Chugai's Race To Zero Emissions At UK4 In Tokyo
A conversation with Shingo Goto, Chugai Pharmaceutical
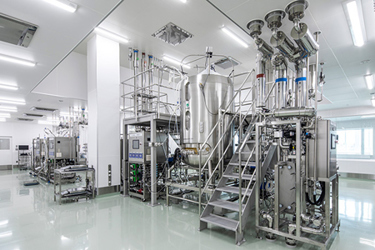
Chugai Pharmaceutical’s ambitious goal to achieve zero emissions at its new UK4 site in Northern Tokyo earned the century-old pharmaceutical company a nod from the International Society for Pharmaceutical Engineering.
ISPE will recognize the company at the 2024 Facility of the Year Awards (FOYA) Banquet and Awards Celebration at the 2024 ISPE Annual Meeting & Expo in Orlando later this year.
Chugai won the FOYA in the social impact category for UK4, which began producing antibodies for early-stage clinical supply in January.
Design and construction made use of the company’s “three zeros for sustainable development” approach, which seeks to cancel out emissions from three key sources directly and indirectly made in the production of its drug substance:
- halogenated hydrocarbons used in cooling,
- natural gas used when producing steam, and
- carbon dioxide released when generating power for non-GMP areas.
The end product is a 40,000-square-foot building that uses solar panels, alternative heating and cooling sources, and single-use technology.
UK4’s construction project manager, Shingo Goto, answered a few questions about the three zeros approach and other parts of the company’s strategy at the site.
Can you talk about each of the ‘three zeros for sustainable development’ that led this project? Where do they come from and how did you execute on them?
Goto: UK4 is a "development-type manufacturing facility" where process development and manufacturing members work together to manufacture the first batch of investigational medicinal products.
By quickly establishing investigational product manufacturing methods for promising drug candidate substances that are constantly produced by the research laboratories and supplying them for first-in-human (FIH) testing as quickly as possible, we can deliver innovative new drugs to patients around the world as quickly as possible. In-house manufacturing allows us to flexibly respond to development plans. Our innovative design allows us to not only accelerate the development of critical medicines but also set an industry standard to reduce CO2 emissions for the good of our planet.
UK4 was designed and constructed under a “three zeros for sustainable development” concept. Leaders and team members at Chugai came together to consider ideas for achieving these three zeros, which was especially important for us as part of our sustainability commitments set in 2021. UK4’s sustainable design will help us meet our midterm environmental goals for 2030, which our team is very excited about.
The first of the three zeros is zero halogenated hydrocarbons. The facility’s HVAC equipment uses 100% natural coolants and no halogenated hydrocarbons.
The second is zero natural gas. By minimizing the amount of steam consumption, UK4 was able to adopt an electric boiler, resulting in an all-electric facility. As a result, UK4 burns no natural gas, and no CO2 is emitted from the building.
The third zero is zero CO2. All electrical power used in the building is sustainably produced. Among them, the energy used in non-GMP areas is generated by solar power within the UK4 building itself. These zeros make UK4 a greenhouse-gas-free drug manufacturing plant.
We evaluated environmental and energy-saving measures as a major item when selecting a contractor, solicited proposals, and considered countermeasures jointly with the contractor during the design stage. We calculated the feasibility and cost-effectiveness of multiple proposals to determine whether to adopt them or not.
UK4 leans heavily on single-use equipment, which is widely viewed as more sustainable than steel. One of its great weaknesses, however, is all the plastic waste. How will you manage it?
Goto: Since we introduced single-use equipment, we have always recognized this as a challenge. We have collaborated with single-use suppliers, collected information from industry groups (BPOG, etc.), and investigated domestic efforts toward recycling. As a result, we came up with the answer: chemical recycling.
Waste plastics that are mixed with multiple materials and difficult to recycle are incinerated, and the incineration ash is recycled into building materials and roadbed materials. This process involves incineration, which generates CO2 — we knew we could do better. This past April, we began a demonstration experiment with a domestic company that aims to conduct chemical recycling by circulating resources without incineration. We’re hopeful about the results.
Was there a strategy behind building a new facility compared to retrofitting an existing one?
Goto: As part of a plan to quickly construct a biopharmaceutical manufacturing plant, with the aim of quickly starting FIH trials, the first stage of clinical development, and quickly obtaining early proof of concept, the initial proposal was to renovate the existing facility rather than construct a new building — especially when you take the construction period into account.
During this process, we set our midterm environmental targets for 2030 and quickly realized that an extensive renovation would not be energy efficient — it was also very likely that additional environmental and energy-saving construction work would be required. In order to achieve our targets while being purposeful in all work, the decision was made to build a new building that could apply the latest energy-saving and fluorocarbon-free technologies.
We’re thrilled to have constructed critical — and sustainable — infrastructure in an exciting new era of medicine. Chugai’s founding spirit of "creating medicines useful to the world" remains our mission statement that’s felt in everything we do, especially as we approach 100 years in business next year.
Editor’s note: Life Science Connect and ISPE are collaborating to explore the winning strategies behind select 2024 FOYA winners. Learn more about the awards.
About The Expert: Shingo Goto joined Chugai Pharmaceutical’s engineering department in 2005 and was responsible for biopharmaceutical manufacturing plant design and construction. He currently works in the pharma manufacturing and digital engineering department and is project manager at UK4 in Tokyo. He has been a member of the ISPE Engineering Management Community of Practice since 2010 and currently manages the group.