Design And Function Of GMP Transition Spaces
By Geoff Middleton, architect, cGMA, Inc.
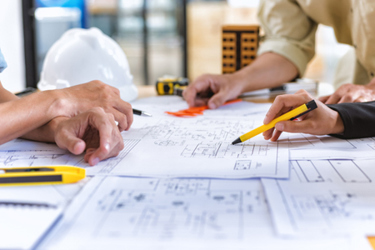
The GMP world has several typical space types that function as transition spaces. These are generally air locks and gown rooms but also include locker rooms, dock and warehouse vestibules, and similar functional spaces. This article discusses their often multiple overlapping functions and how procedure and arrangement can influence their effectiveness.
What’s A Transition Space?
In many types of buildings and areas within them there are disparate conditions. One might be warm, another cold, another noisy, smelly, bright, dark, humid, and so on. If we have little concern for short-term disruptions to these distinct environmental conditions, the areas can simply be directly connected by a door, for example. Should we wish to maintain continuity of a particular set of conditions in one or both adjoining environments, it may be desirable to limit the impact of entry or egress from an area by the use of a transition space. At its most basic, a transition space is a bridge or translator between the two adjacent dissimilar environmental conditions.
Similar to a vestibule at an exterior building entry that limits the cold winter wind from chilling the lobby when the exterior door is opened, a transition space establishes and enforces a process or procedure in space and time that transforms, or translates, from the conditions on one side to the conditions on the other side of the connected areas while limiting the momentary impact to either.
For the building vestibule, one side is still and warm, the other windy and cold. The environment within the vestibule may be either at any given moment in time, based on which door is open, but it serves to form a stabilizing intermediary, or bridge environment, between the two areas that allows, or requires alterations to take place to the people or objects making passage.
Generally, the performance of a transition space is partial, not absolute. That lobby in the vestibule example is still a bit brisk due to the periodic introduction of vestibule volumes of cold external air. It is warmer and calmer than it would be absent the vestibule, but you wouldn’t want it to be your office, either. Several doors, hallways, and intermediary spaces later, the office is warm, stable, and comfortable.
Additionally, a transition space is not to be confused as belonging to either adjacent environment. The lobby vestibule is sometimes as cold (or hot) as the exterior and, alternatively, as moderate and comfortable as the lobby. In between these conditions is a period of “recovery” or environmental adjustment to serve as bridge between adjacent conditions. In fact, the vestibule is likely equipped with greater capabilities for heating and cooling than the lobby itself in order to speed its recovery period and increase its effectiveness.
GMP Transition Spaces
In the GMP regulated manufacturing industry, transition spaces may regulate transitions between air classifications, air pressure levels, air handling unit zones, different product or batch manufacturing areas, biosafety containment areas, containment of toxic or potent materials handling and manufacturing areas, hazardous materials handling spaces, dust generating processes, noisy equipment spaces, or simply the transition from the exterior to the interior of the building itself. Often, combinations of multiple transition conditions, drivers, and functions apply simultaneously. Any one function may lead to the incorporation of transition spaces.
The Myth Of Perfection
The Reality of Engineering and Operations
We all have an understandable tendency to think that our systems are perfect. If it says “waterproof,” then it’s completely dry inside. Well, not quite. In practical reality, no engineering system is absolute. All perform within tolerances and to a stated level of performance. The same is true for transition spaces. They have a range of effectiveness based upon features and procedure and, the higher performance each has, the higher its cost.
Generally, GMP transition spaces are each of moderate performance and are arranged in hierarchical order to generate high collective performance at the areas of greatest concern.
Filter Analogy
As an analogy, any transition space acts similarly to a filter. It has a performance level just as a filter does. A high-performance air filter (HEPA, for example) properly designed, mounted, and maintained may retain 99.97% of particulates within the target size ranges in the feed air. Other filter types may be rated at 85% or less. This is similar to the operation of transition spaces.
To continue the analogy, if the feed air has 1 million particles per cubic foot, and the filter has 85% efficiency, the air downstream of the filter will have 150,000 particles per cubic foot. Passing through the same filter type a second time reduces the particle load to 22,500 particles per cubic foot. Multiple passes result in higher overall performance.
Transition spaces guard manufacturing spaces with high standards of environmental conditions. They can only succeed if the contaminant load outside the transition space is modest in the first place. This is why GMP facilities are structured in a series of layers, each zone cleaner than the last, finally transitioning into the highest, most critical manufacturing environment. As best practice, we proceed from the external environment to air-conditioned interior space, then to clean not classified (CNC) space, to Grade D, to Grade C, and so on. Each step in the hierarchy is accompanied by a layer of transition spaces. We can therefore conclude that the effectiveness of any previous transition will have a direct effect on the performance of all that follow.
To conclude the analogy, HVAC systems are actually designed in just this way. Before feed air gets to the HEPA filter it has already been pre-filtered to reduce the challenge on the primary filter, thereby assuring the required environmental conditions are achieved.
Functionality: Role
GMP transition spaces and attendant procedures may serve several functions and, in many instances, do so simultaneously. A summary of functionality:
Cleanliness: Air Classification Changes
As environments used for manufacturing increase in cleanliness level, transition spaces are incorporated at classification boundaries to maintain and protect the higher level from adjacent lesser-quality environments.
Even where no change to air classification occurs, in some instances we wish to separate more clean from less clean. For example, upon receipt from over the road transportation at the warehouse loading dock, manufacturers often remove wrapping and wooden pallets from shipments, replacing them with non-porous, in-house pallets and fresh shrink-wrap. Ideally, this is accomplished before moving the received materials into the warehouse for storage, though there is no change in air class. The loading dock vestibule itself acts as a transition space.
Segregation
A fundamental concept of GMPs is prevention of contamination, including cross-contamination. Multiple products manufactured in a single facility, or areas where different raw materials are handled, must be kept apart in order to prevent cross-contamination. Similarly, core to GMP concepts is our ability to identify, isolate, and test different batches of any product. Should a batch fail to successfully test, or later prove to be unacceptable in any way, we require assurance that adjacent manufacturing batches of the same product will not have been inadvertently deleteriously impacted. Segregation between batches is thereby required, and in some instances this is extended to the design of environments in which they are made and handled.
Containment
The cleanliness item above essentially speaks to keeping unwelcome elements out of the manufacturing environment. Containment, on the other hand, comes into play when some intentional component of manufacturing must be kept within for the protection of surrounding spaces, staff, and visitors.
These include:
- Flammable, combustible, or explosive materials
- Radioactive materials posing a health threat
- Ingredients in production that comprise a threat to the health of staff or visitors. These could be nearly any active ingredient that must be controlled and contained from ingestion due to their potent effects. Often these materials are referred to as potent materials and have strict operator exposure limits.
- Biocontainment refers to living disease-causing agents such as viruses, bacteria, yeasts, and molds, etc.
- Oxygen depleted environments where the use of a material such as nitrogen may inadvertently result in a dangerously low concentration of oxygen threatening the health and safety of staff and visitors.
Containment as a function of transition spaces may be understood as a broad continuum. At the more severe end of the spectrum are disease-causing agents, toxic or hazardous materials, etc., as described above. In the GMP manufacturing space we also have a primary interest in segregation. Examples include separating product A from product B and batch A from batch B within the manufacture of a single product. In the design and procedure of transition spaces, the tools of containment will be utilized to accomplish these goals as well. Risk evaluation is brought to bear in determining what containment approaches and tools to utilize and to what extent. For example, carryover between products and batches is perhaps less of a risk when the process is closed, versus an open process basis, or processing approaches that potentially contaminate staff and the room.
Access Limitation
Transition spaces are often used in part to allow transfer of material while simultaneously enforcing limits on access to manufacturing areas for members of staff. An example is a material air lock (MAL) between a manufacturing corridor and a manufacturing suite. A member of the logistics support staff can gain access to the MAL by key card from the corridor, but their card will not permit opening of the inner door to the manufacturing suite. The member of manufacturing staff within the suite, on the other hand, can enter the MAL as needed and open the inner door to the suite once wipe down procedures are complete. In this way, a secure material handoff can be accomplished via the MAL with no access limitation breach.
Functionality: Internal Workings
Transition spaces function by incorporating several contributing characteristics, procedures, and systems to accomplish their roles. Fundamentally, a transition space is a physical expression of the procedures it supports and hosts. Procedure and configuration cannot be understood in isolation from one another as they work together to accomplish the transition space’s goal.
A summary:
Air Pressurization Control
Various air pressure hierarchies may apply depending on the specifics of the role of the transition space in the facility. The transition space assures continuous maintenance of the desired air pressure relationship between the two adjacent primary spaces.
Air pressure is used as a means of accomplishing the primary goals of a transition space. Frequently in service to a higher cleanliness classification, air pressures are maintained to flow outward in a cascade, thereby resisting ingress of contaminants from less clean surrounding environments.
Worthy of note is that the transition space itself does not, and is not intended to, maintain its own target pressure while either door is open. For example, if room 1 is pressure A, transition space is pressure B, and room 2 is pressure C, all measured at rest and with doors closed, upon opening the door between the transition space and room 1, the pressure in the transition space will be A. Upon closing the door, a recovery period for the transition space is needed to return to the designed pressure B. Then, upon opening the door between the transition space and room 2, the pressure will be C, and so on. The goal of the transition space is to maintain the continuity of pressure relationships between the two connected primary areas, acting as a sacrificial intermediary bridge space.
Change In Air Classification
A person or physical item passing through a transition space between differing air classifications undergoes a process by which the two adjacent environments are maintained separate and retain their integrity during entry and exit.
For a member of the staff or a visitor making passage through the transition space, the procedure likely includes gowning addition or removal and may include hand sanitization and the like. In support of this procedure, the personnel transition space (gown room) incorporates gowning supplies, a leg swing bench, personal safety equipment supply, waste disposal and hampering for used or soiled items, as well as sufficient space for the number of staff intended to make the transition at one time.
For materials and equipment, wipe downs and bagging or debagging are undertaken to transition external surfaces from the source conditions to the destination environment. This will necessitate supplies of wipe down materials as well as disposal of spent items, and sufficient space to accommodate the largest items to make transition plus sufficient space for access all around for staff to accomplish wipe down, open and close doors, etc.
Similar to the in-process description for air pressurization above, the transition space temporarily adopts the air classification of the adjacent space during the period when its door is open and for a recovery time period after the door is closed and internal procedures have been completed.
The recovery process mentioned previously is a waiting period while HVAC systems clear disturbed air volume within a transition space to the state of cleanliness, pressure, and equilibrium desired before a procedure is completed or a new transition cycle begins. From an operational perspective, shortening this period as much as practicable is advantageous as it debottlenecks use of the transition space. For this reason, transition spaces are often designed and validated with greater air flow (air change rate) than the classified space they serve.
Additionally, the use of wipe down products and materials in material air locks that evaporate or have offensive odors or hazardous fumes may drive an increase in the proportion of exhaust air to that recirculated in order to control odors and vapors. The same may not apply to gown rooms.
Door Interlocks
Automated systems may be incorporated in the design and construction of transition spaces that prevent doors into both adjacent environments from being opened at the same time. Additionally, these systems may be programmed to enforce periods of recovery in transition spaces such that they are able to return to target environmental conditions before any of the doors are allowed to open again. They may also be incorporated into access security (card reader) systems.
Alternatively, status lights within and outside transition spaces can indicate to users whether a space is prepared for entry or exit, relying on compliance with procedure by staff and visitors to affect the same result as interlocks.
Batch Process
Once staff or an item enters a transition space, they must complete the transition procedure and exit before any subsequent user may enter. This is the case for gown rooms and material air locks within manufacturing environments, but not for locker rooms, warehouse and loading dock vestibules, etc.
A handy analog is a pass-through autoclave. We have the general understanding that an item(s) is placed into the autoclave on the load side with viable contaminant materials included. Once the load side door is closed, and the sterilization procedure initiated, no additional items may be inserted until the process has completed and the treated items removed from the unload side and the door closed once again. If additional items were to be introduced to the autoclave chamber after initiation of the cycle, we cannot be assured that its validated function (i.e., sterilization) would be successful.
Similar to the autoclave functional model, a transition space makes a full cycle upon each transition from one environmental condition to the adjacent destination condition. The cycle may include gowning changes, wipe downs, timed air cleanliness and pressure recovery, etc.
Gown Rooms And Material Air Locks
Gown Rooms Baseline
For staff entering a manufacturing area, typically the destination room is at a more stringent cleanliness standard than the arrival environment (often a manufacturing corridor). The diagram below illustrates in general form the transition undertaken. The arriving staff enter the gown room from the lesser classification, dressed appropriately for its conditions and carrying on them accumulated materials and contaminants from the arrival environment. Upon proceeding from the gown room to the destination room they will have donned additional elements of gowning of nature and condition to support the destination’s more stringent environmental conditions. These additional gowning elements also serve to encapsulate the less clean garments and contaminants from the arrival environment, as well as the person themselves. Procedures within the gown room are designed to optimize the performance of this transformation.
At its simplest, egress is the reverse of the entry sequence, releasing the staff member back to the original arrival environmental conditions. A factor almost always present is some level of containment for the manufacturing space. While working in the manufacturing space, the staff may become contaminated with elements of process materials on their gowning. To achieve segregation between products and batches outside the manufacturing space, the removal of gowning elements and other procedural steps within the degown room acts to leave behind any such carryover materials from exiting to the neutral outer environment (manufacturing corridor). This is illustrated below.
In practice, the need for segregation and containment may drive a gowning step upon entry even if there is no step up in environmental conditions within the manufacturing space. thereby having a layer of gowning present to remove upon egress.
Material Air Locks Baseline
Material air locks differ from gown rooms primarily because the materials and equipment passing through them cannot treat themselves, as staff do in gown rooms. Any procedure carried out to clean or decontaminate must come from the room itself or staff within it. What follows is an example of a typical material air lock procedure.
To follow a path parallel to our staff member above, an object arrives at the material air lock (MAL) accompanied by a member of the staff. Both enter the MAL, and the door is closed. Staff retrieves wipe down materials from supplies provided within the MAL and wipes down the object. The staff member then retires to the arrival room (manufacturing corridor) and closes the corridor door. A residence period may ensue for wipe down disinfectants to achieve effectiveness.
A staff member from the manufacturing space then enters, closes the door, retrieves fresh wipe down supplies and wipes the object a second time. This second wipe down may be needed to remove the residue from the first procedure or to assure clearance of contaminations brought in from the arrival environment (manufacturing corridor) or both. A second residence time may need to elapse, depending on materials in use and company procedure. Finally, the staff member from the manufacturing space withdraws with the object, now prepared for the environmental conditions within.
In some instances, an outer bag may be removed from a sequence of concentric layers of bags protecting pre-cleaned or sterilized equipment, tools, or supplies. This may apply to the initial wipe down, to the second wipe down, or both, upon entry.
Note that any accessory that transits the transition space into the manufacturing environment is treated in the same fashion as the object itself, such as, for example, a cart used to transport the object.
Egress for objects often also involve procedures within transition spaces to containerize or wipe them down to limit the transfer of processing or containment materials to neutral spaces outside.
Pass-Through
Pass-through is a term used here as a version of a MAL that is physically too small to accommodate a member of staff. They are typically mounted through a wall adjoining two areas of differing environmental conditions, in a manner similar to a MAL. The primary distinction is that, due to size and accessibility, the procedure that can be undertaken within during a transition is limited.
The range of equipment available for use as pass-through is quite broad. In summary:
- At its most rudimentary, a pass-through is a box mounted through a wall connecting two adjacent spaces that may, or may not, have interlocked doors permitting only one of the two doors to be opened at any one time.
- Pass-throughs may be equipped to maintain a particular air pressure with the doors in the closed position. This may be a positive or negative air pressure relative to the two adjoining areas.
- Pass-throughs may perform an active function. These include decontamination by various active means such as ultraviolet light, vaporized hydrogen peroxide, or others. Note that such automated active decontamination systems are also available at the scale of a MAL. A pass-through (double door) autoclave would qualify in this category, though they are only used as material pass-throughs for sterilizing inbound equipment and materials to an aseptic manufacturing area or for the outbound decontamination of materials and equipment from areas with high levels of biocontainment, for the purposes of this discussion.
Note that active process pass-throughs, other than the inbound autoclave, are focused on decontamination. This is a containment function rather than a cleanliness improvement.
This is simply due to lack of space within the pass-through for staff to function. They are unable to wipe down the object and leave it to reside for the procedural period within the pass-through. Nor can they enter and wipe again before transition. If the wipe down takes place in the arrival environment, the object is exposed to contaminants in the arrival environment continuously up until the object is deposited in the pass-through. Subsequent wipe down by destination staff taking place within the destination environment undermines the isolation and protection the MAL is designed to provide.
In summary, a conventional pass-through is most useful for outbound passage of materials of smaller size where containment is of limited concern. Active decontamination pass-throughs may be utilized where containment of biologic agents is critical but would have little advantageous impact for containment of non-viable substances. Inbound pass-throughs pose challenges that require detailed procedural and quality consideration as they are unlikely to perform as well as a MAL.
Dedicated Directional Flow Versus Bidirectional Flow
In some cases, transition spaces are dedicated to a single directional flow with one gown room and material air lock dedicated to arriving and entering staff and objects and a second separate set of transition spaces dedicated to exit/degown.
There are four primary reasons for such dedication.
- A high traffic level into and out of the area would lead to bottlenecks in the transition spaces, disrupting and complicating operations.
- Overall facility flows incorporate distinct supply and return corridors providing access and egress from manufacturing spaces. Dedicated entry and egress transition spaces are thereby required.
- Containment within the manufacturing space is a high priority. *See below.
- In some instances, regulatory guidance and mandates require dedicated directional flows in transition spaces.
In the absence of any of these reasons, transition spaces may function bidirectionally, meaning either entry flow or egress flow may be accommodated independently and sequentially in a single set of spaces.
Effect On Containment
Where containment performance of transition spaces is at a premium, the design of dedicated directional flow may allow an increase in performance.
Examining procedure and design of entry and egress solely from a containment perspective, the arriving member of staff, or object, is neutral to the subject material or agent to be contained. Upon entering the arrival transition space and initiating transition procedures, it is desirable that the staff member and object remain neutral. For this reason, entry transition spaces are best designed as air pressure bubbles. Inadvertent, premature ingress of contained materials is thereby resisted.
Alternatively, upon egress, the member of the staff or object is conceptually contaminated with materials to be contained. Upon entering the egress transition space there is direct and unavoidable carryover of contained material. The clearance procedure – degowning or wipe downs that involve physical activity and movement – is likely to further release materials into the air during transition. At this stage, positive air pressure may have the potential effect of pushing contained contaminants outward to the neutral outer space (manufacturing corridor). Hence, a dedicated egress transition space would typically be designed to achieve a negative, or “sink” pressure relationship to both the arrival and destination spaces.
Dedicated directional flow transition spaces permit the design to achieve both best cases. If a combined flow transition space is utilized, a compromise design must be used that will undermine best performance in one flow direction or the other.
Where concern for containment is elevated due to the nature of manufacturing within the suite, an additional overlayer air lock at the higher air classification of the manufacturing suite may be incorporated. This additional air lock is used to add a buffer layer of controlled pressure, typically a positive, or “bubble,” offering the neutral manufacturing corridor an added layer of protection from the cyclically contaminated gown room or material air lock, while simultaneously maintaining continuous protection to the higher cleanliness of the manufacturing suite. The diagrams below illustrate comparison between the conventional single layer of transition space and the parallel arrangement that incorporates an added buffer air lock. Note in each case the relative location of the containment boundary. Additionally, the air flow comparison indicates that the added buffer air lock results in continuous higher classification air pushed into the manufacturing suite, whereas without it, lower classification manufacturing corridor air is introduced. The buffer air lock allows optimization of both cleanliness and containment criteria simultaneously.
Click for full size.
Click for full size.
As a primarily neutral buffer space incorporated for air pressure control, these additional air locks may be supplied with air from the corridor air handling unit, rather than the adjacent manufacturing suite.
Multi-Step Air Class Change
In some instances, a double step transition is needed. This includes, for example, a transition from Grade D to Grade B environments with no intermediary Grade C space. This arrangement presents particular challenges.
As discussed earlier, the layered hierarchical approach to transition spaces in GMP manufacturing is built upon the premise that each layer of transition spaces will only be “challenged” by entry conditions one step lower than the served destination space. For example, a transition space leading to a Grade C environment is entered from a Grade D arrival area that has attained equilibrium, operates reliably, and is validated to maintain Grade D conditions. Transition spaces by nature are in flux when in operation. Recall the introductory example of the building entry vestibule protecting the lobby; that vestibule rarely attains comfort conditions. By placing two stages of GMP transition spaces in sequence, the expected, standard challenge to each will likely be exceeded.
Nonetheless, the following is a description and discussion of such a succession of configuration and procedure.
In our example, entering staff proceeds from the Grade D arrival space to the first transition space, a Grade C nominal gowning room. Gowning should be undertaken to a Grade C standard, and sufficient recovery time must elapse within the transition space to attain Grade C equilibrium before proceeding to the subsequent Grade B transition space. In this process, the Grade C gowning step is solely to limit the “challenge” to the Grade B transition space to a level equivalent to a more typical single-step transition. Unfortunately, this description is idealized, and it is often not followed in practice.
Where this type of multi-step transition space stack has been observed in practice, this intermediate step is often overlooked or eliminated altogether. The final upgrade of gowning to the destination Grade B standard then takes place in the second transition space (Grade B) before entry, starting in Grade D attire.
While the described procedure may succeed (meaning, avoid environmental monitoring alarms within the manufacturing environment), it is both a higher risk, or challenge placed on the final entry transition space, and, more often than not, a shortcut in practice.
The more obvious complexity arises for objects transitioning such a stacked set of transition spaces. In the gowning case, people can perform procedures for, and on, themselves. Objects, on the other hand, cannot. They rely upon people for wipe down, movements, entry, exit, etc. The complexities that arise for objects in a multi-stage transition are: Who will perform them? How are they gowned? What contaminants will they bring along from their source environment while performing procedures on the objects? Where, within the stacked transition spaces, are they to perform these procedures?
Upon entry, and following the example case, the object is taken into the first transition space, nominally Grade C. The Grade D staff member accompanies the object and performs the initial wipe down, then retires to the Grade D arrival area. Once the residence time for the wipe down materials has expired, who will perform the subsequent wipe down or take the object to the Grade B transition space? Absent a Grade C environment populated with appropriately gowned staff, a compromise of necessity will have to be struck. Either a member of the Grade B destination environment will pass through the Grade B transition space, entering the Grade C transition space to perform a second wipe down and retrieve the object or a member of the Grade D environment will reenter the Grade C transition space, wipe the object a second time, and transport the object into the Grade B transition space. Either option carries Grade D contaminants into the Grade B transition space and, thence, likely, to the Grade B operating environment.
In summary, a two-step sequence of material transfer MALs presents significant complexity that, if permitted, must be addressed by detailed procedure.
The Demarcation Line
Many MAL transition spaces are equipped with a “demarcation line.” This is a line on the floor within the transition space that visually and procedurally distinguishes the arrival side from the destination side within the room. Procedures in such transition spaces incorporate a wipe down followed by moving the object across the line to the “clean” side upon entry. Subsequent procedures, a further wipe down, for example, are undertaken by staff entering from the destination environment. Such a line is used to indicate, by physical position, the completion of some portion of a procedure to be performed on objects transitioning the space. It may also be used to procedurally limit the extent to which staff members from either side may tread on dedicated floor areas and thereby limit transfer of contaminants by shoe contact between environments. Care should be exercised during design to ensure that transition spaces incorporating demarcation lines are of sufficient size for objects and staff on each side to carry out required procedures.
Summary
A wide range of contributing requirements and functions impact the design of transition spaces, often simultaneously. Additionally, hierarchies and layers of such spaces interact and rely upon one another to succeed in their various functions. A clear, detailed, and explicit understanding of what functions each undertake and how these criteria are satisfied is critical to the design of the overall facility, the success of each transition space, the hierarchy of transitions of which it is a part, and ultimately the protection of product quality.
About The Author:
Geoff Middleton is an architect with cGMA, Inc. He has more than 30 years of experience designing cGMP, regulated products, pharmaceutical, and biologics manufacturing facilities of a wide breadth of sizes and types, all over the world.