Eastern Plastics Demonstrates ULTEM Machining, Bonding Technology
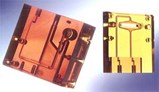
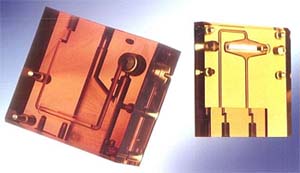
"Diffusion bonding allows OEMs to provide fluidic manifolds where metal and other materials are either incompatible or too expensive," explained EPI Marketing Manager Larry Dawson. "ULTEM is already used for its heat and temperature resistance in sterilization trays, surgical instruments, coffee pots, smokestack analyzers, surgical instruments, and DNA sequencers. Now those same properties can be applied to complex working components."
EPI had been manufacturing multi-layer manifolds for many years from acrylic and PVC. ULTEM—an acronym for "ultimate engineering material"—gives the company a broader materials base which will be especially useful for medical devices and process industries. Engineered channels range in diameter from an inch or more to several thousandths of an inch. At the low end, diffusion bonding can be used to fabricate low-cost plastic microfluidic devices for portable chemical/medical analyzers (labs-on-a-chip). Larger diameters will find uses in process industries, for which EPI can now create precision-channeled gas- and fluid-delivery manifolds that are easy to validate, clean, and combine for gas or liquid distribution/handling or mixing.
Heat, Temperature, Time Replace Adhesives, Gaskets
Making complex, custom manifolds has always been a tricky business, according to Dawson. Gasketing materials (e.g. silicone adhesive) leak, and precision-bonding through adhesives is labor-intensive. "Based on our experience in the medical device industry, we knew there should be very high demand for a manifold manufacturing technique that did not use adhesives or gaskets." Ideally that technique would create multi-layered manifolds by bonding a single material to itself.
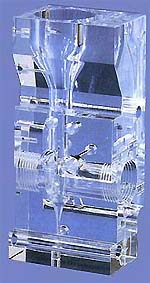
"We came up with a method that used temperature, pressure, and time to bond layers without adhesives or gaskets." EPI's technique requires the manifold first be constructed in layers, which must be super-flat with a very polished surface finish. Once the internal chambers are milled they're placed into a fixture, under pressure, and put into an oven. Dawson explained the resulting bonding as a "molecular fusion" somewhere near the material's softening point.
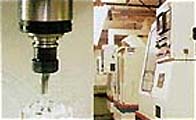
EPI's manufacturing method is part art, part science, and requires a lot of precision. If all goes well manifolds can be constructed with almost any fluidic configuration, with complex-shaped tracks at angles or straight across the final structure. "We can create internal features that could not be made through simple machining or even bonding," Dawson explained, "such as a cylindrical chamber within a manifold. We can also embed mixing and flow features, or even electronic contacts and circuits."
EPI can assist OEMs in the design of a flow schematic and manifold layout. The company also provides complete valve/manifold assemblies fully tested for flow, pressure, leak, and function. Right now materials/engineering considerations limit diffusion bonding to ULTEM, polyvinyl chloride, and polycarbonate, "But we're always experimenting with new materials," Dawson said.
For more information: Larry E. Dawson, Vice President of Marketing, EPI, 110 Halcyon Dr., PO Box 9188, Bristol, CT 06010-9188. Tel: 860-314-2880, ext. 151. Fax: 860-314-2888.
By Angelo DePalma