A Rapid, Low-Risk Approach For Process Transfer Of Biologics From Development To Manufacturing Scale
By Sebastian Ruhl, Naomi de Almeida, Melisa Carpio, Jens Rupprecht, Gerhard Greller, and Jens-Christoph Matuszczyk
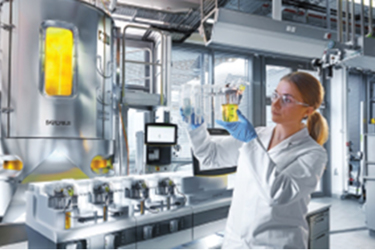
Successful scale-up of cell culture for manufacturing of biopharmaceuticals gives companies time to accelerate clinical development, product commercialization, and market access (1). Scaling a cell culture process in stirred-tank bioreactors ideally includes optimizing that process at laboratory scale and then transferring it through larger pilot-scale and finally to manufacturing-scale bioreactors (2). This is a complex, time-consuming business that can involve process transfer — sometimes to different geographical locations and through many sizes of bioreactors, each of which can operate according to different agitation principles and gassing strategies (3). Therefore, each scale might require several runs to obtain similar results, and optimization also might be required at the different scales.
One approach for overcoming several scale-up issues is to use miniature bioreactors for process development. In this study, BIOSTAT STR bioreactors with single-use FlexSafe STR bags (Sartorius) were used for the pilot- and manufacturing-scale single use bioreactors. They use proven and established design principles such as a top-driven, midpositioned stirrer and harmonized impeller and consistent sparger design across scales, with two impellers and a unique combination of ring spargers and microspargers.
Get unlimited access to:
Enter your credentials below to log in. Not yet a member of Pharmaceutical Online? Subscribe today.