Equipment Validation In The Pharmaceutical Industry
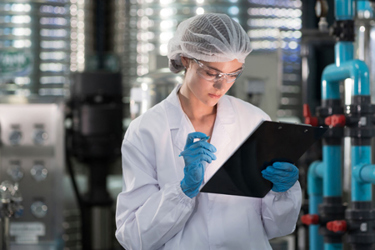
Equipment validation is essential in the pharmaceutical industry to ensure that manufacturing, testing, and production equipment consistently meets predefined quality and regulatory standards. It ensures compliance with Good Manufacturing Practices (GMP) and safeguards the reliability of pharmaceutical products, preventing defective outcomes that could jeopardize patient safety. Regulatory agencies, such as the FDA, mandate a risk-based approach to validation, focusing on equipment with the highest impact on product quality.
The equipment validation process typically follows three critical stages: Installation Qualification (IQ), Operational Qualification (OQ), and Performance Qualification (PQ). IQ verifies proper installation according to specifications, OQ ensures the equipment operates within predefined parameters under all conditions, and PQ tests the equipment’s performance in real-world scenarios to confirm consistent quality.
Ongoing requalification and periodic reviews ensure equipment continues to meet regulatory requirements and maintains consistent performance over time. Laboratory equipment used for testing pharmaceutical products also undergoes validation to guarantee accuracy and reliability in results.
Digital equipment validation has revolutionized the process by improving efficiency, accuracy, and compliance. Digital tools offer real-time traceability, reduced errors, faster cycle times, and streamlined audit readiness, while adhering to ALCOA++ principles for data integrity.
By implementing a structured validation process and leveraging digital solutions, pharmaceutical companies can enhance operational efficiency, maintain regulatory compliance, and ensure the safety and quality of their products. For a comprehensive understanding, explore resources and tools to optimize equipment validation processes.
Get unlimited access to:
Enter your credentials below to log in. Not yet a member of Pharmaceutical Online? Subscribe today.