Experts' Advice On Facility Design And Construction

By Tyler Menichiello, Chief Editor, Bioprocess Online
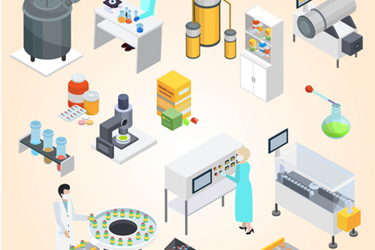
Last week, I hosted the Pharmaceutical Online Live event “Facility Design And Validation Considerations For Drug Manufacturers.” The hour-long panel discussion featured biopharmaceutical facilities design expert and Bioprocess Online contributor Herman Bozenhardt, along with his son, Erich Bozenhardt, associate director of process engineering at United Therapeutics. They were joined by Fred Grossfeld, director of process architecture at Jacobs.
The panelists explored key considerations and common oversights around single-use systems, modular facility design, HVAC, and utilities. Below are some of the most valuable takeaways from the event.
What To Consider When Designing For Single-Use
Design Around Maintenance And Cleaning
When designing the layout of a facility, “maintenance access is critical,” said Grossfeld. Whether it’s for fixed equipment or single-use reactors, cleaning and maintenance access should be thought about and prioritized in the design phase. Herman Bozenhardt shared an unfortunate story about a stainless-steel tank with an 18-inch swing hatch on top — but the tank was only 12 inches from the ceiling. “So guess what?” he said, “They could never open the swing hatch to go inside and inspect the vessel.”
Erich Bozenhardt suggests letting maintenance staff review a facility during the design phase to avoid these kinds of failures. “At United Therapeutics, we invite our maintenance staff into those [planning] sessions so they can go into the 3D model,” he said.
It’s no secret that cleanliness is critical in a biomanufacturing environment, and a commonly cited advantage of SUS facilities is not having to go through cleaning validation. While this is true for entirely SUS, “it’s hard to get a 100% SUS,” said Erich Bozenhardt. Regardless, even a hybrid SUS approach can reduce the time and resources spent on cleaning validation — or cleaning in general. And while this is appealing, it’s important not to overlook how difficult it can be to manage SUS waste. Single-use bioreactors may arrive at your facility very neatly packaged and compact, but they don’t end up that way.
“After you use them, they do not go back down to that same size,” Erich Bozenhardt said. “If you have a 5,000-liter bioreactor, you’re going to have a very large, cumbersome bag and tubing set to somehow package up and contain before you move it out of the suite.”
Accelerating Construction With A Modular Approach
The conversation shifted to facility construction — specifically, to the merit of a modular construction approach. Herman Bozenhardt and Grossfeld recalled their time working on a facility for Locus Biosciences and how they opted for a modular approach in which a nearly complete cleanroom was delivered to the site — complete with walls, ceilings, doors, HEPA filters, light fixtures, etc.
“There’s a lot of advantages to using a modular system like that,” Grossfeld said. Perhaps the biggest, the panel agreed, is a significant reduction in the logistical complexity that comes with having multiple trades on-site for a stick-built facility. “You have a framing contractor, you have a drywall manufacturer, you have finishers for the drywall,” Grossfeld explained. With a turnkey modular design, you only have one source to communicate back and forth with. Not to mention that “it is very messy work” building a cleanroom in the field, he said.
The goal should be to have as many components fabricated in a factory as possible, according to Grossfeld. “It’s far more precise,” he said. “The level of cleanliness and the level of finish is far better than a field-assembled system.”
The speed of construction is another benefit to modular design. “The erection time was unbelievably short,” Grossfeld said about the Locus facility. “These things, they go together like Legos,” Herman Bozenhardt chimed in. This not only allows for fast construction, but flexible construction. “You can actually unbutton them and put in a new piece of equipment, or you could reconnect and rebuild them,” he explained. He described how his team unbuttoned the back of a whole fill-finish room, brought new equipment in, and put it back together in the span of a couple hours.
While there are clear benefits to modular facility design, there are tradeoffs to consider — mainly, the premium cost and upfront planning involved. “You have to know what you want and define that very early on,” Erich Bozenhardt said. This means having to spend time coordinating the location of utilities and chases earlier than you normally would with a stick-built facility, Grossfeld said. And while the costs are more expensive, “the savings in labor offsets that,” Bozenhardt said. “Overall, you’re probably still going to pay more for it, but you’re getting a much, much better finished product.”
Aligning HVAC Specs With An Appropriate Biosafety Level
One of the biggest challenges people encounter in facility design and construction is getting the HVAC correct, according to Herman Bozenhardt. HVAC systems are a critical aspect of any bioprocessing facility’s containment, as they capture and eliminate contaminants using air pressure. Bozenhardt lists the top three functions of a robust HVAC, which are to:
- Protect employees from dangerous biological entities or potent compounds
- Protect the environment from contamination
- Protect the product from being contaminated or reinfected
He went on to describe the major differences between different HVAC biosafety levels (BSL):
- BSL-1 involves normal GMP gowning in accordance with Annex 1, along with positive air pressure. “You can use basic good lab or GMP practices,” he said. BSL-1 is generally for organisms like E. coli or “simple little guys like that.”
- BSL-2 focuses a bit more on recirculation using HEPA filters for incoming and outgoing airflow. “We see a lot more of [BSL-2] now,” Bozenhardt said, as it is better at containing therapeutic biologics and vaccines. BSL-2 offers a continuous means of cleansing the environment to minimize contaminants.
- BSL-3 is for “far more dangerous and exotic agents that can cause serious lethal disease due to inhalation,” Bozenhardt said.
- All Bozenhardt had to say about BSL-4 was that “you better be careful.”
It’s important to understand which BSL level applies to your production and base your HVAC system on the relevant regulations. Municipalities and countries have a lot of say on which BSL or HVAC system is necessary, so it’s important to engage local regulatory authorities about which containment is needed for your facility. In the United States, this includes agencies like the CDC, NIH, National Institute of Allergy and Infectious Diseases (NIAID), and the Environmental Protection Agency (EPA).
Consider Utilities Early In Planning
When it comes to managing utilities and their implementation during facility construction, a well-informed construction manager who can offer guidance is invaluable, said Erich Bozenhardt. The most-important utilities for a biopharma manufacturing facility are process and purified water systems, compressed gases, steam, and HVAC systems, but underpinning almost all of these is a stable and protected power supply. As such, your facility’s electrical switchgear (the equipment that manages power distribution throughout a facility) is critical for operations. If there is a delay or challenge with implementing a facility’s switchgear, it can negatively impact the construction timeline and push out commissioning and qualification, Erich Bozenhardt said.
Ultimately, the process is going to drive a facility’s utility demand, Grossfeld said. “Whether it’s water for injection (WFI), clean-in-place (CIP), or compressed air — whatever the case may be — the infrastructure has to be evaluated and analyzed very early in the overall design,” he said. “If you plan ahead and make sure you evaluate the existing infrastructure of the facility, that will save a lot of grief and a lot of cost in the long run.”
If you’re interested in hearing more from this conversation on facility design and construction, you can watch the entire event recording here thanks to our event sponsor, AES Cleanroom Technology. And if you want to continue down the rabbit hole to learn more about facility design, maintenance, and operations from the Bozenhardts, you can now buy their recently published book, “Commercial Biotechnology: Practical Guidance for Engineering, Operations and Maintenance.” They are long-time contributors of Bioprocess Online, and this book is a collection of those articles. You’re sure to find plenty of wisdom in those pages!