Flameless Thermal Oxidation: The Whats and Wherefores
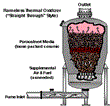
Flameless thermal oxidation* (FTO) is a technology designed for the destruction of organic gases and vapors emitted from a variety of manufacturing operations and hazardous-waste treatment processes. FTO reaction temperatures in the normal operating range typically result in CO emissions of less than 10 ppmv and thermal NOx emissions of around 2 ppmv.
The Nature of FTO
Thermal oxidation of organic compounds in a gas stream takes place in a refractory-lined reactor filled with inert random ceramic packing, as shown in the accompanying figure. The packing is spherical and saddle-shaped with typical sizes being 1 to 2 in. (2 to 5 cm). Burners are used to preheat the ceramic bed but are not used during waste-gas processing.
The FTO process founds on a commercially proven and patented "destruction matrix" that separates and enhances the processes of mixing and oxidation. The matrix is a carefully designed volume of porous inert media selected for its thermal- and flow-distribution properties.
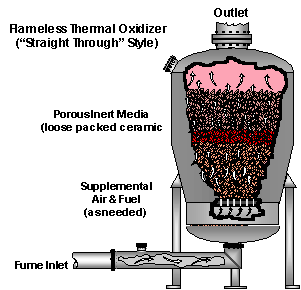
Premixing and reaction can be optimized separately in the process, thereby eliminating the forced coupling that these divergent processes experience in a flame thermal process.
In a flame device, the right time, temperature, and turbulence must be achieved simultaneously to obtain desired levels of organic-compound destruction. The matrix design, however, with its large thermal mass and outstanding radiation and convection characteristics, promotes temperature homogeneity both in time and space.
In flameless thermal oxidation, the fast chemistry of premixed combustion (less than 50 ms) at normal operating temperatures of 1750° F to 1850° F (950° C to 1010° C) results in complete mixing of the gases before they reach the reaction zone. Thus temperature alone governs destruction. Also, enhancing the complete mixing, the plug-flow nature of flow through the matrix establishes a stable, self-sustaining reaction wave across the flow axis.
In the reaction zone, the matrix both absorbs and radiates heat generated by combustion of the organic compounds. This provides both the required thermal driving force to initiate the reactions and an energy-storage capacity that acts to stabilize these reactions even with varying flows and inlet VOC concentrations.
The matrix is non-catalytic and therefore impervious to poisoning or sintering, ensuring predictable and repeatable operation. Also, in contrast to catalytic oxidizers, pressure drop across the system is very low due to the high void space ratio (70%) in the matrix.
A standard hydrocarbon VOC fume stream is "self-sustaining" (requiring no supplemental fuel). For organic-rich or oxygen-deficient streams, dilution air is mixed with the fumes to maintain the matrix at desired operating temperatures. For lean-fume streams, supplemental energy (fuel) is added to maintain the oxidation reaction.
The uniform temperature in the reaction zone and the uniform flow across and through the reaction zone produce the consistent exposure of combustible compounds to oxygen. Also there is small possibility of waste constituents' bypassing the radical-rich reaction zone. Thus, under normal operating conditions, removal efficiencies exceeding 99.99% are possible.
Efficiency Breeds Safety
The process characteristics that make FTO highly efficient also contribute to its inherent safety.
The fixed-bed non-catalytic matrix permits destruction of organic compounds at concentrations at levels lower than their respective lower flammability limits (LFL).
Moreover, the large thermal mass (inertia) of the ambient mixing zone adds to system safety by acting to prevent flashback.
The thermal inertia of the matrix also allows for a manageable thermal response to process upsets should they occur.
FTO controllers have more time (several seconds to minutes) to respond to temperature changes in the FTO process compared with the fractions of a second for flame-type units.
For all of the aforementioned safe features, FTOs are desirable in areas with Class I, Division 2 electrical classification (flameproof).
Acceptability
The U.S. EPA in a status report has described the FTO as a non-incineration technology.
The permitting history of FTO systems is striking for its consistency, speed, and success. Construction and operating permits have been granted in widely differing process operations. In many cases, these permits have been granted in fewer than 30 days.
Regulatory agencies have referred constituents to FTO technology for difficult applications that require high destruction.** In some cases, states have authorized the installation of an FTO system by exemption to permit installations requiring extremely low emissions.
Permits for flameless oxidizers have been issued in Canada, England, Ireland, The Netherlands, Taiwan, and several states—including California, Connecticut, Idaho, Kentucky, Louisiana, Maryland, Mississippi, New Jersey, New York, North Carolina, Ohio, Pennsylvania and Texas.
Permits for conventional flame-based incinerators may require a continuous emission monitor (CEM) to verify performance during operation. Typically, FTO units do not require a CEM, and temperature is the only monitored process parameter required to verify performance.
Valued Attributes
FTO technology and associated unit operations provide a cost-effective, robust, and high-performance, air-toxics pollution-control system. FTO technology has demonstrated that it can provide:
- 99.99% destruction and removal efficiency,
- an extremely low NOx emission,
- an extremely low CO emission, and
- an attractive cost of operation.
Plus, for intermittent operations, or overnight or weekend shutdown, airflow through the insulated reactor can be significantly reduced to help maintain appropriate temperature profile. This operational "ready idle" mode, reduces operating costs and prolongs system life by minimizing thermal cycling.
* Thermatrix patents the Flameless Thermal Oxidation process
** The Thermatrix FTO is listed on the Texas Natural Resources Conservation Commission Innovation Technology Program.
The previous article was adapted from an extract of paper 99-55, "A Case Study: for the Safe, Efficient Destruction of Phosgene," presented at the Air & Waste Management Association's 92nd Annual Meeting & Exhibition, June 20 to 24, 1999, St. Louis, MO.
About the Authors
Susan DesJardin is with the Thermatrix Diesel Systems Division at 2025 Gateway Place, Suite 132, San Jose, CA 95110.
Mike Barkdoll and Robert Manseill are employed at the Thermatrix Inc. facility at 308 N. Peters Road, Suite 100, Knoxville, TN 37922.