6 Common Root Cause Analysis Mistakes
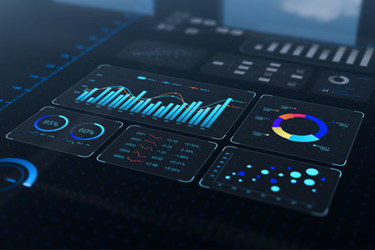
Root cause analysis (RCA) is a critical process in manufacturing that is essential for identifying and resolving underlying issues to prevent recurrence and safeguard organizational reputation. However, several common mistakes can undermine its effectiveness. First, teams often jump to conclusions, hastily identifying solutions without a comprehensive examination of the problem. This can lead to addressing symptoms rather than root causes, resulting in persistent issues. Additionally, inadequate data collection and a lack of collaboration among stakeholders can skew results, while neglecting human factors may misdiagnose the core problems.
Moreover, organizations frequently overlook the importance of follow-up, allowing unresolved issues to resurface. The pressure of tight deadlines can exacerbate these mistakes, leading to superficial analyses that fail to uncover deeper systemic problems. To counteract these pitfalls, it’s vital to adopt a thorough, collaborative approach to RCA, ensuring that all perspectives are considered and that solutions are effectively implemented and monitored.
ETQ, a division of Hexagon AB, offers integrated quality management solutions to facilitate effective RCA through its Corrective Action (CAPA) application. To learn more about avoiding RCA pitfalls and enhancing your problem-solving capabilities access the full article.
Get unlimited access to:
Enter your credentials below to log in. Not yet a member of Pharmaceutical Online? Subscribe today.