The Role OF The FDA And Patient Safety In Aseptic Liquid Dose Packaging Systems
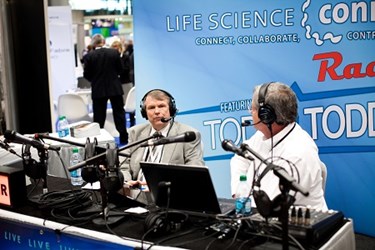
Chuck Reed, VP of Weiler Engineering recently sat down with our editorial team to discuss blow-fill-seal packaging technology at INTERPHEX 2014. “The FDA is totally focused on patient safety so there is a big focus on risk management in the industry right now. It goes with our technology again because our machines operate with no human intervention” says Reed. Weiler Engineering is America's leading provider of aseptic custom packaging for pharmaceutical and healthcare applications. Weiler Engineering’s focus is to provide the most advanced aseptic liquid processing technology available through the application of customized ASEP-TECH® Blow/Fill/Seal machinery and integrated services. Chuck Reed is a past chairman of the ISPE Packaging COP.
Get unlimited access to:
Enter your credentials below to log in. Not yet a member of Pharmaceutical Online? Subscribe today.