Quality Systems 101: Basic Concepts & Considerations
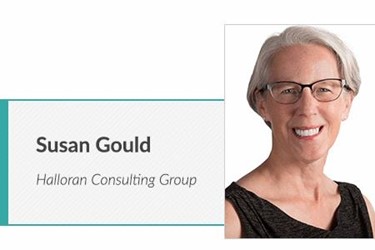
By Susan Gould, Halloran Consulting Group
Whether you are a life science startup with a brick-and-mortar office or working as a virtual company, at some point the question comes up: Do we need a quality system? Or perhaps your question is, What is a quality system? In an effort to answer both of these questions, this article will:
- Outline the basic concepts of a quality system
- Define when to consider adding a quality system and quality resources
- Describe how to scale your quality system for your stage in development
Quality Systems in a Nutshell
A quality system can be defined as the organizational structure, responsibilities, processes, procedures, and resources needed for ensuring the quality of products and consistency of delivering services to customers. In regulated industries like the life sciences, this includes ensuring the integrity of data provided to agencies responsible for reviewing the safety and effectiveness claims of a product, and ultimately the granting of approval to market a new drug, biologic, or device.
It helps to break this definition down into individual topics. The quality system can be seen as covering the following:
Organizational Chart
The organizational chart demonstrates that the organization has the structure and resources needed to ensure consistent and compliant deliverables. The structure and resources are determined by the type of organization, the goals and objectives of the organization, and the stage of product development. Each role identified on the organization chart should have an associated job description.
Job Descriptions
A job description is a summary of expectations the organization has for each role within the company. This typically includes an outline of the type of experience, skills, training, and education determined necessary to perform the function. It also summarizes the nature of the tasks the employee will conduct. These are often developed by functional leaders, maintained in human resources files, and utilized by hiring managers to identify the appropriate job candidates.
Standard Operating Procedures (SOPs)
The ICH Good Clinical Practice (GCP) guideline defines SOPs as “detailed, written instructions to achieve uniformity of the performance of a specific function.” Simply put, SOPs specify in writing who does what and when, or the way to carry out an activity or a process. For an activity to become the topic of an SOP, it must be either subject to regulations or address a key component of the quality system.
Standard Templates
A template document is a tool that supports SOPs and facilitates a consistent recording or presentation of information expected by the organization. These may be in the form of checklists, tracking logs, signature approval forms, reports, or specific language that must be utilized in order to demonstrate compliance with SOPs.
Training and Qualifications
All personnel should have documentation of the necessary experience and training to ensure they can perform the tasks assigned to them. There are three components to this requirement: 1) defined training requirements and documentation of the requirements being met, 2) defined tasks, often detailed in a job description, and 3) demonstrated experience, as documented in a resume.
Continuous Improvement
A quality system should continuously improve and mature with the organization. Two key ways to ensure ongoing improvement of the system are auditing and learning from mistakes.
Auditing is the process of evaluating your internal processes and documentation. It allows the organization to understand where improvements are needed and where processes may either be inadequate, overly complicated, or not feasible as described. Audits should be conducted by someone independent of the area being audited. For small companies, this can mean using a contact auditor; Larger companies typically have a department who will manage this process.
A corrective action and preventative action (CAPA) process is a formalized way to record deviations to SOPs (i.e., mistakes, errors), to understand the reason for the deviation and then put corrections in place to prevent future issues. A CAPA process demonstrates the organization’s commitment to learning from mistakes and continuously improving.
Management Review
Management review is a formal process for reviewing the quality system on a periodic basis. The review includes an assessment of performance indicators — such as audit findings, CAPAs, training compliance, SOPs, and resourcing. It is also used to ensure processes remain relevant and continue to reflect expectations as the organization evolves and new regulations and practice guidelines emerge.
The above basic aspects of the quality system are often described in a quality manual. The quality manual is a roadmap describing how your organization defines and ensures quality.
The Right Time to Implement a Quality System and Quality Resources
Early-stage companies may consider themselves to be outside of the regulated environment and therefore without the need for a quality system. However, if any of the data being generated during these early stages of product development are likely to be used for a regulatory submission, it might be time to consider implementing a quality system.
Certainly, as soon as the organization moves from basic research into a regulated environment — where GxP compliance is required — a quality system and quality resources must be considered. GxP is an acronym referring to any or all of laboratory, manufacturing, and clinical regulations encompassed under good laboratory practices (GLP), current good manufacturing practices (cGMP), and good clinical practices (GCP).
If your end-game is to seek a potential partner for funding down the road, having a quality system in place sooner rather than later may be a key to success. A defined quality system demonstrates a commitment to quality and compliance to GxP, lowering the potential risk for potential partner companies.
Implementing a quality system does not necessarily require the addition of quality resource(s), but the two often go hand in hand. Consultants can often fill in the gaps by providing on-demand support and offering assistance with developing any of the components of the quality management system (QMS). At some point, however, it makes financial and logistical sense to hire an internal quality resource who can take ownership for the system. The qualifications of that resource will vary depending on the needs of the company. At the very least, quality resources should be well-rounded and able to provide oversight of all aspects of the quality system.
Scaling the Quality System to your Stage of Development
As a startup, your needs are quite different from a mature company. Very likely, you outsource some or all of your GxP activities. You run a lean organization and require a flexible quality system. With that in mind, below are some suggested components for your quality system.
- Quality manual and organizational chart (the org chart may be part of the quality manual)
- Job descriptions
- Outline the expectations for each role identified on the org chart that has responsibilities listed in any of the SOPs
- SOP development and control
- SOP on how SOPs are developed, version controlled, reviewed, approved, revised, and obsoleted
- Template SOP to ensure consistency across all SOPs
- SOP files (electronic or paper) to ensure only current, approved SOPs are available for reference
- Vendor/supplier oversight
- SOP on vendor/supplier selection, qualification, and management
- Quality agreements that clearly state compliance requirements expected for each vendor/supplier
- Vendor oversight plans for each vendor, describing the steps taken to review and approve all vendor deliverable
- Vendor/supplier files capturing all aspects of selection, qualification, and oversight
- Training
- SOP on defining and documenting training requirements
- Training file on each employee, including resume, job description, and evidence of training on SOPs
- Audits
- SOP on the conduct of vendor audits and internal audits
- Audit file containing auditor credentials (CV of contract auditor) and completed audit reports
- Management review
- Documented periodic reviews of the quality system. Including a review of the quality manual, vendor files, and training — could be a PowerPoint presentation or a simple memo describing what was reviewed, who was part of the review, and any action items
Small organizations will typically outsource much of the regulated activity to vendors and service providers such as contract development and manufacturing organizations (CRO), and it is acceptable to delegate those tasks being conducted by them under their SOPs. However, you remain accountable for your product’s development. Therefore it’s essential you select qualified vendors with the experience and quality system that will achieve your objectives and satisfy GxP and regulatory expectations. A plan or SOP that documents your involvement and oversight is equally important, even at this stage of development.
As your organization grows and matures, additional components will need to be added. SOPs for any tasks brought in-house (e.g. the writing of clinical study protocols) will need to be developed. As more GxP work is brought in house, a CAPA system should be implemented to document and correct any noncompliance.
So how do you know what you need? A gap analysis is an excellent vehicle for understanding what needs to be put in place now versus down the road. A gap analysis is a risk-based assessment of the quality system taking into consideration the stage of development, the company size, the current and planned outsourcing model, and the regulatory pathway. Often done by a third party, the gap analysis includes a review of existing SOPs, audit files, vendor files, training files, management review documentation, and any CAPAs (if applicable).
In addition to document review, interviews are conducted with key staff to understand the current and future needs of the organization and any perceived (or real) compliance gaps or concerns. The output of a gap analysis is an independent assessment of the quality system with prioritized action items to address any current gaps or potential misalignment with future goals and objectives for the company.
Conclusion
There is no one-size-fits-all when it comes to quality systems. Each organization must assess what is appropriate for them based on development stage, goals and objectives, and acceptable risk. Quality systems should be seen as iterative rather than static. An ongoing cycle of review, revise, and adjust is necessary to continuously improve and grow the quality system with the organization. Furthermore, planned external reviews of the quality system in the form of audits and/or gap analyses can offer an essential critical evaluation of your quality system and ensure it is appropriate for your needs.
About The Author:
Susan Gould, a principal consultant at Halloran Consulting Group, joined the company in 2015. She brings over 20 years of experience in the medical device and pharmaceutical industry. Her career has focused on clinical quality, compliance, and technical execution, including quality systems regulation (QSR), Phase I-IV clinical trials, and human factors evaluations.
Prior to joining Halloran, Susan held senior-level global positions at Baxter and Boston Scientific, both in clinical and medical affairs, where she supported the development of device and drug-device products. Susan started her career in the pharmaceutical industry, taking multiple products to market.
Susan holds a master's in business administration from Lake Forest Graduate School of Management, with advanced certification in business analytics and strategy development, as well as a master's degree in clinical microbiology from Thomas Jefferson University and a bachelor's degree from Mount Holyoke College. She is certified in quality systems from AAMI.