Can AMTs Make U.S. Pharmaceuticals Faster, Better, Stronger?

By Katie Anderson, Chief Editor, Pharmaceutical Online
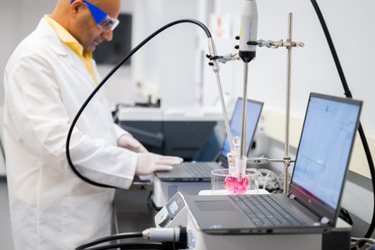
Whether or not the recently promised 200% tariff on imported pharmaceuticals takes effect, preparation for its potential implementation has manufacturers big and small exploring options to bring their API and finished formulation production stateside. Those options differ based on company funding, facility capabilities, technology needs, staffing and much more; however, one possible common solution may be adoption of advanced manufacturing technologies (AMTs) according to U.S. Pharmacopeia Vice President of Advanced Manufacturing Technologies, Dennis Hall.
With a background in physics and business, Hall is ideally suited to navigate the complex waters of advancing pharmaceutical manufacturing. That’s why he was asked to create the Advanced Manufacturing Technologies team, when the USP saw the industry moving fast in different places with a need to be out front of standardization.
Bringing Pharma Manufacturing Stateside
As we are well aware, most pharmaceutical manufacturing is taking place off U.S. soil in other countries where it is cheaper, there are more advanced manufacturing capabilities, and there are personnel to man this process. However, needs are changing.
Because of cost, Hall believes the answer is in manufacturing technologies. He furthered, “The issue is, if you want to make a particular drug in the U.S. and not make it, for example, in India, the cost base is so different that you have to think about how to make it in a different way, so that you can be cost competitive, or, more specifically, just not raise prices to the consumer, because they're ultimately the ones who will have to bear that. And that's where the advanced manufacturing technologies really could come into play.”
The cost difference varies; however, Hall noted that it can be 50-70% reduction of cost in some cases.
Cutting Costs with Continuous Flow
Rethinking the way APIs are manufactured is really where a significant cost reduction can be seen. Hall has seen significant cost reduction with API synthesis, where a movement away from batch processing can yield better product at lower costs.
“In a large batch, [a particular API synthesis] might get so hot that it would melt the batch container. You can't do that from a safety standpoint, but if you shrink that down to a much smaller area, you're able to deal with that high temperature in a safe way. That opens up a new way to make a particular product that might have better, locally sourced raw materials have a better yield, etc.,” Hall explained.
Taking continuous flow manufacturing as an example, Hall sees significant opportunity for cost reduction when the process is fully implemented. “It takes less physical space, less power and energy, less water, and produces less waste. Taking all of those various costs into consideration, that's where you can see process intensification happening,” he explained.
In one example, Hall noted a collaborator company reduced manufacturing costs by an amazing 93% by switching to continuous flow along with other chemical engineering interventions for process intensification. “It was just taking something that had been made the exact same way since the early 70s and figuring out a new way to make it, and that implementation was just a night and day change,” he added.
But after over 50 years of batch manufacturing pharmaceuticals in the U.S., shifting to a new process is a tall order. “The pharmaceutical industry has never really shifted in probably 50 years away from batch manufacturing to continuous. Companies in the food industry, probably some in the cosmetics industry, certainly oil and gas, etc., moved to this continuous manufacturing model decades ago. And so it's only pharma now that is really catching up to that technological shift,” noted Hall.
Consistent Quality with Continuous Direct Compression
Dosage form consistency of quality can be improved with AMTs, according to Hall. Rather than doing the current practice of statistical sampling, continuous direct compression can ensure quality faster, more consistently, and with more reliability.
“Continuous direct compression is a really good technology on the finished dosage form side for having that real time feedback and being able to analyze every pill that comes out of that system. Consistency of quality is what you get for finished dosage forms,” added Hall.
AI For Issue Identification in Manufacturing
Artificial intelligence (AI) can not only make the discovery process faster, but it can ensure quality of product during manufacture, according to Hall.
“AI allows pharmaceutical manufacturers the ability to create models and rapidly identify new ways to synthesize a product, but it also helps them pick up on early signals of problems in a manufacturing line that you couldn't do with traditional testing. An analyst simply can’t look at all of the spectra as rapidly as an AI model. That helps build the quality aspects to manufacturing in real time.”
Personalized Medicine in 3D
Hall continues that 3D printing offers benefit for finished dosage manufacturing in customized settings. “In areas like pharmacogenetics, where a particular person may need a customized dosage of a particular pill that isn't standardized, being able to dial in dosage in a 3D printer is beneficial,” added Hall.
The unique applications continue for 3D printing of pharmaceuticals. Hall continued, “For emergency situations, as long as you have the supply of API, the printer could make products in the basement of a hospital, for example. We are looking at some of these fascinating examples of personalized medicine.”
AMT Risk and Reward
There are many other AMTs with quality, efficiency and consistency benefits to pharmaceutical manufacturing, according to Hall. Some additional examples include continuous drying, distributed manufacturing, process analytical technology, advanced lyophilization and more.
Opportunity is out there when it comes to modernizing pharmaceutical manufacturing to reduce costs for both the manufacturer and the end consumer. Taking the leap to the investment level, however, is a different story. Check out Part II of this series for a deep dive into the industry concerns with adopting AMTs and solutions to overcome those challenges.