Quality Culture Tips From Pharma Pros
By Ken Congdon
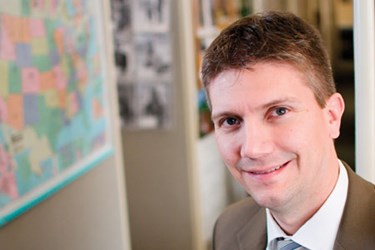
In my last column, Pharma’s Quest For Consistent Quality, I analyzed some of the preliminary findings of the International Society for Pharmaceutical Engineering’s (ISPE’s) Quality Metrics Pilot Program that were presented at the association’s recent summit in Baltimore. One of the key messages stressed throughout the summit was how important corporate culture is to achieving quality outcomes.
For example, much of the data collected throughout the pilot showed a direct correlation between cultural scores and site performance on key quality metrics. To reiterate, specific findings showed that:
- Stronger culture is correlated with fewer action limit excursions in steriles
- Stronger culture scores are associated with higher lot acceptance
- Sites with higher quality culture scores have lower deviations recurrence
- Sites with higher quality culture scores have higher Corrective Actions and Preventative Actions (CAPA) effectiveness
With this data at hand, it’s no wonder why creating a corporate quality culture is central to not only ISPE’s Quality Metrics initiative, but it’s Drug Shortages Prevention Plan as well. But, what exactly exemplifies a “corporate quality culture?” Well, according to ISPE, it’s when an organization is designed to foster cross-functional ownership of quality so that it is not viewed as a hindrance for success, but an absolute necessity for the company to collectively make decisions that best benefit business operations and patients. In other words, much like the old proverb “it takes a village to raise a child,” ISPE believes it takes a village (or multiple departments and employees) to ensure quality outcomes in pharma.
Merck & Perrigo Executives Speak Out On Quality Culture
Several keynote speakers at the ISPE Quality Metrics Summit reinforced the corporate quality culture message and shared their own approaches for creating an environment of shared quality ownership among all employees. For example, during his opening keynote titled The Importance of Quality Metrics to Manufacturing Performance, Willie A. Deese, Executive Vice President and President of Merck & Co., stressed how a direct connection between the shop floor and executive management is crucial to producing a safe, complaint, and reliable drug supply.
Deese outlined several of Merck’s escalation procedures for quality control and process change. He also stressed the importance of strong enterprise-wide leadership to enhance overall quality performance.
“At Merck, we believe that strong leadership can and should come from any employee,” said Deese. “Therefore, all employees — regardless of their level or function — have ownership and accountability for quality and compliance.”
Another presentation by Louis Yu, PhD, Executive Vice President of Global Quality for Perrigo focused entirely on the importance of quality culture in pharmaceutical manufacturing. Yu’s message also stressed that a quality culture is every employee’s responsibility. Moreover, he believes that this culture is the result of collective learned behavior and instilling a shared belief and value system in all employees.
Yu encapsulated this philosophy in a three-step process that drives Perrigo’s quality initiatives:
- All Perrigo employees must first look in the mirror. Are we communicating our quality principles and modeling ideal behaviors to all of our employees?
- Do we have the wisdom and the courage to act appropriately when metrics are trending in the wrong direction to maintain and sustain quality capabilities?
- Repeat steps 1 and 2.
Quality Culture Best Practices
For example, the Kaizen philosophy stresses the real experts in any organization are the people actually doing the work each day, and these employees should be intimately involved in improving their workflows and the quality of the products they produce. Kaizen strives to not only include every employee in process improvement initiatives, it actually puts a structure in place that empowers all workers to implement certain changes related to their jobs. This approach is often viewed as being more effective than funneling every request up-line for approval from executive management.
Respected business journals, such as the Harvard Business Review (HBR), have also dedicated time and effort into identifying the key characteristics of a culture of quality. For example in its April 2014 issue, the HBR published results of a survey it conducted that identified four essential attributes that predict a culture of quality. These attributes are as follows:
- Leadership Emphasis
- Message Credibility
- Peer Involvement
- Employee Ownership.
Moreover, HBR authors Ashwin Srinivasan and Bryan Kurey offered some clear actions that can help companies improve in each of these key areas:
- Maintaining a leadership emphasis on quality — Even when executives have the best intentions, there are often gaps between what they say and what they do. As a result, employees get mixed messages about whether quality is truly important. Company leaders must first buy into quality improvement initiatives and clearly demonstrate their own personal commitment to this effort to employees.
- Ensuring message credibility — Most companies energetically promote messages about the importance of quality, but their efforts are often wasted if these messages aren’t believed. Quality messaging should be tailored in such a way that it resonates with every employee. Different messages may need to be developed to resonate appropriately with employees at different sites. For example, emphasizing reduced costs or defect-free goods may inspire a team at one site, while stressing patient satisfaction may hit home with employees at another. The key is to regularly test these messages with employees, solicit their feedback, and refresh these messages over time if necessary.
- Encouraging peer involvement — Fostering peer engagement is a delicate balancing act. If leaders become overly involved in orchestration, then impact and authenticity may suffer. On the other hand, if they show too little support, they could miss important opportunities. A variety of different tactics can be used to create positive social pressure that encourages employees to participate in (and even generate) quality initiatives. These can include friendly “quality competitions” that may or may not include financial incentives or public recognition of employee quality initiative contributions to the company. Again, the key is to test these tactics and solicit feedback to see which are most effective with your employees.
- Increasing employee ownership and empowerment —As discussed throughout this article, one of the defining traits of an organization with a true culture of quality is that employees are free to apply their own judgment to situations that fall outside the common directive. Providing the right level of guidance is crucial to this effort. Too much guidance stifles creativity and discretionary action, while too little leaves employees unclear about their decision-making authority. Creating formal written quality guidelines can go a long way to outlining the company’s quality expectations. These guidelines can also provide employees with an instruction manual for how to act when they encounter specific quality issues.
It’s undeniable that corporate culture and pharmaceutical quality are linked. And, many of the principles of creating a culture of quality aren’t rocket science. However, not all pharmaceutical manufacturers dedicate the time and effort necessary to make this important cultural shift. In the end, it all comes down to execution. So, when it comes to your own manufacturing operations, can you pass this three-part test?
- Do your company leaders not only stress the importance of delivering a quality product, but reflect that mantra in their own day-to-day job functions?
- Does your organization clearly communicate quality-focused messages that your employees take to heart?
- Does your company encourage peer involvement in quality efforts and empower its employees to initiate change for the sake of quality improvement?
What anecdotes or examples illustrate how your company excels in each of these areas? Please submit them in the comments section below. By sharing collective best practices for building a pharmaceutical corporate culture focused on quality, we can help drive our entire industry forward.