How To Implement Proper Gowning Procedures In An OSD Facility
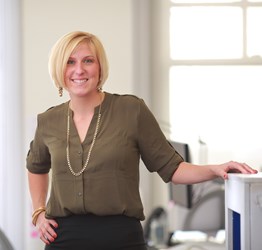
By Christine Hofnagel, AIA Associate, JacobsWyper Architects
Levels Of Exposure In OSD Facilities
Within an oral solid dosage (OSD) Manufacturing facility, there are typically three levels of product exposure: general, protected, and controlled. Generally, the division of levels is directly related to the product or product component exposure, as well as to the physical environment and function within the facility. These levels vary as many manufacturing processes differ from site to site. Within the industry, these levels are typically separated into categories, such as Level 1 (Black/General), Level 2 (Gray/Protected), and Level 3 (White/Controlled). The highest level of risk for product exposure is a white space, compared to a black space which has the least stringent protective parameters due to virtually zero product exposure.
An example of a “black” space would be a shipping and receiving loading dock for manufacturing, which is adjacent to a GMP warehouse. The product, material, or components are typically protected by an additional packaging layer surrounding the primary packaging or container with little to no risk of product exposure to the environment. An area, such as secondary packaging, could be considered a “gray” space because, while the product is not exposed, the primary package’s handling and physical environment can have an effect on the finished product. Finally, a “white” space would include weigh and dispensing rooms where product is directly exposed to the environment. The following article addresses specific gowning regulations that can be found in the three sites whose rankings are described above.
Gowning Requirements
The amount of contact with a product has a direct correlation to gowning procedures within an OSD manufacturing and packaging facility. Gowning is a subject that is addressed only by baseline documentation provided by multiple regulatory authorities. The following are excerpts from regulatory guidelines on protective clothing only, from different parts of the world.
- UNITED STATES: FDA: CFR – Code of Federal Regulations Title 21
- Sec.211.28 Personnel responsibilities: (a) Personnel engaged in the manufacture, processing, packing, or holding of a drug product shall wear clean clothing appropriate for the duties they perform. Protective apparel, such as head, face, hand, and arm coverings, shall be worn as necessary to protect drug products from contamination.
- EUROPEAN UNION: Eudralex, Volume 4, EU Guidelines for Good Manufacturing Practice for Medicinal Products for Human and Veterinary Use. Part 1- Chapter 2 Personnel
- Section 2.18 Every person entering the manufacturing areas should wear protective garments appropriate to the operations to be carried out.
- Section 2.20 Direct contact should be avoided between the operator’s hands and the exposed product as well as with any part of the equipment that comes into contact with the products.
- INDIA: CDSCO Good Manufacturing Practices and Requirements of Premises, Plant and Equipment for Pharmaceutical Products. (Schedule M) Part 1 Good Manufacturing Practices for Premises and Materials
- Section 7.6 Direct contact shall be avoided between the unprotected hands of personnel and raw materials, intermediate or finished, unpacked products.
- Section 7.7 All personnel shall wear clean body coverings appropriate to their duties. Before entry into the manufacturing area, there shall be change rooms separate for each sex with adequate facilities for personal cleanliness such as wash basin with running water, clean towels, hand dryers, soaps, disinfectants, etc. The change room shall be provided with cabinets for the storage of personal belongings of the personnel.
Although regulatory agencies provide manufacturers with some direction on how to protect drug product by means gowning and stipulated hygiene, it is clear that the exact procedure is ultimately left to the manufacturer as the decision-maker. Below are three gowning procedures developed by three major OSD manufacturing companies at one of their facilities, relating to the levels of exposure (black, gray, and white) for production personnel only. The exact process operation and/or specific drug product manufactured has been omitted from this discussion for simplicity.
- Company 1:
- BLACK: Street clothes or overgowned plant uniform with booties
- GRAY: Plant uniform, plant shoes, hairnet, beard covers, lab coat, booties
- WHITE: Overgown, booties, hairnets, beard covers
- Company 2:
- BLACK: Plant uniform and safety shoes (labs require lab coat over street clothes and safety glasses)
- GRAY: Plant uniform or lab coat, company safety shoes or personal safety shoes with booties over, hairnet (specific color), beard covers, gloves, safety glasses
- WHITE: Plant uniform, dedicated white space shoes, cover hairnet with duplicate hairnet (different color), beard covers, reusable jumpsuits over plant uniform, gloves, safety glasses
- Company 3:
- BLACK: Plant uniform, plant shoes, safety glasses
- GRAY: Plant uniform, plant shoes, hairnet, beard covers, safety glasses
- WHITE: Plant uniform, plant shoes, over gown, booties, hairnets, beard covers, safety glasses, nose & mouth covers (where applicable)
Comparing these companies shows a difference in typical gowning procedures within the same level of product exposure. One reason for these discrepancies between major OSD manufacturing companies’ gowning procedures could be the difference in architectural finishes or the location of the process within the facility relative to personnel flows.
For instance, some facilities may have linearly planned personnel flows that allow a more streamlined approach to gowning, such as only one layer of protective clothing. These linear flows may remove the necessity of overgowning or gowning twice to achieve the same level of protection. Overgowning or gowning and de-gowning repeatedly to get to the area of the plant where product is highly exposed can also be due to existing physical constraints of the facility. Since the regulatory agencies provide open-ended guidelines on gowning requirements and physical environments, the decision of how to handle operational procedures and gowning can be based on a risk-assessment program.
Risk Assessment To Help Achieve Appropriate Gowning Needs
It is unlikely that regulatory agencies across the world will be able to standardize guidelines for the physical environments in which drugs are exposed and for the gowning procedures required, due to infeasibility and lack of consistent control. Alternatively, informed decisions can be made using quality risk assessments that are based on scientific knowledge. This can lead to standardization of expectations throughout the industry.
In order to help standardize manufacturing/packaging environments of drug product, a quality risk assessment program should be implemented. On the issue of gowning specifically, risk should be systematically evaluated as it pertains to drug exposure.
Points to consider are as follows:
- Exact type of drug manufactured
- Specific task within the manufacturing process
- Physical environment surrounding the process
- Personnel safety and protection surrounding the exposed product or product component
The ICH Harmonized Tripartite Guideline – Quality Risk Management Q9 offers guidance on how to execute and apply quality risk management within multiple aspects of pharmaceutical quality using examples of successes and failures. This guideline has been recommended for adoption by regulatory agencies such as the European Union, Japan, and the United States in order to help provide clarity on this matter.
Below are the Q9 Principles of Quality Risk Management:
- The evaluation of the risk to quality should be based on scientific knowledge and ultimately link to the protection of the patient; and
- The level of effort, formality, and documentation of the quality risk management process should be commensurate with the level of risk.
Decision makers should:
- Take responsibility for coordinating quality risk management across various functions and departments of their organization; and
- Assure that a quality risk management process is defined, deployed and reviewed and that adequate resources are available.
In conclusion, if a manufacturing company uses a quality risk assessment plan to develop and implement gowning procedures, if it observes continuous operational controls, and if regulatory audits are performed, the result should be a safe and responsible environment in which drugs are produced.