High Shear Mixers for Pharmaceutical Processing
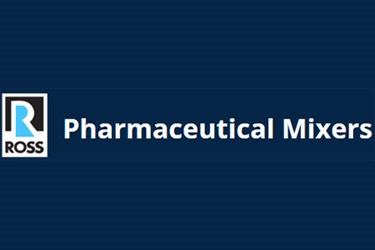
Ross manufacturers the world’s broadest line of rotor/stator Pharmaceutical High Shear Mixers.
Included are traditional single-stage designs to the new generation of patented ultra-high shear X-Series and MegaShear mixers.
In stock for fast delivery - purchase or rental
Ross maintains the world’s largest inventory of batch and in-line mixers - new and used, fully warranted, and ready to ship when you need them.
Your choice - Batch or Inline?
The first step in specifying the right mixer for your application is to decide between a batch or continuous inline system. Each type of system offers a unique set of advantages, and the engineers at Ross will help determine which one will provide the most efficient and economical solution for you.
Batch mixing
Batch High Shear Pharmaceutical Mixers can be permanently mounted to the mix tank or suspended over the vessel with a portable lift. The mobile configuration offers you the flexibility to use a single mixer in multiple vessels. It also allows you to vary the position of the rotor/stator generator in the vessel to fine-tune the process to handle a variety of materials. For many applications, the batch design produces fast particle size reduction and short mixing cycles, but only if the flow pattern within the vessel is optimized. The rotor/stator generator of the batch High Shear Pharmaceutical Mixer is generally positioned 2-3 head diameters from the bottom of the vessel, and slightly off-center. To promote adequate circulation with heavier solids, the rotor/stator generator may be located in the center of the vessel.
In-line mixing
Whether your system is set up for single-pass mixing or multiple passes with recirculation, the inline mixer allows you to produce an end-product with a predictable particle size distribution and outstanding reproducibility. Because the in-line system is closed, it also minimizes problems caused by air entrainment during processing. Especially when mixing material in large volumes, the in-line mixing system is extremely cost-efficient. Unlike a batch mixer, which requires a high-horsepower motor to generate adequate circulation in a large vessel, a small in-line pharmaceutical mixer can handle a 25-gallon batch as easily as it handles a 250-gallon batch. As the vessel size increases, the energy required by the in-line mixer remains low - while the savings grow.
A Ross High Shear In-line pharmaceutical mixer is versatile choice for process lines that require frequent changeover from one product to another. A simple valve can divert finished product downstream or switch instantly from one source vessel to another.
Single-stage rotor/stator mixer
All rotor/stator pharma mixers are comprised of a rotor that turns at high speed within a stationary stator. In a “single-stage” unit, the rotor includes a single set of four blades. As the rotating blades pass each opening in the stator, they mechanically and hydraulically shear particles and droplets, and expel material at high velocity into the surrounding mix. As fast as material is expelled, more is drawn into the rotor/stator generator, which promotes continuous flow and fast mixing.
Multi-Stage Rotor/Stator Mixers
Multi-stage rotor/stator generators include multiple rows of rotating blades that nest inside a matching stator. The mix material enters the center of the generator through an inlet pipe and is accelerated outward by centrifugal force. During each transit through the rotor/stator generator, the material is subjected to a quick succession of increasingly intense shearing events - until it finally exits the generator and is either piped downstream or recirculated for another pass through the mixer.
New technology for high speed powder induction
Powders like gums and thickeners are notorious for driving up processing costs. Even with a strong vortex in an open vessel, they resist wetting out and often float on the surface for an hour or more. Once they submerge, they often form agglomerates with a hard outer surface that is difficult and costly to break. Ross has developed new technology that enables you to mix and wet out powders almost instantly. Available in either a batch or in-line configuration, the SLIM (Solid/Liquid Injection Manifold) system injects solids directly into the high shear rotor/stator, where they are immediately pulverized and mixed with the liquid stream. The SLIM system accelerates the mixing process dramatically, while it virtually eliminates dusting – minimizing the volume of airborne particles released inside the plant atmosphere.