An Introduction To Quality Agreements For Pharmaceutical Outsourcing
By Joy McElroy
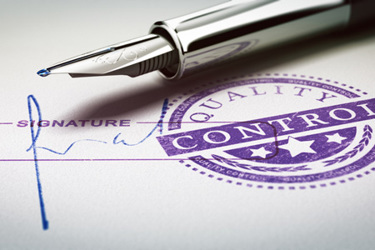
A quality agreement is a comprehensive document that outlines both specific quality parameters for a project and which party is responsible for the execution of those parameters. The level of detail in a quality agreement will be different depending on the developmental stage of the project.
Any time a contractor or CMO is used, including arrangements between different divisions of the same company, regardless of the physical location of the parties involved, there should be a quality agreement in place. The agreement should cover all aspects of the project that affect the identity, quality, safety, potency, and purity of a product. Items that could affect the compliance status of either the contractor or client must be included as well.
Regulatory Requirements
Quality agreements are not just good business practice – there are regulatory requirements for them as well. ICH guidance for industry Q7 Good Manufacturing Practice Guidance for Active Pharmaceutical Ingredients recommends that owners evaluate contract facilities to ensure that contractor sites comply with CGMP for specific operations. The written agreements should also define considerations for subcontracting. They should describe how changes to processes, equipment, methods, and specifications will be managed, and permit the owner to audit its contractor’s facilities for compliance with CGMP.
ICH guidance for industry Q10 Pharmaceutical Quality System recommends that, as part of a pharmaceutical quality system, the owner is ultimately responsible for ensuring that “processes are in place to assure the control of outsourced activities and the quality of purchased materials.” It indicates that these processes should incorporate quality risk management and include critical activities such as:
- Assessing the suitability and competence of potential contractors before outsourcing operations or selecting material suppliers. This can be accomplished through prequalification questionnaires, on-site audits, and material evaluations.
- Defining the manufacturing responsibilities and communication processes for quality related activities of the involved parties. Include all outsourced activities in the written agreement.
- Monitoring and reviewing the performance of the contract facility and identifying and implementing any needed improvements.
- Monitoring incoming ingredients and materials to ensure they are from approved sources using the agreed-upon supply chain.
The FDA encourages parties engaged in contract manufacturing to implement quality management practices. This guidance builds upon the quality risk management principles and recommendations outlined in the ICH guidance to illustrate key points in developing and executing quality agreements that describe and support contract manufacturing arrangements.
Chapter 7 of the EU GMPs requires Quality Agreements to define the responsibilities of the contract giver and the contract acceptor. It states, "Contract manufacture and analysis must be defined, agreed upon and controlled." Chapter 7 also specifies the contract preparation as it relates to the scope of responsibilities. The EMEA is in the process of adding certain outsourcing activities to Chapter 7 that are not directly linked to contract manufacture or contract analysis, such as:
- Maintenance, qualification, and validation activities
- Storage and transport
- Label printing
- Release activities
- GMP audits by third parties
Types Of Quality Agreements
There are four types of quality agreements: manufacturing, supplier, vendor, and service quality agreements, each tailored to address the relevant aspects of the particular type of relationship.
Manufacturing quality agreements are comprehensive written agreements between parties involved in the contract manufacture of drugs that define and establish each party's manufacturing activities in terms of how each will comply with CGMPs.
Supplier and vendor quality agreements define the terms and conditions relating to the quality of materials or services supplied to a manufacturing facility that are used in the products or in the production of products. Service quality agreements define the terms and conditions relating to the quality of services supplied to a manufacturing facility that are used in the production of products.
What To Include In A Quality Agreement
A quality agreement should include the following sections as a minimum:
- Purpose or scope
- Terms (including effective date and termination clause)
- Responsibilities, including communication mechanisms and contacts
- Change control and revisions
- Dispute resolution
- Glossary
The scope of the quality agreement should cover several compliance activities, such as qualification, calibration, and maintenance of analytical instruments and manufacturing equipment; validation of computer systems, analytical procedures, and manufacturing processes; specifications used to pass or fail analytical tests; supply handling, storage, and preparation; receipt, analysis, and reporting of samples; collection and management of laboratory records; and deviation management and change control.
The agreement should clearly define routine, escalated, and emergency cases and how they will be handled. The agreement also needs to define what happens in case of disputes that can be raised by either party and should document the mechanism for resolving disputes quickly and effectively.
The agreement must specify which controlled and documented changes can be made by the contractor with only the notification to the owner and those that need to be discussed, reviewed, and approved by the owner before they can be implemented.
To reduce any misunderstandings, a glossary defining key words, acronyms and abbreviations is essential. It is critical that everyone knows what is meant by each term used in the quality agreement. This is especially true when contracting with non-U.S. parties, as terminology can vary greatly. Be sure to define all referenced documents clearly.
The agreement should not include certain items such as general business terms and conditions, pricing and escalator clauses, forecasting, delivery terms, confidentiality obligations, and liability limitations. These items belong in the supply agreement, which is a separate document. The quality agreement may be incorporated in the supply agreement by reference. If the two documents are created as a single document, the approval list may include individuals that have no reason or time to review issues that are unrelated to their area of expertise.
When Do I Need A Quality Agreement And Who Should Prepare It?
A standard operating procedure should be in place to indicate the types of vendors and services that will require a quality agreement. At a minimum, an agreement must in place any time a CMO is used, as well as with all vendors of critical materials. They are recommended for vendors of large quantities of raw materials or components.
Quality assurance, with the input of manufacturing and lab personnel from both parties, should prepare the agreement. Both parties’ QA functions should review and approve the quality agreement. Nothing should be taken for granted. Each party has to review the quality agreement to ensure their requirements are included.
The quality agreement must be drafted and mutually accepted by the CMO and the client before the supply agreement is adopted, to ensure the identification of all items that are being charged and any capability limitations.
Conclusion
Quality agreements help both parties in the overall process of contract analysis. They define, establish, and document the roles and responsibilities of all parties involved in the process. Quality agreements allow each party to define their expectations and rules governing projects and ensure both parties’ quality attributes align and that each party will receive effective services and quality products.
About The Author:
Joy McElroy is the founder of McElroy Training and Consultancy, LLC, which provides consultants for various projects, as well as on- and off-site training to pharmaceutical and biotech companies globally. McElroy began her career in the pharmaceutical industry performing environmental monitoring and sterility testing and then moved into a supervisory role overseeing QC. From there, she moved into QA and then into equipment qualification and process validation. In addition to consulting, she develops and delivers webinars and seminars in areas such as technical writing, equipment qualification, cleaning validation, FDA audit preparation, and more. You can connect with her on LinkedIn.