Best Practices For Applying Automation To The Manufacture Of Drug Delivery Devices
By Ryan Moran, SMC Ltd.
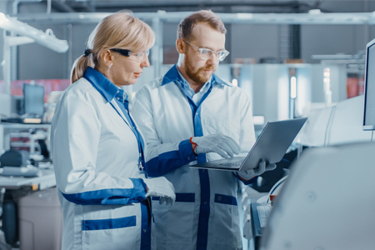
Utilizing automated manufacturing is a common strategy for contract manufacturing organizations (CMOs) to deliver quality, cost savings, speed to market, and scalability to the manufacture of drug delivery and other devices. But to exploit these advantages, it is vital that pharma companies understand automated manufacturing’s strengths and limitations, as well as how to optimize collaboration with their manufacturing partners.
As obvious as it may sound, engaging a partner early is critical to saving time, money, personnel resources, and aggravation. This means engaging a contract manufacturing partner as early in the project life cycle as the “napkin sketch” phase, when the device design is more an idea than a completely conceived product. This is not necessarily because the contract manufacturer will contribute to design for function, but because it will provide input on design for manufacturability, scalability, and packaging. Those elements are much more difficult to amend further downstream, once validations and regulatory submissions are in progress or have been completed.
Additionally, changes are a reality of most, if not all, projects. But the ease of their application depends on the extent of their impact to the automation process — it is a function of time and money. Automation is not infinitely flexible. It largely depends on three factors: the area in which change is required, the scale of automation being built, and the delta between the previous design and the new design.
Get unlimited access to:
Enter your credentials below to log in. Not yet a member of Pharmaceutical Online? Subscribe today.