Combined Processing of Solid, Liquid, and Highly Viscous Materials
By W. Schwenk and G. Raouzeos, LIST Inc.
Contents
Multi-Step Batch Processing
Kolbe Synthesis
Combined Continuous Processing
Combined Chemical Reaction and Drying Processes
Continuous Evaporation or Drying Combined with Chemical Conditioning
Future Developments
Literature
Over the past few decades, manufacturers have used heavy-duty agitated vessels or Sigma-blade kneaders for batch processing and screw-type or special thin-film equipment for continuous processing of high viscosity materials. Applications have included polymerization, solid-liquid reactions or combined mixing/reaction/evaporation and devolatilization processes.
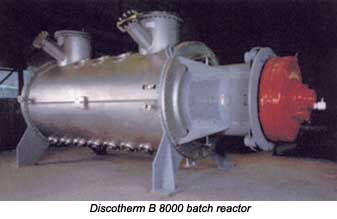
Recently, versatile single- and twinshaft kneaders combining high working volumes and large contact heat-exchange surfaces have been developed.1,2 Their large process chambers permit long residence times, opening up new possibilities for combined one-step processing. This is particularly useful for processes characterized by slow chemistry or large amounts of process gases and vapors. Table 1 shows the complex relationship between equipment design and the functional aspects of combined one-step processing where mechanical, thermal, and chemical operations interface in concentrated phases.
Multi-Step Batch Processing (Back to Top)
Batch processing is generally more flexible. Process parameters like operating pressure, heating temperature, or agitator speed can be easily changed during a batch cycle according to the specific needs of each process step or product formulation. There are, however, two constraints. The final product must be a free flowing solid or liquid to be discharged by gravity, and torque capacity must be high enough to overcome the peaks that occur during high-viscosity transition stages.
Kolbe Synthesis (Back to Top)
Sodium salicylate is used as an intermediate for the production of acetyl salicylic acid. Heavy-duty, single-shaft LIST Discotherm B batchtype kneaders (Figure 1) with a total volume of about 10 m3 (working volume of about 6 m3) are used for this multi-step synthesis.

Starting with phenol and sodium hydroxide solutions, the product repeatedly changes back and forth between liquid and pasty or solid granular in several successive phase changes. To achieve the best possible yield and degree of conversion with fewer by-products, very tight control of the product temperature is important, particularly during the carboxylation reaction. The Discotherm B provides this control, thanks to its combination of good mixing/kneading properties and interface renewal with large, self-cleaning heat-exchange surfaces (Figure 2).
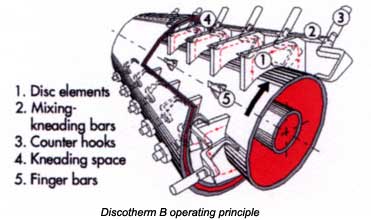
Combined Continuous Processing (Back to Top)
Extruders or similar screw-type equipment are widely used for high-performance, combined one-step continuous processing in the polymer and food industries. Some examples are melting/compounding/devolatilizing polymers, reactive extrusion and bulk polycondensation.
If slow, diffusion-controlled chemical or physical processes requiring long residence times are involved, or if large amounts of gases or vapors need to be removed, extruders and screw-type equipment may not be suitable. Their relatively small working volumes and restricted free crow sectional area and vent port sections act as constraints. High-volume LIST CRP/ORP kneader/reactors 1,2 are free of these constraints and offer custornizable continuous processing.
Combined Chemical Reaction and Drying Processes (Back to Top)
Urea resin production by combined one-step polycondensation, and drying is a very effective way to obtain final product. Concentrated hot urea solution and liquid aldehyde are continuously fed in a stoichiometric ratio to a continuous, single-shaft reactor/dryer. The addition of catalyst initiates the exothermic reaction in the first section. The excess reaction heat is partly removed by the evaporation of aldehyde, which is condensed in a reflux condenser. The reaction mass undergoes a series of phase changes from slurry through a pasty, sticky intermediate phase to a final, crumbly solid state, and is then dried in the second half of the unit. The whole process is autothermic in steady-state operation.
Continuous Evaporation or Drying Combined with Chemical Conditioning (Back to Top)
Continuous vacuum evaporation and drying of distillation residues, polymer solutions, and food concentrates are important applications for heavy-duty kneader/dryers. In many of these applications, the drying process is combined with the necessary chemical modification of the product under controlled temperature and residence/time conditions. Following are some examples.
- Maillard reactions provide delicate flavoring for milk crumb, dried under vacuum from sugared milk concentrate.
- Toluene diisocyanate (TDI) is recovered from extremely sticky, toxic and chemically unstable distillation residues by continuous vacuum evaporation. A high-yield, safe conversion of the residual tars to a non-toxic, granular matter by chemical reaction can only be achieved in a low vacuum and with a long residence time.
Future Developments (Back to Top)
When fine chemicals or polymers need processing, heavy-duty kneader/reactors allow multiple operations like melting, chemical reaction, devolatilization, and mixing or compounding to be combined in a single unit. New high-potential technologies are being developed by close cooperation between manufacturers and equipment suppliers.
- List, J.: High-volume kneading reactors, cpp 2/94, pages 34-37
- List, J.: GroBvolumige Knetreaktoren, cav 5/95, pages 164/165
For more information: LIST Inc., 42 Nagog Park, Acton, MA 01720. Tel: 978-635-9521. Fax: 978-263-0570. Email: listinc@worldnet.att.net.
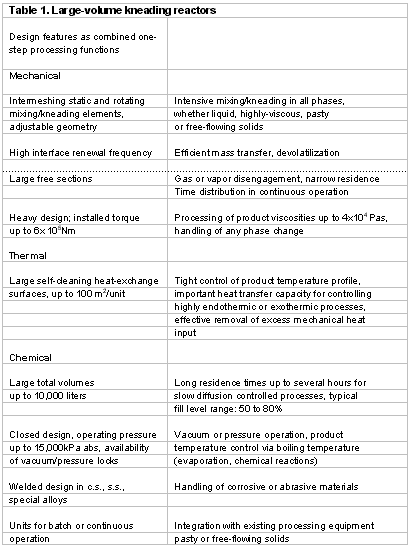