How To Speed Up Time To Market With CMC Knowledge Management
By Irwin Hirsh, Q-Specialists AB
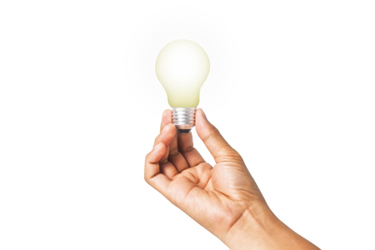
Business success in pharmaceuticals development hinges not just on groundbreaking discoveries and regulatory approval but also on effective and timely deployment of the technical and business process knowledge so that it becomes a strategic advantage over competitors.
Knowledge management (KM) is the strategic key to navigating regulatory complexities, accelerating innovation, and ensuring seamless operations that connect process and product. KM enables quality by design (QbD), provides clarity on development priorities, and is the linchpin for unlocking process efficiency as well as faster and better-informed decisions. This introductory article, the first in a four-part series, presents the business case for KM and the framework of understanding required to transform development groups into a higher level of productivity and value-add to the business.
Although the examples and context for discussion come from CMC process development, the approach and tools presented for knowledge management are agnostic and will add value anywhere in your value stream.
What Is Knowledge Management?
Knowledge management in the context of CMC development is the systematic organization and sharing of critical knowledge related to the process of development so that it is available for use when needed and continues to be built upon as new knowledge enters the organization and/or knowledge gaps are identified.
Costs Of Poor KM
In new drug development, CMC failures in knowledge management can significantly extend the time required for regulatory approval and, thus, market access. Failure to supply clinical trials is a particularly egregious example; other more subtle, yet more common, examples include:
- A poorly understood manufacturing process with high levels of variability. In the best case, such a process will reduce productivity and increase costs of non-quality for products that make it to the market. In the worst case, the inconsistency of batch performance also results in failed process validations and launch delays.
- Lack of robust analytical methods results in the inability to accurately assess variability in process parameters and their impact on product quality attributes. This can lead to a rejected dossier and request for additional data and experiments. On the market, it increases risks for scrap and even recalls.
- Inadequate documentation (knowledge sharing) commonly occurs when communicating about process capabilities, such as, for example, at changes of scale and location or between upstream and downstream processes after changes are made. Even well-designed processes may fail to win regulatory approval or suffer costly delays if development claims cannot be supported with documented evidence.
Knowledge Management Systems
The two most important knowledge management systems for CMC process development are:
- quality risk management (QRM) for the systematic management of the knowledge of quality risks (risk to the patient) across the product lifecycle including and starting with development and
- business process knowledge management. This is the know-how for performance of the tasks that are required in process development: from controlling raw materials and CDMOs to COGS modeling and process characterization studies.
The Business Case For Knowledge Management
A business should be eager to develop knowledge management, not because it increases compliance but because of the return on investment (ROI) it delivers to the business. Some improvements to ROI for CMC programs are highlighted below:
- Time to competency for those new to the organization and/or project is reduced by good knowledge sharing. When critical knowledge about the project and training in performance of the critical processes are available in a timely and systematic way, an individual’s movement in and out of a project causes minimal delays. Additionally, when the knowledge is explicit, such as, for example, available as a digital resource, team members have minimal disturbances to their ongoing work due to onboarding.
- Knowledge sharing kills ambiguity, reduces complexity, and increases productivity. Knowledge management achieves these benefits by creating clarity on roles and responsibilities. Task-specific process aides utilize critical knowledge collected so individuals know who must perform what standard work when and how. In such an environment specialists can turn their attention away from training and firefighting and look toward innovation.
- A systematic application of QRM across the entire life cycle of development provides clarity about the gaps between product requirements and manufacturing process capabilities. This knowledge enables limited resources to be focused on the most important needs of development.
- Timely knowledge sharing about these quality gaps maximizes the dynamic response of the process to the product demands and enables controlled changes in response to new clinical or business requirements. Additionally, should the entity be sold at any point in its development, a fair price can be negotiated based on a clear and substantiated risk profile.
Challenges To Implementation
Compliance with QRM
Although QRM could be considered a business process, it is singled out for its importance to process development and since the publication of ICH Q9 in 2005, it has been a regulatory expectation for which our industry has continuously faced challenges. Systematic application of QRM throughout the product life cycle, in my experience, has been tepid at best.
Instead of adding value as a life cycle tool, QRM is often reduced to a one-time effort in late-stage development. That’s in part because of complicating circumstances, including long development cycles across multiple departments with overlapping responsibilities but significantly different skills and focus areas; churn in staff; and under-allocation of resources until clinical Phase 3.
Understanding QRM knowledge flows
The following video presents an overview of how QRM information flows and knowledge is created during development to align process capabilities with product requirements. Understanding this conceptual framework is the essential first step to the successful systematic deployment of QRM.
Subsequent articles in this series will provide insights into the use of digital knowledge management tools to overcome the implementation challenges mentioned.
QRM as a compliance exercise
Too often, the first attempt for a systematic use of QRM begins in late-stage development, after the process is largely fixed. The focus of the QRM exercise is usually a process failure mode and effects analysis (FMEA) performed before PV to de-risk failure of demonstration batches and provide the information required to fill out the relevant sections of 3.S.2 in the CTD.
However significant this work is, when QRM starts in late-phase development it often contains significant information gaps on criticality for many of the process parameters. This results in gaps in the cause-and-effect knowledge about process parameters and their impact on product quality attributes. Additionally, such a late implementation of QRM is highly indicative that the knowledge captured will fail to become living knowledge passed on to the final site of manufacture to support changes planned or otherwise.
Similarly, any process that is not understood or fully implemented can at best deliver limited value. Many CMC processes suffer because they’re missing a common single source of knowledge. Multiple versions of the same process exist so that the same work is performed differently at different sites, departments, or even within the same project — in short, poor governance.
To derive business benefit from the knowledge generated by our processes, we must first understand how the processes work, what data are generated, and how that data can be used as knowledge to improve processes to meet business goals.
Lack of process orientation
Digital process management tools are now commonly available. We can use generic tools within the Microsoft Enterprise environment or shop for bespoke tools for specific use cases. However, when processes are poorly described, understood, implemented, and maintained, mapping them onto a digital platform can only result in faster failures and the elimination of the analog workarounds established to “get the job done” within the broken system of processes. In short, we suffer the garbage in/garbage out algorithm.
By applying a process orientation — I recommend the LEAN approach — we can stepwise unravel our processes and build business and process excellence. There is a general progression of work to be performed to bring processes under control before productivity gains can be realized. This progression is well expressed in the top 10 list below.
Top 10 Reasons Your Process Is Broken
- Process is not defined.
- Process is not owned.
- Process is not understood.
- Process is not followed.
- Customer is not understood.
- Supplier is not understood.
- Process is difficult to perform.
- Process is filled with waste.
- No performance metrics.
- Connection with the business strategy is lost.
More mature processes will suffer issues related to items further down the list. Less mature processes must tackle the first items on the list before they can even see the way forward to address the later items.
Figure 1 below depicts a systematic approach to process maturation. In this system, there is a progression through five levels of maturity wherein each level creates the environment that supports work to come.
This model was inspired by the work of Phillip Crosby, a late 20th-century quality guru, and the grid was created to support my clients who were kicking off a formal process governance system for their department.
For six months prior to this kickoff, to support the launch and ensure the process owners understood what they were working on, the fundamental work of simply cataloging and mapping the departmental processes was performed by the line managers and specialists.
Process Maturity Grid | ||||
---|---|---|---|---|
Maturity Level | Governance | Mapping | Metrics | Strategy |
1 | Process owners are trained. SOP in DMS clearly describes who does what and when. | Process mapping documents, flow mapping, and SIPOC are created. | Process KPIs are drafted. | Purpose is defined and the greatest challenges are identified. |
2 | Work instructions support the process (both GxP & non-GxP). | Improvement is identified via mapping analysis and stakeholder interviews. | KPIs are defined and measuring has begun. | Performance metrics are documented and communicated to stakeholders. |
3 | Job aids are created to support WI (checklists, decision trees, etc.). | Future state is mapped and creates new KPIs. | Process is measured and KPIs drive improvements. | Future state is used to identify and prioritize improvements |
4 | Qualified/certified trainers and mentors are available. | Interfaces with other departments are mapped. | KPIs are refined and include good leading indicators. | Process strategy is implemented. Risks are defined and monitored |
5 | Regular audits report excellence into the quality review process. | Materials and information flow mapping with metrics. | KPIs hit or exceed all targets. There is measurable site impact. | Risks to performance are controlled in real time. |
Figure 1: Process Maturity Grid (DMS = document management system, KPI = key performance indicator, WI = work instruction)
Management Participation
Direct participation by senior management is essential for successful knowledge management initiatives, as with any significant change management initiative.
Once management participation is firmly established and process maturation has moved forward, perhaps somewhere between levels 1 and 2, a concurrent project to rethink the digital knowledge management strategy of the organization is warranted.
Outdated Document Orientation For Data
Digitization of our processes and the data they create must change paradigms from document-centric to data-centric. At present, we often create documents that serve a purpose at a distinct point in time and, for compliance purposes, we must retain those documents. The knowledge within those documents is then frozen as PDF files, accessible and cataloged, but not likely to be widely known of or ever accessed. This is commonly called “paper to glass” and this knowledge, for all practical purposes, is lost.
Most manufacturing organizations begin their digital journey focused on mining manufacturing batch run data. However, development expects manufacturing methods to evolve, and the data mining gold is the experimental data that elucidates the cause-and-effect relationships between the process parameters and the product attributes.
Once development can prove, with data, that the process consistently produces product with the predefined quality attributes, optimization for business purposes can take precedence. Features to delight the customer and win market share come into being. Discussions around innovation and identification of IP can get the attention they deserve. Alternatively, development resources can simply be deployed to new entities.
About the Author:
Irwin Hirsh has nearly 30 years of pharma experience with a background in CMC encompassing discovery, development, manufacturing, quality systems, QRM, and process validation. In 2008, Irwin joined Novo Nordisk, focusing on quality roles and spearheading initiatives related to QRM and life cycle approaches to validation. Subsequently, he transitioned to the Merck (DE) Healthcare division, where he held director roles within the biosimilars and biopharma business units. In 2018, he became a consultant concentrating on enhancing business efficiency and effectiveness. His primary focus involves building process-oriented systems within CMC and quality departments along with implementing digital tools for knowledge management and sharing.