Dry Blenders for Pharmaceutical Processing
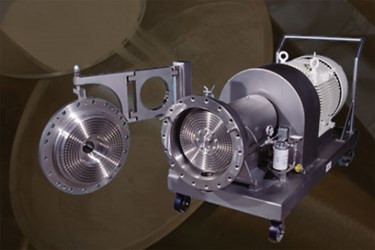
Charles Ross and Son Company offers four types of pharmaceutical dry blenders: ribbon, paddle, vertical, and tumble. There is a type of blender that will be most efficient in each application.
Which design is best for your application?
Ribbon blenders, vertical cone screw and tumble blenders are found in many pharmaceutical plants, and in many ways they perform a similar function on the process line. But the differences in their design - and in the advantages they offer - are far more important than their similarities. The ribbon blender is generally less expensive than a vertical cone screw blender or a tumble of comparable capacity. So, in practical terms, you should determine which your application requires in order to achieve the product quality and processing efficiency that you need.
To decide which type of blender will work more efficiently in your application, ask yourself these questions
1. How much room is available on your plant floor? If floor space is tight, you may have to go up - with a vertical blender - since a vertical blender requires a much smaller footprint. If overhead space is limited, you may be forced to use a horizontal ribbon blender, which allows you to use a low-profile loading system. A multi-level operation is generally unnecessary.
2. Does the friability of your product require gentle blending? If so, you will probably need a vertical cone screw or a tumble blender. The blending action of these designs is extremely gentle.
3. Is complete discharge essential? The cone screw blender or a tumble blender gives you virtually 100% discharge through the lower cone.
4. How tight is your budget for power? Since the ribbon blender consumes more power, over long blending cycles this can add up.
5. Is contamination a critical risk? With a packing gland in the product zone, the ribbon blender poses a greater threat of contamination. New seal designs have reduced the risk dramatically, but if your application requires the best protection available, you will have to switch to a cone screw or tumble blender.
6. Is your product heat sensitive? The blending action of a ribbon can generate more heat than that of a mixing screw or a tumble blender.
7. Will you always operate with the blender at least half full? If you need the flexibility to operate with smaller batches, choose the cone screw blender. Because of the geometry of the cone, this blender can operate efficiently with batches as small as 10% of blender capacity. The ribbon blender generally requires a minimum of 40-50% of full capacity.
8. How fast do you want to finish the batch? A fast blending cycle is not always the most important concern, but it is always a factor you should consider carefully. Cone screw blenders are usually about 30% faster than ribbon blenders in similar applications.
9. Are you concerned about blending accuracy? All produce a well-blended product. If accuracy is critical, be sure to test the blender in the equipment manufacturer's laboratory before you buy it - to prove that it can deliver the product quality you need.
10. Will you need complete cleaning between batches? The cone screw blender is easier to clean, especially since you will never have to disassemble a packing gland in the product zone. Just make sure that the cone screw blender you select does not require a bearing at the lower end of the screw. A screw supported entirely from the top end will give you faster, more thorough discharge, easier cleaning, and fewer maintenance headaches.