A Road Map For PAT Monitoring And Control
By BioPhorum
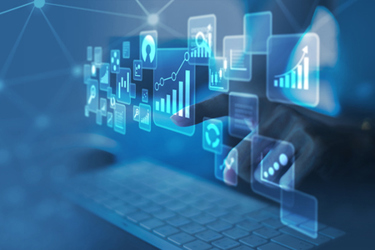
Process analytic technology monitoring and control (PAT MC) is rapidly progressing as instruments shrink in size and have faster signal acquisition times, analyzers account for more variables, and modeling becomes more machine learning-based. In this environment, it is challenging for pharmaceutical and biopharmaceutical companies to understand the ideal path to implement PAT.
PAT enables advanced process controls and quality by design, and it culminates in a well-understood process that ensures predefined quality attributes, which is a precursor for real-time release testing. Each organization, vendor, and technology will have its own challenges regarding data management, organizational structure, internal support staff/resources, and funding.
The road map outlined below:
- advises on the best practices to move from concept through life cycle management and/or regulatory approval of the PAT application
- highlights use cases for PAT MC and the benefits
- enables effective decision-making and scalability.
Building A Business Case
The rationale for implementing PAT can be based on speed and efficiency, risk mitigation, and ensuring process and product quality, which will be measured by return on investment. PAT MC will impact these business drivers by:
- providing greater process understanding and control of each unit operation
- increasing product output via real-time PAT MC and enabling continuous manufacturing
- eliminating human error via closed-loop control and electronic data.
The initial steps to building a business case are to identify specific pain points from current practice and the potential benefits of PAT. Two major benefits offered by PAT are improvements to process design and control via real-time detection and/or feedback control and supporting quality by design to improve process understanding. Implementing PAT could improve process development by providing additional data and control strategies resulting in improvements, e.g., increased titer or improved quality. In manufacturing, cost reductions are attainable via reduction of run failure, cost of goods, and skilled operator costs.
Implementation At Development Scale
The predevelopment stage starts with identifying a use case and the associated user requirements of the system. Refining the problem statement will ensure that proper technologies are identified to suit the use case. The technological solutions that meet these requirements can be compared or even evaluated in the lab against one another to determine a path forward. Key evaluation criteria include maturity of technology, fitness-for-purpose, cost of implementation, data management technologies, regulatory compliance, scalability, risk assessment, system life cycle management, and compatibility with current infrastructure.
Figure 1 shows the key stakeholders (primary decision makers) engaged to build the business case are process development, manufacturing, or a technology transfer sub-team and business strategy analysts.
Figure 1: Building a business case is a cross-functional exercise that requires a team
Implementation At Scale
When process development feels that a PAT method is sufficiently mature to migrate into a manufacturing space, a new cost/benefit guide should be built. This should consider the compatibility of the technology on a larger scale. It should also provide detailed insight into the comparability of the bench scale model to current quality data to ensure consistency of the process. A risk assessment generated by manufacturing subject matter experts (SMEs) may provide insight that the development group has not yet considered. A ranked list of mitigations in the risk assessment may help with the cost/benefit analysis. Finally, the cost of the core technology and the related costs associated with its operation in a highly regulated space should be forecast.
Development
PAT MC has proved to be an asset for defining and developing biopharma processes and will effectively reveal insights in a timelier and more cost-effective manner, as well as add to the robustness of the process, process characterization, and data packages.
Technology Comparison
A technology comparison will be conducted via investigation of available PAT and the business drivers. The organization will want to answer questions such as:
- What are the desired attributes to monitor and/or control?
- What are the business or strategy drivers?
- What instruments and technologies exist to achieve this?
Early Phase
The first step in developing a PAT is to define the application of the technology. Prior to developing a PAT, a comparison of similar PATs of different models or from different vendors should be conducted to assess technical feasibility and demonstrate business case benefit. This initial scoping may include preliminary tests in a scale-down environment to better understand performance capability and/or limitations. Once the specific vendor, maker, and model of PAT have been selected, the method should be clearly defined and developed further in scale-down models to provide a robust basis for proof-of-concept studies.
Mid Phase
As part of the PAT MC development, the “design of experiment” should incorporate studies to determine the statistical significance of the program, including:
- demonstration of the PAT MC capabilities, including impacts, identifying and mitigating adverse events
- assessment of PAT MC effect on process parameters, product quality, and performance indicators (PI).
Development data will be used to classify process parameters and in-process controls and establish the respective PAT MC effect. The development team will document the justification for parameter and control classifications, such as critical or noncritical. A summary of the control strategy (reflecting inputs, procedural, statistical, and model-based assumptions) will be created. These classifications will be made by advisors and support resources and endorsed by stakeholders.
Final Phase
The final phase of development is to support deployment and prepare an initial technology transfer package to manufacturing facilities. Standard tech transfer documents include:
- bill of material: A brief narrative description of each unit operation, including the step purpose and how the unit operation is to be run
- media, buffer and solution preparation information, including lists of raw materials, related concentrations, preparation methodology, and storage details
- chromatography column packing and membrane installation information with any associated process parameters and PIs.
Deployment And Engagement
The PAT MC program development will have assessed the in-scope PI, which is a direct or indirect measurement of a product quality attribute, product quality indicator, or process consistency measurement. The PI and PAT MC action limits should align and specify if:
- the PAT MC program will reduce the risks of specification failures and provide important information for process consistency
- the in-process control testing is required per regulatory expectations.
As this information becomes available during development, it should be discussed and analyzed extensively with the primary decision makers on the project team. The business case (project charter) should also mature as the project advances, accounting for the time, costs, and labor associated with the offline analytics that the PAT MC will replace. The result will be a well-vetted PAT MC platform that is nearly ready for implementation. Figure 2 summarizes the activities required for deployment and engagement.
Figure 2: Examples of development and deployment activities.
Key: IQ – installation qualification, OQ – operational qualification, PQ – performance qualification
Tech Transfer From Pilot Lab
Development phase activities typically occur in a less rigorously controlled environment than on a commercial scale. These activities may be conducted using vendor SMEs, company development staff, and vendor or temporary infrastructure, such as a local server. In this way, the resulting networking and digital robustness of the PAT MC will need to be shored up to allow for scaling up and regulatory scrutiny.
Digital Considerations
Another important aspect of a PAT MC program in good manufacturing practice manufacturing is data integrity. Software or the interface of the instrument must comply with 21 CFR Part 11. The system can be integrated into an existing control system or operated by itself. However, data should be accessible to users during operation and saved as well as backed up appropriately with traceability.
Organizational And Operational Readiness
Due to the cost and duration of the return on investment, PAT MC projects are challenging. Project momentum can be maintained via strategic organizational roles and responsibilities. A team of scientists and engineers would ideally work with vendors to test PAT and develop its use case. As the technology matures, these SMEs could move with the technology to ensure continuity of knowledge, enabling a way for SMEs to grow professionally.
Qualification, Validation, And Transfer Of Method/Models
During the initial development of a PAT method, the data generated are for understanding and used for information and monitoring purposes only. This helps build an initial understanding, including potential challenges and roadblocks toward the development of a PAT method.
An important step during the implementation of a PAT method is a comparison of the technology against the existing reference method. This requires data from qualified methods to validate the corresponding PAT methods.
Qualification And Validation Method
The main objective of the validation runs is to successfully execute the required number of lots as specified by validation, stability, comparability, local qualification/validation procedures, and/or regulatory requirements, while demonstrating a robust control strategy and critical quality attributes within the required ranges. Change control assessments should be considered where relevant. Process performance qualification is where you need the methods validated, although there may be some exceptions, e.g., for inline products.
Transfer Of Methods/Models
If a method needs to be qualified or validated at another site, processing area, lab, etc. (see flowchart in Figure 3 of steps for consideration), a supplementary validation should be performed to ensure the method can be used in the new space.
Figure 3: Flowchart of potential steps considered during method transfer
Key: TOST – Two one-sided t-tests
Life Cycle Management
After the completion of validation/qualification activities, a life cycle management process is put into place to ensure the integrity and availability of the PAT method over time and to address potential risk factors that could impact the product quality and/or the product control strategy. Life cycle management for PAT is considered continued process verification for the method/model that was validated. An implementation strategy documents the potential mitigation steps for the identified risk factors, as well as the method acceptance criteria and how to detect and respond to outliers.
All these initiatives have inputs from cross-functional teams that include, but are not limited to, members of the engagement, project implementation, and validation teams, support teams such as engineering, calibration, and maintenance operators, IT, and local quality oversight. Other inputs from PAT SMEs, manufacturing, and end users are valuable in identifying and mitigating potential risk factors and developing a robust PAT life cycle management process.
Regulatory Landscape
Implementation of PAT tools should be encouraged during the development phase of the product as it helps collect critical data during the early phases of the product life cycle prior to commercialization.
Important guidelines include ICH Q8 Pharmaceutical Development, ICH Q11 Development and Manufacture of Drug Substances, and ICH Q14 Analytical Procedure Development. The ICH Q14 is intended to complement ICH Q2 Validation of Analytical Procedures. Guideline ICH Q2 discusses the characteristics for consideration (e.g., accuracy, precision, specificity) during the validation of analytical procedures as part of registration applications submitted within the European Commission, Japan, and the U.S. The objective of validation is to demonstrate that the analytical procedure is suitable for its intended purpose. On the other hand, ICH Q14 describes science- and risk-based approaches for developing and maintaining analytical procedures suitable for the assessment of the quality of drug substance and drug product. ICH Q14 also defines the minimal and enhanced approaches to analytical procedure development (Table 1).
Table 1: The minimal approach and enhanced approach for analytical procedure development according to ICH Q14.
Key: RA – risk assessment
Conclusion
Adopting PAT is a collective journey that necessitates a broad spectrum of expertise within an organization. It is essential to involve QA, regulatory, and other advisory teams from the outset and maintain regular engagement to avoid potential roadblocks, unnecessary reiterations, and delays. Implementing PAT should be driven by a clear business case or a specific problem, rather than the appeal of new technology. Knowledge management plays a pivotal role, spanning from the initial problem statement to life cycle management.
This article summarizes some of the main points from a recent BioPhorum publication on this topic, which includes an Appendix that outlines the PAT framework described in this article. To learn more about the additional data points that are required, check out the full paper, PAT monitoring and control road map.