectations in practice.
Even with the best intentions, you don’t know what you don’t know. Education can fill some of that gap, experience the rest. They’re both necessary.
How Do You Figure Out The Balance?
The answer is to consider what the job requires, and where educational background or experience is required to meet the elements of the job — and not promote or discount one or the other unnecessarily.
For example, is it necessary to require a biotech manufacturing operator to have a degree in biology? While it might enable the operator to understand more of what’s happening in the manufacturing process, it’s probably more than is necessary for someone to consistently follow a documented process. But for a manufacturing operator working with process development? Might be a good idea — where this person would provide feedback to the development team, a background in biology could enable them to recognize details that someone without it might miss. For a development scientist working to create a new biotech product and manufacturing process? Hard to argue against requiring a degree in biology or another science, because that knowledge will be needed to successfully execute the responsibilities of the position.
Think of it this way: If the person is likely to have learned the required skills or knowledge on the job (i.e., most schools don’t teach aseptic gowning or computer system validation, but companies do), then a degree may not add to the person’s ability to execute the position correctly. If not (i.e., most companies don’t teach basic microbiology techniques or chemical engineering skills for optimizing a manufacturing process), then the educational background becomes more important for the position. If they need some combination of the two, be reasonable in the expectations you set for each — and then abide by the parameters you’ve defined.
Because, as in other things we document, the FDA holds us to what we say are the required education and experience needs for our positions — as referenced by this warning letter excerpt:
“Failure to have sufficient personnel with the necessary education, background, training, and experience to assure that all activities…are correctly performed. For example:
a. The job description for the Director of Quality Systems requires that the person have a Bachelor of Science/Technical/or Engineering discipline. The person holding the position does not have this type of degree, but rather a Business Administration degree.
b. The person holding the Regulatory Affairs Manager position lacks the minimum of 5 years of regulatory experience required in the job description.
c. The person holding the Quality Control Supervisor position lacks the required bachelor’s degree in science or the alternative five to eight years’ experience in Quality Control.
d. The person holding the Calibration Coordinator position lacks the required bachelor’s degree and the four years of relevant experience.”
Don’t be too aggressive in what you want, though, because by doing so, you potentially lose out on good candidates. For example, if I say my QC analytical lab personnel need a master’s in chemistry — with no other parameters — anyone who applies without that master’s may fall out of contention in the screening process. This means the hiring manager may miss seeing the applicant with the bachelor’s degree and five years of QC lab experience — who might actually be a more attractive candidate, because they already have experience with GMP controls and expectations and have likely learned just as much in a practical setting as the master’s recipient did in the academic setting.
This is why the regulations call for education, experience, and training in combination … they support each other. One on its own may not be sufficient.
About The Author:
Joanna Gallant is an experienced, solutions-driven quality and training professional who has spent the last 25 years in pharmaceutical, biotechnology, tissue culture, and medical device development and manufacturing environments. Over her career, she has provided regulatory, technical, skill, and management development training support to all operations functions, as well as IT, R&D, customer service, and senior management. Now, as a consultant, she works with clients to design and deliver custom training and build/remediate training systems, including in support of regulatory audit observations and commitments.
Joanna has been a GMP TEA member since 2001, and now serves on the Board of Directors as an advisor. She is one of the founders of the Biomanufacturing Certificate Program at Worcester Polytechnic Institute and became an Adjunct Professor at the Boston University School of Medicine's Biotechnology degree program in 2011.
You can contact Joanna at Joanna@JGTA.net or connect with her on LinkedIn