Drug Delivery Systems: Measurement System Analysis Using Continuous Gage R&R Studies, Part 2
By Allan Marinelli and Howard Mann
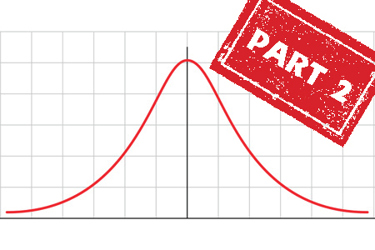
All drug delivery manufacturing systems that undergo quality improvement projects to reduce the defect level while improving the response time for correction(s) involve teams, or an assigned group of stakeholders, to gather as many potential inputs as possible that are intrinsic to the system at question and to subsequently analyze the data to arrive at the most plausible solution(s). This constitutes the intent and elements of designing continuous gage repeatability and reproducibility (GR&R) studies.1 Read part 1 of this article series here if you missed it.
In this article, which is part 2 of three, we will examine the following topics with respect to designing a continuous gage R&R study protocol:
- prior to designing the study protocol (prerequisites) phase,
- development and approval of the study protocol phase,
- execution of the study protocol phase (execution sequence), and
- post-execution of the study protocol phase.
In part 3, we will discuss a generic case study example of continuous (variable) GR&R using Mini-tab, including:
- an overview of interpreting the setup and how the data is connected in conducting a generic case study,
- the role of the study director in how the measurement system analysis is set up and configured, including its parameters,
- data entries,
- the analysis phase, and
- an optional step for data compilation.
Designing A Continuous (Variable) Data Gage R&R Study
A continuous data GR&R study constitutes a measurement assessment performed by obtaining various output results (in a randomized trial) for several device types, items, or parts. An operator performs the assessment by using an external calibrated device or other applicable measurement devices used in the development and/or manufacturing processes to measure the items or parts of the device.
When the same operator measures the same type of items/parts/devices in another randomized trial, the result is expected to equate to that of the first trial or show the lowest number of variances amongst operators.
Post-evaluation analysis of the data obtained by such measurements, reported in data sheets from randomized trials for each operator, determines the individual operator’s “repeatability” of the GR&R study (determinations of intra-operator variability based on the output of the data).
When different operators measure (for inter-operator variations) the same known master items/parts/devices, this will substantiate the overall “reproducibility” of the GR&R study. Because of the complexity and interdependencies involved in putting together a continuous GR&R study, all drug delivery developers must factor in certain recommended elements, as listed in the prerequisites sections below.
NOTE: This overview represents neither a prescriptive nor an exhaustive list of elements to be encompassed in designing a continuous GR&R study.
Prior To Attempting To Generate A Continuous Data GR&R Study
In many companies, study directors (authors of the study) often wish to “copy and paste” information quickly into a continuous data GR&R study, in an attempt to ascertain a smooth execution by minimizing preventable human-error deviations from the study template, without factoring in all the necessary prerequisite steps. The study director must understand the theoretical and actual manufacturing process applications as stipulated in Part 1 of this series. The prerequisite steps necessitated before designing a continuous data GR&R study are delineated below:2
- Assess and use the required known sample quantities (previously captured during a development and/or manufacturing run that was assessed by the study director or designee) intended to be used in alignment with the required number of samples/items/parts/devices stipulated in the QMS Statistical Sampling Requirements SOP(s).
- Assess and ensure that all measurement devices needed to measure the manufactured items/parts/devices are in a state of current calibration and will not expire during the intended execution date.
- Ensure that all applicable SOPs, work instructions (WIs), worksheets (WSs), manufacturing processing instructions (MPIs), job aids (JAs), and document links (e.g., SOP hyperlinks to delineate the correct effective dates) intended to be pasted into the continuous data GR&R study template are current and functional when clicked, taking into account the timing of the projected execution dates (e.g., If it is known ahead of time that the SOP hyperlinks transcribed in the proposed preapproved protocol may become obsolete or expired during the projected execution dates of the protocol, then wait to obtain the most effective SOP hyperlinks prior to finalizing the preapproval of the protocol or let QA know ahead of time to wait for the new SOP link to become effective prior to preapproving).
- Ensure the training records for all the involved stakeholders are current and up to date.
- Ensure that a continued educational policy is in place to enable continuous awareness and knowledge transfer with respect to changes in technological applications and intended business uses.
Study Development Phase
To obtain preapproval for executing a continuous data GR&R study (typically, standard gage involves three operators, two replicates, and 10 parts), proceed with the following steps in congruence with all involved applicable stakeholders. Note that “operator” or “appraiser” is the person who routinely works in the manufacturing setting while conducting the measurement of the device/item/part; “replicates” means repeating the same test/measurement one more time, which equates to at least two trials; and “parts” can be devices or any testable items produced in your manufacturing process that can be measured.
- Post-Prerequisite Completion Phase: Ensure that “noncritical gaps” are identified and put in a placeholder (to be saved in a draft summary/final report folder on your computer), such as the operator not being currently trained in the involvement of non-direct-impact SOPs. This can easily be addressed as part of the summary or final report by delineating, as an example, that the “vendor management SOP” does not result in any direct relationship to the operator’s primary duties within their respective job function. Now, you can populate all the necessary attributes/information.2
- Ensure that there are diverse samples/items/parts/device types to represent the various types of variations possible compared to the mean (data) during the manufacturing of part-to-part variation scenarios.
- Label all parts/items/devices in alignment with your protocol’s nomenclature or labeling requirements.
- Ensure that all parts/items/devices are stored in a secure location for which only the study director has the keys.
Execution Phase
The execution phase of the continuous data GR&R study comprises four steps, as outlined below:2
Step 1 of 4: Pre-Training as Part of Readiness
Pre-training refreshes operators on how to execute the continuous GR&R study. We suggest that study directors (who can be validation engineers driving the hands-on project) provide a preliminary 30-minute (or other duration as needed) training session to go over the relevant points of the study for those who will be primarily involved in its execution.
Pay special attention to the points at which operators will need to transcribe information (data), and how they will interpret their understanding of the instructions in alignment with the stipulations of the study protocol, including the interpretation of the acceptance criteria. This training can be documented formally by completing a training form that identifies the intent of the training and subsequently appending the record to each operator’s documentation training file or including it within the study protocol as justification for supplemental training.
Typically, operators know how to do the jobs they are hired for, given their assigned training and tasks. But operators may not at first know exactly how to enter information into the continuous GR&R study data sheets or protocol, since performing any validation activities is never or rarely part of their daily duties.1
Execution Sequence
NOTE: To be repeated for every trial as part of the Gage R&R study
To ensure a successful execution of any continuous data GR&R study in a cleanroom environment, the following sequences are recommended per tasks/roles delineated below:2
Step 2 of 4: Study Director’s Task 1
At a minimum, all parties involved must have sufficient documented training in gowning and entering cleanrooms, with continued adherence to the principles of the company’s SOPs. The study director supervises the test procedure:
- Pick up the items/parts/devices to be evaluated (all in one bag) from their locked location, using a correctly identified bag to relate to the continuous data GR&R study.
- Spray the bag with isopropyl alcohol (IPA) before entering the gowning area.
- Put the bag in the pass-through window between the cleanroom and non-cleanroom locations.
- Close the door of the pass-through and spray more IPA within the pass-through compartment.
- Sanitize the pass-through according to your company’s SOP.
- Enter the operator’s manufacturing suite location by gowning according to your company’s SOP for cleanroom classification requirements. Then pick up the sanitized bag containing all the sample items from the pass-through.
- Position yourself at the relevant cleanroom manufacturing location (e.g., table where the operators and study director can sit), where you will distribute the numerically identified devices/items/parts that will be randomly put in front of the operators (appraisers, etc.) to perform the execution measurement.
Step 3 of 4: Operator’s Task 1
Follow directions specified above pertaining to entering the cleanroom. Reread and understand the entire preapproved continuous data GR&R study protocol. Ensure that you are familiar with the stipulations specified in the acceptance criteria, coupled with an understanding of the instructions stipulated within the section of the protocol for every operator, trial, and respective sizes or device/item/part identifiers.
Step 4 of 4: Operator’s Task 2
In the presence of the study director, one operator at a time will perform the study by filling out a raw data sheet. Each operator assesses/performs the required measurements provided by the study director for each randomized item/part/device using the specified measurement devices according to the respective manufacturing instructions.
Post-Execution Phase
After a continuous data GR&R study has been fully executed, the following step can take place:2
Study Director’s Task 2:
The study director can use a validated version of Minitab (version 17 or later is recommended) or other validated statistical software to enter the raw data that was generated during the execution phase to represent the data compilation of all inputs from the operators (appraisers) so as to obtain the necessary outputs (various graphs obtained by using the two-way ANOVA approach, as an example, reports, etc.).
NOTE: The study director ensures that all input data sheets (for each operator for every trial), including their corresponding metadata, meet good documentation practices (GDPs).
See Part 3 of this series for discussion of the steps and the results of a successful generic case study, including its corresponding graphs, reports and recommendations after the raw data has been properly compiled within the statistical software.
Conclusion
Once you acquire a theoretical/practical understanding of the uses and pertinence of continuous (variable) GR&R studies in a measurement system analysis, including its practical hands-on study design with respect to your manufacturing processes, populate all the input information (raw data) derived from the operators (appraisers) during the execution phase into the protocol data sheets, to be followed by entering the data into Minitab for generating printouts (graphs), or you can directly input the raw data information into Minitab to generate printouts.
References
- Drug Delivery Systems (Part 1 of 3): Measurement-System Analysis Using Continuous Gage R&R Studies by Allan Marinelli and Howard Mann, Drug Delivery Systems Measurement System Analysis Using Continuous Gage RR Studies Part 1 (meddeviceonline.com)
- BioProcess International eBooks,20(9)E1 September 2022 titled “Drug-Delivery Devices: Measurement-System Analysis Using Gauge R&R Studies”, Allan Marinelli and Howard Mann, with Cheryl Scott, Drug-Delivery Systems: GR&R Studies - BioProcess International (bioprocessintl.com
About The Authors:
Allan Marinelli is the president of Quality Validation 360 and has more than 25 years of experience within the pharmaceutical, medical device (Class 3), vaccine, and food/beverage industries. His cGMP experience has cultivated expertise in quality assurance, compliance, quality systems, quality engineering, remediation and validation roles controlled under FDA, EMA, and international regulations. His experience includes quality systems, CAPA, change control, QA deviation, equipment, process, cleaning, and computer validation, as well as quality assurance management, project management, and strategies using the ASTM-E2500, GAMP 5, and ICH Q9 approaches. Marinelli has contributed to ISPE baseline GAMP and engineering manuals.
Howard Mann works as an independent consultant and/or contractor in the operational, regulatory, and quality assurance arenas. He has extensive experience in the healthcare industry and provides technical leadership guidance to the business development process, including the product development process in all areas of GxP compliance.