Continuous Flow Processing
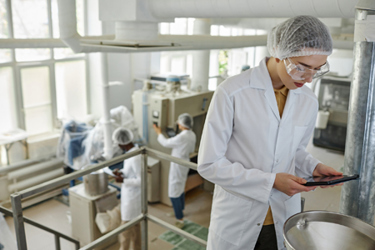
Continuous flow processing can be integrated into a broader strategy of sustainable manufacturing. By optimizing processes to reduce waste, energy consumption, and environmental impact, pharmaceutical companies can demonstrate their commitment to environmental stewardship and meet regulatory requirements for sustainable practices.
With decades of experience in continuous flow processing, SK pharmteco is equipped to support your project at all scales.
Reduced Waste
~99% The waste reduction achieved through SK pharmteco’s solvent recovery strategies
Continuous flow reactions typically run significantly more concentrated than batch reactions and are less prone to side reactions, resulting in better yield and better atom efficiency. As a result, continuous processes use less unit operations, consume less solvents, and generate less waste.
In addition, continuous processes are amenable to recycling strategies, resulting in a significant reduction in waste generated.
Lower Energy Consumption
~50% Electricity used at SK pharmteco is sourced from renewable sources
Continuous flow processes can be more energy-efficient than batch processes.
By continuously flowing reactants through the system, there can be less downtime and energy wasted in heating and cooling between batches.
Lower Solvent Use
By accessing higher operating temperatures and pressure, continuous reactions can be run more concentrated using more environmentally friendly solvents than in batch.
Also, flow processing is amenable to recycling stategies allowing for a significant reduction in the consumption of natural resources and reduction of transportation.
Solvent Recycling
SK pharmteco’s large scale solvent recovery drives significant PMI reduction
Improved Process Control
AACE Team
Analytical, Automation, Chemistry, & Engineering work together at SK pharmteco to provide a robust, scalable continuous process
Continuous flow processes typically offer better control over reaction parameters such as temperature, pressure, and mixing compared to batch processes.
This enhanced control can lead to higher yields, fewer side reactions, and overall, more efficient use of resources.
Sustainable Manufacturing
Continuous flow processing successfully addresses the 12 principles of Green Chemistry providing pharmaceutical companies solutions for improved sustainable manufacturing. Therefore, continuous flow processing demonstrates a strong commitment to environmental stewardship.
Net Zero Carbon
SK pharmteco’s goal is to achieve net zero carbon emissions by 2040
SK pharmteco has decades of experience conducting chromatographic separations at a commercial scale in a highly regulated environment. Our Simulated Moving Bed (SMB) processes can be developed in a few weeks and are easily scalable. In many cases, scale-up from gram to multi-ton quantities can be achieved in less than six months.
Our services include SMB screening, method development, proof-of-concept demonstration, and production of gram-to-multi-ton quantities of intermediates and APIs. SK pharmteco proudly operates the largest CGMP SMB unit in North America (5 x 1,000 mm), which supports commercial-scale API production of hundreds of metric tons per year. Our facilities include kilo-scale and pilot-scale units to support smaller quantities also under CGMP conditions.
The FDA has inspected and approved the SMB process for manufacturing APIs. SK pharmteco has four registered products with regulatory authorities (FDA/EMA) using SMB technology. With several decades of experience, we consistently deliver high-purity products tailored to meet the specific needs of our partners under CGMP.
Typical Applications are:
- Chiral separations
- Separation of diastereomers & regioisomers
- Removal of troublesome or genotoxic impurities
- Other complex separations
Discover how our advanced separation techniques and expertise can support your next breakthrough.