Evaluating Methodologies For Cooling Submersible Wastewater Pump Motors
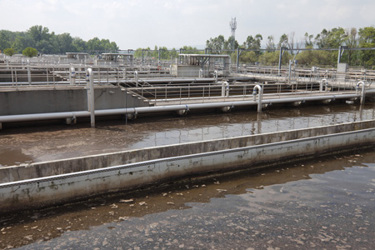
Compare two primary cooling methodologies for submersible wastewater pump motors: oil-filled and closed-loop cooling (CLC). Efficient cooling is crucial in preventing motor overheating, maintaining efficiency, and extending component lifespan.
The oil-filled solution uses dielectric transformer oil to transfer heat from motor windings to the housing, ensuring effective cooling. This method also provides constant lubrication for bearings, reducing maintenance and enhancing longevity. Tests indicate that oil-filled motors run up to 40°C cooler than CLC motors, leading to greater efficiency and reduced wear on components. Additionally, they offer better seal leak detection, allowing early intervention before significant damage occurs.
In contrast, the CLC system circulates a propylene glycol solution through a heat exchanger to dissipate heat. However, this approach has drawbacks, including added complexity, potential for leaks, and increased heat retention, which raises winding resistance and decreases efficiency. The CLC system also requires additional protective measures to prevent contamination if a seal fails.
Overall, the findings suggest that oil-filled motors offer superior cooling, longevity, and cost-effectiveness. They simplify maintenance, reduce failure risks, and provide better early leak detection, making them a more reliable choice for submersible wastewater pumps.
Get unlimited access to:
Enter your credentials below to log in. Not yet a member of Pharmaceutical Online? Subscribe today.