Equipment Change Control For GMP Production Facilities — Proving It All Works
By Greg Weilersbacher, Eastlake Quality Consulting
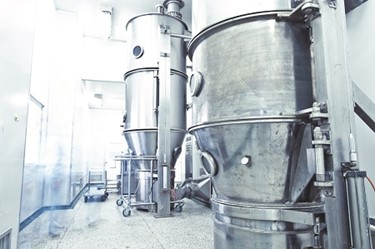
The first article in this two-part series outlined the six primary stages of equipment change control and discussed the first two stages: (1) determining the equipment utility/IT requirements and (2) pre-installation assessment, utility evaluation, and remediation. In doing so, it hammered home the need to fully understand the utility requirements for a new piece of equipment and assess whether utilities can meet the new equipment’s demands. This article describes the final four stages of this process: (3) evaluating the impact of new equipment installation on previously validated utilities, (4) executing validations for new equipment, (5) review of equipment turn-over packages and validation reports, and (6) performing change control effectiveness checks.
Stage 3: Assessing The Impact Of New Equipment On Utility Validations
Adding new equipment to a manufacturing facility is seen by some as a “plug and play” activity: connect equipment to power and you’re off and running. However, in cases where high-purity water, pharmaceutical grade gases, or refrigerant for equipment cooling are needed in cleanrooms that previously did not have these utilities, additional lengths of stainless-steel piping and points of use are required.
In each case, revision to or, at minimum, redline edits to, the facility’s as-built drawings are needed to reflect the change. This should also trigger a change to the utility’s validation protocols. The utility’s installation qualification (IQ) protocol should include schematics for process piping, lengths of each segment, insulation type, connections to equipment, and valves for sampling along with P&ID (piping and instrumentation diagram) numbers. Adding a new autoclave to a production facility, for example, might require an extension of piping from the clean/pure steam generator or water for injection (WFI) system. The validation protocols for the clean/pure steam generator or WFI system require updating, pressure testing of new piping, and testing for purity of steam or water at the points of use. In the rush to complete the commissioning activities, many production facilities fail to address these related impacts or just ignore the need.
I experienced the impact of a contract manufacturing organization’s (CMO) lack of thoroughness in equipment change control during a mock pre-approval inspection I performed for a client. The FDA had identified the CMO as a final dosage form manufacturer for my client’s product, and it was soon to be inspected. My role was to identify problem areas and help the CMO make corrections before the FDA came knocking on the door. The CMO recently installed a new vial washer in a cleanroom located across a hallway from the current vial washer. Installation required adding approximately 30 feet of stainless-steel piping that traveled up one wall, over the ceiling of the cleanroom hallway, and down a second wall to the new vial washer. A sampling port was installed next to the new vial washer at the end of an 18-inch length of pipe that connected to the main WFI supply line.
I reviewed the WFI validation and identified the problem. The WFI system was installed and validated nearly a decade earlier and the drawings of the distribution piping reflected the system as it was built (i.e., had not been updated to include the 30 additional feet of piping and the new sampling port). Strike one. A little more digging revealed that the SOP for WFI sampling and testing had not been revised to include the new WFI sampling port and the new port had not been given a P&ID number. Strike two. This resulted in failure to sample and test the new sampling port since the vial washer’s commissioning. Once the CMO was notified of these issues, it tested the new sampling port and received failing results. Further investigation uncovered the source of the problem: The 18-inch pipe that connected the sampling port to the main WFI line was a dead leg (e.g., pipe length too long to allow for proper water circulation). Strike three. The CMO could have prevented these problems by implementing detailed equipment change control, which should have required updating the WFI validation and performing regular testing of the new sampling port.
Stage 4: Calibration/Validation Of New Equipment
When calibrating equipment, it is important that the calibration match or exceed the intended operational range of the equipment that will be used during actual production activities. Too often, equipment is operated at RPMs, flow rates, compression forces, etc., that exceed the lower or high-end calibrated range of the equipment. This is a common audit observation made in sponsor and regulatory inspections of production facilities.
Requirements for validating equipment should be detailed in a validation master plan (VMP) that outlines the quality requirements for the types of equipment already in-house. The VMP defines the systems, equipment, methods, and facilities that are in the scope of the plan; compliance requirements for validation, including how the validated state will be maintained; required validation deliverables; and the validation risk mitigation strategy. Equipment-specific validation protocols must follow the requirements of the VMP, whether written in-house or provided by the manufacturer or installation company. Deviations from the VMP requirements are common audit observations by regulatory agencies, as manufacturers’ validation protocols are too often approved without careful comparison with the VMP.
Equipment change control should reference the requirements for calibration and validation detailed in the VMP. The challenge arises when a state-of-the-art piece of equipment is purchased that is not within the scope of the VMP. In this case, the most compliant and thorough course of action is to review the equipment manufacturer’s validation package and identify IQ, operational qualification (OQ), and performance qualification (PQ) gaps for the intended use of the equipment. The equipment change control should reference both the manufacturer’s validation package and the gap validations that you will perform. Note that in all cases, the manufacturer’s validation protocols and your internal gap validation protocols must be approved by the equipment owner, validation, and quality prior to executions. The VMP should also be updated to include the validation requirements for the new equipment.
Stage 5: Review Of Turn-Over Packages, Executed Validations/Data/Reports; Release Of equipment For GMP Use
A turn-over package (TOP) is a set of documentation provided by the equipment manufacturer that provides the foundation for equipment validation. The TOP generally includes a factory acceptance test (FAT), a site acceptance test (SAT), and materials of construction and identification of product contact surfaces. The FAT is performed by the manufacturer at the manufacturer’s facility and verifies that the system and its components are configured correctly and function properly in compliance with the equipment design and/or the customer’s specifications. The SAT repeats this work, or a subset of tasks, after the equipment is installed and can be performed by the manufacturer or the end user.
Identification of the equipment’s product contact surfaces and their material types is critical for writing cleaning verification/validation protocols and SOPs. Most manufacturers provide this information, but some do not. For those that do, the names of each product contact part, along with their measured areas (cm2), are needed to define surfaces to swab for cleaning samples. If the manufacturer can’t or won’t provide this information, your engineering department should take on this task and attach documentation to the change control.
Content, Approval, and Execution of Validation Protocols
It’s in the validation of equipment that you prove to yourself and to regulatory agencies that the equipment operates as intended. Installation, operational, and performance validation protocols (IQ, OQ, and PQ) capture these requirements. The end goal is to demonstrate that the equipment not only conforms to the manufacturer’s and end user’s specifications but also that the equipment is appropriate to manufacture the intended product. It’s likely that new equipment will meet IQ and OQ requirements and also those of a generically written PQ but fail in GMP production settings if the unique needs of the product are not included in the PQ.
For example, if your company’s manufacturing batch record requires producing high-quality tablets (i.e., low number of rejects) at a rate of 800,000 units per hour, but the new tablet press yields high numbers of broken tablets at production speeds exceeding 600,000 units per hour, you will have a production deviation with a serious impact on product quality. As a rule of thumb, evaluation of equipment validation deviations should always include the impact on the products that will be made with the equipment. This is especially challenging for equipment intended to be used for multiple products.
Review of Executed Validations
This stage in the change control process is often treated as a rubber-stamp activity: Get quality to sign off quickly so the equipment can be used. This review, however, is an extremely critical phase where issues, gaps, and deviations are identified and remedied with input from quality, engineering, validation, and department owners. The goal is a complete set of documentation that delivers confidence that product will be made correctly and reliably. Take time to address every issue.
Substitution of Components
Validation protocols may incorrectly identify a component, or the manufacturer may have substituted a different component during assembly. For example, if a mechanical valve was substituted, the replacement valve should be of the same type (i.e., ball, butterfly, check, sanitary, constant flow, diaphragm, etc.), size (internal and external diameters), and materials of construction. Ensure that the manufacturer provides drawings and specifications for the replacement component. The job of the reviewer is to ensure that the substitute component matches the specifications of the original component. If specifications don’t agree, a deviation should be written and scientifically justified.
Don’t Fear Deviations
It is fairly rare for validations to be executed without some type of issue. Actual humans write validation protocols, and humans make mistakes. It’s the completeness of the investigation and clarity of wording that makes all the difference.
A well-written protocol deviation should have the following components: (1) statement of test result and comparison to protocol requirements, (2) impact of the deviation on equipment performance expectations (e.g., operating ranges, pressures, flow rates, temperature ranges, and operating parameters listed in production batch records), (3) whether errors were made in authoring protocol requirements and how changing the original requirements can be justified, (4) review and approval by subject matter experts and quality. All participants should agree with the details of the deviation, justification, and conclusions. If not, discuss and rewrite the deviation. It’s important to remember that the deviation should stand on its own (i.e., without further explanation) many years after it has been approved.
A common mistake is forgetting to provide a written statement certifying that the equipment is now released for GMP use. The statement of release is an expectation of European QP (quality person) audits. Without this written statement, the equipment should not be used in GMP.
Stage 6: Change Control Effectiveness Check (Or, What Did We Miss?)
An effectiveness check is a valuable tool that can be used to identify equipment commissioning and change control gaps to prevent the same issues from happening in the future. In reality, this is rarely performed, as staff members are quickly redirected to the next piece of equipment to commission. When this happens, speed bumps and potholes are never leveled and filled, and the company inevitably repeats the same failures over and over again.
A robust change control effectiveness check should be built into the company’s equipment commissioning process as a required step. The change control effectiveness check should ask the following questions: Were protocol specifications set correctly? Were the manufacturer’s equipment capability claims valid? Was the equipment’s utility requirement correctly identified prior to validation? Did all utility capabilities meet expectations?
The Takeaway
The goal in equipment change control is not simply to approve the use of a new piece of equipment. The goal is to provide a thorough documentation trail that supports the conclusion that equipment works properly, meets requirements of the product you will manufacture, and does not negatively impact GMP utilities that supply electrical, water, and gases to other equipment that may be used simultaneously. This is not easily accomplished and requires coordination of engineers, manufacturing operators, facility mechanics, and quality. The guidance provided in this series will help you to implement an equipment change control system that instills confidence in the quality of the equipment used in your facility.
About The Author:
Greg Weilersbacher is the founder and president of Eastlake Quality Consulting, a GMP consulting firm based in Southern California. Over the last 25 years, Weilersbacher has held director and VP positions leading quality assurance, quality control, analytical chemistry, materials management, GMP facilities, and product manufacturing in biotech and pharmaceutical companies. His unique experiences and technical background have led to the manufacture and release of hundreds of solid oral, sterile, and biologic investigational products to clinics in the U.S. and abroad. Weilersbacher can be contacted at weilersbacher.greg@gmail.com.