Top Single-Use Suppliers Make Standardized Equipment A Reality – Part 2
By Trisha Gladd, Editor, Life Science Connect
In Part 1 of this article, I spoke to Dave Wolton, biotechnology consultant at PM Group, about his company’s project to offer standardized single-use equipment through the websites of some of the top single-use suppliers in the industry. Luke Heaven, director of marketing for fluid management technologies at Sartorius, and Mark van Trier, owner and director of JM Separations BV, discussed their thoughts on the benefits of this project to both suppliers and users, as well as how it addresses some of the biggest objections to equipment standardization. In Part 2, Jeff Johnson, new technology lead at Merck, and Guido Ragetlie, a principal scientist at Janssen Biologics, offer insight from the eyes of a user.
A User’s Point Of View
Currently, PM Group is receiving a user’s perspective on the project beta testing of the JM Bioconnect website, which both Merck and Janssen are both open to participating in. Ragetlie thinks this concept could greatly reduce the planning and ordering phase of facility design. “I see the advantage to having these drawings readily available,” says Ragetlie. “While you would normally start sketching these on paper, and at that time, your questions to the vendor are less clear, this would allow you to ask questions about price and delivery at a very early stage.” When PM Group’s first introduced their project to Johnson, he thought the project had potential and was “the most concrete and the most progressed” of the standardization efforts he’d seen.
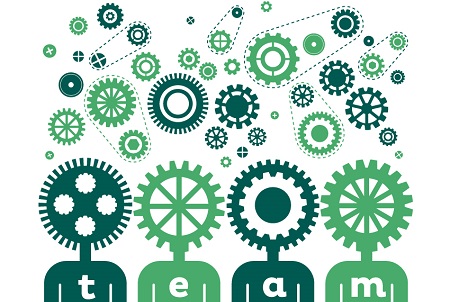
Johnson says one of the benefits of this solution is that suppliers would be able to automate the production of their assemblies, which would lead to higher quality connection technologies at a lower cost, such as molded assemblies. “Currently, we do it with hose barbs and tie wraps, which can lead to leaks,” he explains. “Molded assemblies are a higher quality, but at this time, they’re quite expensive. If we standardize, suppliers could automate them and bring that molded cost down, so you could get higher quality, lower cost, quicker turnaround times, and lower inventory.”
Additionally, Johnson says if there is standardization on some of the more mature technologies, it would enable suppliers to stock instead of make to order, which would reduce lead time and internal inventory levels. Ragetlie adds, “When you reduce your stock, you are no longer required to manage all of those parts. And the more efficient your process, the better it is for you.” Heaven says about the benefit to the user, “The same way it backs our ability to manufacture, it impacts theirs as well. It optimizes stock control and inventory management, because if you’re using 10 references as opposed to 100, you can have a much better stock control process that keep your security supplies in place for the manufacturer. It also helps with their ability to tech transfers, including those done internationally,” he says. “It’s much easier if the all the validation and extraction work has been done, and they’re using standardized references globally. Of course, the most important is cost. We can bring in more automation, so that means products become cheaper but also less risk of variation during manufacturing. It becomes much more industrialized.”
Johnson says he sees value in what Wolton is doing, but the perspective of other experts will need to be considered. “He (Wolton) is able to cover the engineering aspects of it so that he can design and build facilities quickly, and I think operating companies, like Merck, could include additional requirements around quality and validation and perhaps even around operability, as well as offer some input on the designs.” Johnson explains he still needs more information about the project before Merck can endorse it, but he adds there are additional meetings scheduled in the future between PM Group and Merck to discuss what that information is.
Ability To Innovate Still Exists
In regard to the concern about standardization taking away the supplier’s ability to be innovative, Johnson says the idea of standardization does not mean a standardization of the equipment that still requires innovation. “I’m not proposing we standardize things like bioreactors or purification equipment,” he notes. “There are many aspects of single-use technology that are quite mature, such as single-use bags and connection of the bags together, assemblies, and manifolds.” He continues, “Most people are worrying about their project, their building, their local problems, and their own firefighting and can’t take a long-term strategic view of this. Therefore, they see little value to standardization, because they’re only thinking about their existing facility, where it would be difficult to retrofit these standard assemblies. However, they’re missing the future value.”
As it stands today, Wolton intends for over half of the suppliers to have the standardized equipment available to existing and potential customers this year. Long term, Johnson says PM Group’s solution could fit into the existing approach Merck is taking to single-use standardization. “Right now, we’re developing our own standard assemblies with a modular approach, where you can click them together like plug and play,” he explains. “In the past, we’d make these custom assemblies that were quite large and quite complex and caused several issues. Now learning to break those down into smaller parts, which is a little counterintuitive because you have to pay for the extra connections and each additional connection increases the risk of a leak. We’re finding though that we can competitively bid those smaller components to the appropriate vendors and have examples of tremendous savings doing so.” With this approach in mind, Merck’s Single Use Network (SUN) is developing an internal catalog of best practice assemblies selected from throughout the Merck facilities worldwide. They want to deploy this and hope to do it this year so that people from all sites can pick from the already existing best designs, rather than the typical approach of going through their local sales rep for a new custom design. He says PM Group components could be added to that catalog.
While there are many in support of this project, skepticism naturally exists. Questions have arisen around the process of ordering parts online as well as the long-term involvement of PM Group, as some feel this is in an issue that should ultimately be solved between pharmaceutical users and suppliers; however, as more suppliers and end users get involved, this project as it stands now will finally offer the ability to see how standardized single-use equipment plays out. And while there may be bumps along the way, this might be the step in the direction everyone has been waiting for.