Addressing Human "Error" In Pharma Manufacturing
By Jim Morris, IQS Consulting
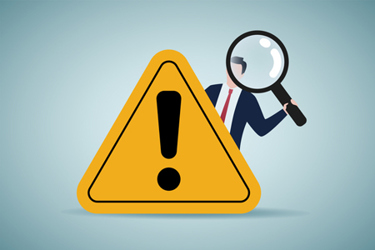
On occasion I have been asked by manufacturers with multiple sites to help improve their investigations program, with particular emphasis on reducing “error” rates. Without going into too much detail, I’ll share some of the learnings and recommendations.
Often sites will still be paper-based and gradually moving to electronic systems in the lab or on the production floor. An analysis of the types of errors in pharmaceutical operations will generally point to very similar problems:
- Documentation errors including missed signatures, wrong dates, etc.
- Production related errors in handling rejects or not following the batch record (missed samples, exceeding mixing times, etc.)
- Laboratory errors such as sample preparation issues, not reading environmental monitoring plates on time, late stability sample pulls, etc.
What most of these errors have in common is that additional training or reconfiguration of the documentation and workplace will reduce the probability of reoccurrence. However, proponents of “systems” thinking will point to more endemic issues that need to be addressed. These might include the way in which personnel are trained, how personnel communicate across shifts, and what tools they have available or don’t have available to do their work. So, if we understand the causes of these reoccurring issues, why is it that managers at sites continue to be frustrated by what could be labeled as “avoidable” human errors?
It is in that context that we must consider alternative approaches to reducing human error rates. Most managers would probably also agree that when personnel are given a task to do repeatedly, they are likely to get into a rhythm and error rates will be quite low. However, when production volumes are low and operations are performed infrequently, it is inherently difficult to get into a rhythm. One could describe this is as an “error rich” production environment, which is typical of many pharma/biotech operations.
A key objective in production operations is to minimize variation and standardize work as much as possible. Top initiatives will include automating operations, deploying operational excellence programs, addressing documentation complexity, and analyzing workflows to tease out common and special cause variation. These are all great initiatives, but experience shows that error rates will persist. So, what can we do?
I have been close to investigation system improvement for many years and have run dozens of courses on the topic. Included are sessions on improving human performance by optimizing cognitive load, reducing distractions, and making work easier for people to complete. We avoid classifying events as “human error” and judiciously try to associate the error with something else that would explain the event. I also have noticed that organizations that are good at problem solving are quite agile and their problem-solving cycle times are fast. They move the minor issues along quickly and create a work structure that results in quick response and action.
The menu of solutions to the goal of reducing error rates is extensive and sites will typically tackle it from multiple angles. The prescription offered here is based on the premise that people will do good work if we set them up for success. Therefore, our solutions need to be people-focused and drive toward reducing cognitive load (reducing distractions) so personnel can execute their work more consistently, more often. Solution set #1 involves facilitating job execution to reduce error occurrence. Solution set #2 is aimed at creating an operating environment where the investigative approach is effective at reducing error reoccurrence.
Solution Set 1 — Reducing Error Occurrence
The focus here is to select from the menu of initiatives that will standardize work and minimize variability in job execution. There is much that can be done; however, I would like to highlight four areas that foster more focus on task execution.
- SOP simplification and the use of work instructions must be an ongoing program, not a one-off initiative. If tackled as an “initiative” it will only yield short-term benefits. SOP simplification needs to be embedded as part of the way work procedures are developed.
- Focus on what personnel need to know to execute their work. Job curricula often include SOPs that fall into the “nice to know” category. Focus training on what people need to know to do their jobs.
- Instill in personnel what I call “GMP habits”. This is a way of training personnel on those tasks they must do every day, such as completing a logbook, entering data, reviewing a test record, etc. They may not be operating in a high-volume shop, but there will be tasks they complete every day that are prone to error. Standardize those tasks and provide “GMP habit” training for those tasks to drive down avoidable errors.
- Develop a job execution mindset among personnel. Most players in sports warm up before a match. Most workers, however, do not “warm up” before initiating their work. Embedding daily work habits such as pre-job briefs will encourage people to focus on the task at hand and prevent avoidable errors.
Solution Set 2 — Drive Out Error Reoccurrence
The menu of options is extensive; however, I recommend several primary actions to move in the direction of the agile, problem-solving organization.
- Develop the capability and systems to support the rapid triage of events based on risk to patients and risk to the business. Most investigation programs do not do this well and the result is an overloaded system and an overworked investigations support unit.
- Install organizational techniques that create an operational learning environment. These include forming learning teams, using pre-job briefs and after action reviews, and staying in the role during job execution (e.g. avoid switching verifier and doer roles).
- Ensure that within each unit operation there are subject matter experts, deeply knowledgeable of product and process, who can handle in-depth investigations.
- Develop the skillset to ensure event triage works, personnel are comfortable facilitating work unit meetings (e.g., pre-job briefs, after action reviews), and root cause analysis skills required to support your company’s investigation program are in place.
Often “human error” is due to lapses in communication, lack of clarity, and incomplete understanding. Thus, these should not be considered “errors” in the first place and their contributing factors need to be understood to identify suitable actions or CAPAs. Sites that embrace operational learning will have a better chance of avoiding “errors” due to the improved flow of information.
The goal of an investigation program is to get to root cause(s), assess risk to patients, and identify effective solutions or CAPAs. If work is structured such that minor issues are handled quickly by line personnel (within the quality system) and more time is devoted to root cause analysis on the challenging issues, the outcome will undoubtedly be more effective CAPAs.
Management Buy-In
In essence, what will be achieved is a new way of working, avoiding error through greater job focus and investigating events more effectively. Management needs to be on board and help to create the right environment so that people feel safe reporting and tackling error-related investigations. Change will not be long-lasting unless management is willing to support the investment to institutionalize the new ways of working. Management should select a metric that is easy to measure, easy to understand, and that will track progress.
In Summary
- Continue ongoing initiatives to automate and simplify operations as much as possible.
- Select solutions that will make work easier to perform and drive down avoidable errors.
- Develop the skills and capability to triage events quickly and consistently.
- Build operational learning techniques into day-to-day work.
- Establish a plan to sustain and institutionalize the new ways of working.
- Select a metric to track and recognize progress.
In conclusion, there are no quick fixes to the problems described above. There are no shortcuts. It’s a long road, but leaders must start somewhere. A good place to start is with your most important asset: your people.
About The Author:
Jim Morris is founder and principal consultant at IQS Consulting. Investigation and CAPA system improvement is core area of focus for IQS Consulting. Previously, he was vice president of NSF’s Pharma-Biotech Consulting practice delivering consulting, training, and certification services to NSF clients globally.