Identifying cGMP Issues Caused By "Management Problems"
By Joanna Gallant, owner/president, Joanna Gallant Training Associates, LLC
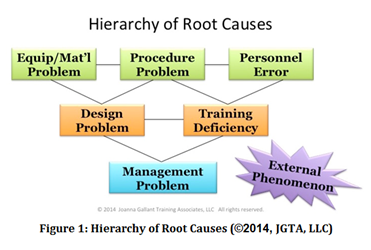
I’ve noticed an interesting trend in identified root causes of cGMP issues across a variety of companies, small and large, borne out in my root cause analysis webinars and courses. Using the hierarchy of root causes (Figure 1), I ask two questions and get the same answers—every time:
- Which is the most frequently identified root cause? It’s always “Personnel Error” (used for anywhere from 25-50+% of root causes!).
- Which is the least frequently identified root cause? It’s always “Management Problem” (used for <10% of root causes). Some companies don’t even include management as a cause!
So why do we see so many “Personnel Errors” and so few “Management Problems?” Managers are people too and should therefore be just as prone to making an error as an operator. It begs the question: Do managers truly make so few errors in comparison, or are we not correctly identifying situations as “Management Problems” when they occur?
What’s The Difference?
The table below lists different types of issues we might see in root causes related to both operators and managers:
Personnel Error |
Management Problem |
|
|
(Source: Department of Energy “Root Analysis Guidance Document”, DOE-NE-STD-1004-92, Appendix A)
“Personnel Errors” are pretty straightforward and relatively simple to identify when they occur. They typically happen when someone isn’t paying attention or makes a mistake. There also is usually an easily identifiable, maybe even immediate, effect of the error.
“Management Problems,” however, aren’t quite as easy to identify when they happen, and their effect usually isn’t immediate. It typically requires time for a situation to play out or for someone else to make an error for the problem to become noticeable.
Identifying “Management Problems” Requires Time
One potential reason why we don’t identify “Management Problem” root causes very often may simply be because the effect of the problem isn’t immediately obvious. Managers make choices and decisions that direct operations for the future, based on the information they have at the time. Errors or problems in the decision-making process lead to issues that play out when those futures come to pass—weeks, months, or even years after making the decision.
For example, with “Inadequate Resource Allocation,” it takes time for the inadequate resourcing to stress the current situation/environment. There is a time delay between the problematic allocation decision and when its effect is noticed. Picture a staffing decision that cuts personnel, leaving too few resources for the required work, which leads to errors or shortcutting to meet timelines. Or maybe it’s decided to not use financial resources to upgrade a facility and to allow equipment to run to failure rather than replace it. Eventually, the equipment fails, impacting production and/or product quality if no qualified backup systems are available.
Consider these staffing examples from FDA warning letters and 483 observations:
- You failed to provide an adequate number of qualified personnel to perform and supervise the manufacture, processing, packing, or holding of each drug product. Specifically, during an interview, the Quality Manager stated that investigations are often not conducted due to a lack of personnel. (2014 warning letter)
- There are an inadequate number of personnel conducting and reviewing complaint investigations at your firm, as evidenced by the lack of review of critical complaints as required procedurally and by the fact that, once the deficiencies were discovered, you brought in outside assistance to conduct the reviews, which should have been done by your QA staff. (2011 483)
These examples allude to a couple of different management issues that, combined, may have led to the problems cited by the FDA:
- First, it appears that staffing decisions—maybe to not hire personnel or to allow for vacant positions to be eliminated, for example—were made without considering all of the tasks that must be performed for cGMP compliance. If the company had a matrix of tasks required and who performed them, they could have identified that critical activities were unstaffed and therefore could not be performed.
- Subsequently, the failure to complete the tasks appears to have gone unnoticed. Had metrics of identification/closure rates been presented in ongoing management reviews, it might have shown that complaints were being received but not closed, investigations were identified as needed but were not progressing, and more. Had those trends been seen, good practice would have been to identify why they were happening, realign staff to deal with these areas, and then monitor going forward.
Identifying “Management Problems” May Require Other Issues To Highlight Them
Another potential reason for identifying so few “Management Problem” root causes may be because the problem leads to someone else making a mistake—an operator, perhaps. At that point, we usually identify the operator’s error and focus the investigation to why the mistake occurred. Only then can we identify that the mistake resulted from a “Management Problem,” assuming our root cause analysis is good enough to get us to that underlying root cause.
One place this may be seen is when a situation arises and the operator reacts inappropriately or makes a decision they weren’t qualified to make. Initially, these look like a “Personnel Error,” but further investigation identifies that the operator needed direction and their supervisor wasn’t available, which left the operator to decide what to do without appropriate guidance. In this situation, the supervisor failed to provide adequate oversight. (Operators should be trained and qualified to perform tasks and handle common issues and problems; however, training cannot address every possible situation that could occur and how to handle them, which is why supervisory oversight and guidance is needed.)
Other problems may occur when:
- Expectations aren’t set or communicated appropriately. As a result, the operator works without fully understanding what is expected and makes what they believe is an acceptable decision. Had they understood their management’s expectations, the operator could—and likely would—have made a different decision.
- A policy changes and not enough information is provided on what it means in the work environment. Or it doesn’t get communicated to specific groups of people who continue status quo operations until an error is identified.
- A policy is violated, and the manager doesn’t enforce it. Letting policy violations slide—even for good employees—compromises the integrity of the manager, and it doesn’t help employees to understand performance expectations. As examples, this situation may happen if managers are not familiar enough with policies/practices, or if they don’t have personnel management skills and shy away from difficult conversations.
These situations, and others, can also be found in FDA Warning Letters. For example:
- Your management failed to prevent the practices of product sample retesting without investigation, and rewriting and/or omission of original CGMP records persisted without implementation of controls to prevent data manipulation. (2014 FDA Warning Letter)
- An employee performing a demonstration of the bubble point test inside the clean room was observed with their hairnet improperly donned, exposing ~15 inches of hair to the environment throughout the demonstration. The supervisor did not instruct the employee to correct the deficiency until the demonstration was completed, after FDA personnel brought it to his attention. (2012 FDA Warning Letter)
- Your QA Manager stated investigations are not conducted unless requested by the client. However, your firm's SOPs state that an investigation must be performed whenever a client's sample results are outside of the stated specification. (2010 FDA Warning Letter)
- Your response suggests that: 1) your training is ineffective; 2) the procedure is not readily available; 3) the procedure is not understood; or 4) your personnel are not qualified to perform their functions. Please comment on how your leadership will ensure that your firm's procedures are fully followed to achieve an acceptable level of compliance. (2009 FDA Warning Letter)
How To Identify Situations As “Management Problems”
Identifying issues like these require a robust root cause analysis program. Investigations must identify the true root cause of the problem—the underlying cause, not just the direct cause of the specific event. Again, the 5 Whys approach discussed in my previous article is a useful practice to help ascertain the underlying cause of the problem.
Use the 5 Whys to identify the root cause of the problem by working through the levels of the Hierarchy of Root Causes presented earlier in the article (Figure 1). As the “Why?” questions are posed, push down to the most reasonable level of the hierarchy. The key to identifying “Management Problems” is to work through the analysis—they typically won’t be the first thing you see.
For example, if we perform a 5 Whys analysis on one of the previous FDA warning letter observations—just from what we know—it might go like this:
- Your QA Manager stated investigations are not conducted unless requested by the client. However, your firm's SOPs state that an investigation must be performed whenever a client's sample results are outside of the stated specification:
- Why is there a difference between the manager’s explanation and the SOP? Based on what we can glean from the observation, let’s say the manager wasn’t familiar with the SOPs.
- Why might the manager not be familiar with the SOPs? It’s possible they weren’t included in his training curriculum.
- Why might they have not been included in his training plan? It’s possible his manager overlooked them when developing or assigning the training curriculum for the position.
This could then be categorized as a “Management Problem” and subcategorized as “Policy Not Adequately Disseminated: Individuals who needed to be aware of these SOPs were not properly informed of their existence and content.”
You’ll likely be tempted to call this a “Training Deficiency,” but it’s not. Following our 5 Whys, it’s not a case where training failed because we didn’t know the person needed the training. We didn’t know this because of a “Management Problem” where the policy existed but wasn’t assigned to all who needed to be aware of it. Something that needed to be put in place wasn’t and led to the other issues.
Once you start down this path of asking “Why?” when situations occur, you’ll be quite surprised how many items may be identified as “Management Problems”—far more than the <10% most companies currently see.
Avoiding “Management Problems”
The best way to deal with these problems is to avoid them in the first place—by giving managers what they need to do their jobs. At a minimum, it requires:
- Emphasizing the importance of communicating expectations in a way that personnel can relate to them and apply them to their daily tasks
- Company leaders who set expectations and provide the time for managers to be on-floor with their groups in order to provide oversight and in-the-moment coaching and direction
- Appropriate oversight by all levels of the organization with a focus on successful performance of compliance-related activities, not just business results
- Making appropriate information available to decision-makers, such as a matrix of tasks or identification of compliance versus business needs, etc.
- Considering both short- and long- term risks in the decision-making process to evaluate possible decisions prior to implementation and identify the potential risks associated with each choice
- Contingency planning during the decision-making and implementation process, based on the risks identified in the evaluation process
- Providing training programs that develop “soft skills” required for personnel management, such as communication, coaching, and performance management processes and tactics, in addition to ensuring managers possess appropriate technical knowledge for their positions
Managing is a difficult job, and it becomes even more difficult if managers don’t have what they need to perform effectively. In this respect, managers are no different than operators. Where they differ is that “Management Problems” can and likely will be far more costly to an organization’s performance, if they are allowed to continue undiagnosed and unchecked. This can happen when “Management Problems” are not considered or identified during root cause analysis.