A Justification For Using In-Process Controls In Place Of Cleaning Validation
By BioPhorum
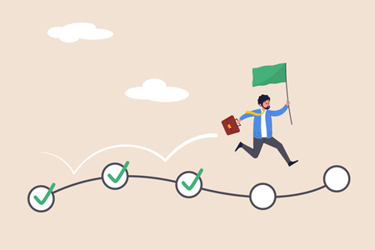
Column resins are typically dedicated to processing specific products, offering optimal prevention of cross-contamination. By association, column equipment and column packing equipment are also subject to multi-product questions. Column equipment must undergo cleaning validation for batch-to-batch cleaning and possibly for product-to-product cleaning.
Cleaning validation of the columns using a justified method or limit (based on maximum allowable carryover (MAC) calculations) that demonstrates product removal, and that is in line with the strategies employed with other multi-use/product equipment, has allowed column equipment to be shared across products. Some companies consider that equipment used to pack and unpack resins from different columns is multi-product and subject to cleaning validation.
However, this equipment should not be subject to product residues if certain procedures are followed and, therefore, does not require cleaning validation.
This article provides a procedure for using and cleaning shared columns and column packing equipment and using in-process checks and controls that eliminate the need for cleaning validation and ongoing revalidation or cleaning monitoring.
A risk-based approach to the validation strategy associated with this equipment may be employed that considers the equipment designation as product contact/non-product contact, residues the equipment is exposed to, function and frequency of use, and storage conditions.
Process Flow
The flow diagram in Figure 1 shows the typical procedure used to unpack a column and repack using either new or cleaned resin. In this process flow, new/naive/virgin resin (called “new resin” in this article) refers to any resin not previously used to purify product. Used resin is resin that has been used previously for purification. Cleaned resin is used resin that has been cleaned of previous product and made ready to use for the next batch or product campaign.
Figure 1: Process flow when a column is being unpacked to remove used resin and repacked using either new or cleaned resin.
Key: Cond – Conductivity, TOC – Total organic carbon
Step 1: Resin Cleaning
During manufacturing, the column is cleaned after each use. This is either validated cleaning or verified by taking post-cleaning samples that must meet established limits. Typically, after the last batch campaign ends, the same cleaning cycle is performed before column unpacking.
The chromatography column, resin, and wetted parts are all ”product contact,” and removing the process residue, bioburden, endotoxin, and detergent/cleaning agent is demonstrated based on the cycle being validated or by verification of the samples taken. Once these parts are clean, there is no expectation that the unpacking process will reintroduce product residue or contaminants.
The definition of “clean” includes that product contact parts have been sufficiently cleaned to acceptable levels of product residue, detergent/cleaning agent, and microbial control. These acceptance criteria have been determined to be appropriate for using the column to manufacture the next batch, including all required safety factors.
Step 2: Resin Unpacking
This step involves removing the “cleaned resin” from the column. Typically, this is in a controlled area or a “controlled not classified” area as a minimum. Removing residual resin may be done through automated or manual steps and should meet the criteria for visually clean. Residual resin from the previously packed resin bed, below the acceptance criteria for visually clean, does not pose a carryover risk.
If there is a process check that the column is visually clean of the previous resin and this check is recorded, the risk of resin carryover from the previously packed column to the column packing equipment or the newly packed column is low.
Step 3: Empty Column Cleaning
The chromatography column, resin, and wetted parts are all “product contact,” and the removal of product residue is demonstrated through the final cleaning before unpacking. Cleaning validation/verification of the packed column, using a suitable method and limit (based on MAC calculations) that demonstrate product removal and is in line with the same strategy applied to other multi-product equipment, allows this justification. Visual detection of residual resin is also performed at disassembly to ensure conformity.
After unpacking the column, preventive maintenance should be performed to replace parts like frits and seals. Other wetted parts should be replaced preventively. Companies should follow their post-maintenance procedures for cleaning and visual inspection.
Column packing equipment is considered indirect “product contact” as it only sees cleaned or new resin, cleaning agents, buffers, and detergents. Verification of the cleanliness of ancillary support equipment would include a visual inspection.
At this point, the “cleaned” resin has been removed from the column, reusable parts have been cleaned, other/ancillary parts have been replaced, and the entire empty column has been cleaned again. There is no risk of product residue carryover as there is no product to carry over.
Step 4: Packing The Column With Resin
When the empty column and packing equipment are clean, the column can be packed again with a new resin. Once the column is repacked, it will be cleaned again. This could be with a validated “clean in place,” verification sampling, or other justified means to ensure it is ready for the next run.
At this point, the resin and equipment are considered clean and the risk of any carryover to the column or column packing equipment is very low or nonexistent.
Risk Assessment
The need to perform cleaning validation on empty columns and column packing equipment should follow a risk assessment process. An example step is:
- Risk question: What are the risks (and mitigations) for not having cleaning validation in place on the empty column and column packing equipment cleaning processes?
- Concerns: Cross-contamination through product residue carryover, contamination from the resin itself, packing equipment contamination, detergent residue, and bioburden (e.g., clean and ready for use) could occur.
- Product residue carryover (product residue carryover/cross-contamination): The packed column is cleaned before unpacking the resin. The resin cleaning is either validated or verified through sampling. Therefore, the skid removes the clean resin. If there is no concern for product carryover batch-to-batch, there should be no additional concern for contamination of the column packing skid and equipment.
- Conclusion: The risk is low.
Other topics to be considered include resin contamination, packing equipment contamination, and microbiological contamination (bioburden, endotoxin). The answers will allow readers to arrive at an overall risk assessment conclusion.
Downstream Process Impact
The equipment surface area upstream of the last chromatography column represents minimal carryover risk due to multiple opportunities for the removal of cleaning residues through purification processing and may be excluded from MAC limit calculations.
Purification of biological products involves multiple separation and purification steps designed to remove process- and product-related impurities. Based on purification process capabilities, there are multiple opportunities to remove cleaning-related impurities through the last chromatography step.
Any product residue from a previous molecule would be exposed to caustic solutions and subsequently removed via multiple rinses and washes during the cleaning process. Also, any residue present after cleaning would be exposed to several removal steps before the final buffer exchange and concentration or ultrafiltration/diafiltration.
Based on the risk assessment and the justification and procedure for how the column is used and located in the process, not performing cleaning validation of column packing equipment can be supported.
Conclusion
Considering the risk assessment above, we can say that cleaning processes for empty chromatography columns, as well as ancillary column packing equipment, do not require cleaning validation. If sufficient in-process control measures are in place, the risk of cross-contamination (through product residue) and microbiological contamination is negligible. The overall risk of contamination is sufficiently mitigated through standard in-process controls and process steps.
This article summarizes some of the main points from a recent BioPhorum publication on this topic. To read more, check out the full paper, Changeover cleaning of empty columns and column-packing equipment — a justification for using in-process checks and controls in place of cleaning validation.