For Gilead, Sustainability Is More Than A PR Effort

By Tyler Menichiello, Chief Editor, Bioprocess Online
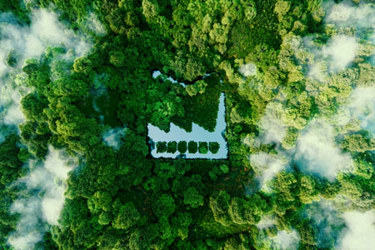
“Sustainability” is a shiny word. It makes us feel good, conjuring images of green forests, clear waters, smog-free skylines, and positive trend lines in corporate slide decks. But beyond compelling headlines and inspiring conference sessions, what does sustainability actually mean for the biopharma industry? What does it look like in practice? How can advanced therapy manufacturing become more sustainable?
I was fortunate enough to dig into these questions with Joydeep Ganguly, the chief sustainability officer and SVP of operations at Gilead. To Ganguly, sustainability is more than lofty goals and corporate jargon. It’s an attitude.
“Companies that do it well do it as part of the culture,” he says. Ganguly explains Gilead’s cultural focus on sustainability and how it influences everything from R&D to manufacturing.
Greener Processes Start In R&D
Ganguly believes in embodying this philosophy from the earliest stages of development. “The toughest thing to do when you’re in early phase is to try and look at green chemistry, green biology, or other ways of developing the process to reduce waste, but that’s when you get it done,” he says. Once a process is commercialized, retroactively improving it or making changes is exceedingly difficult.
In the spirit of designing environmentally conscious processes from the start, Gilead co-locates its R&D and in-house clinical manufacturing all in one site. Ganguly uses the term “frictionless tech transfer” to describe this setup. “There needs to be zero inertia as a molecule moves from early phase to late phase,” he says. “By retaining internal research and clinical manufacturing in-house, we’re able to fine-tune the process not just for efficiency and optimality, but for sustainability.”
Using AI, ML To Optimize Energy Consumption
Advanced technologies like AI, ML, and real-time monitoring sensors offer the quickest, most impactful ways to reduce the industry’s carbon footprint, according to Ganguly. Gilead uses these tools to build predictive models that provide insight into energy consumption and process efficiency.
“Building energy signatures of your process is one of the best use cases of these advanced technologies,” he tells me. These models create a sort of “heat map” for processes to reveal and understand where inefficiencies or “hot spots” are. In one example, he explains, “We used years of data to predict how long batch processes function and create an energy signature, and we used that to optimize the process. This led to over a million dollars a year in true energy savings, let alone the fact that the process became more consistent.”
Predictive energy models can also be used to detect variance in energy use across the company’s manufacturing sites — i.e., the delta in actual energy use versus the predicted use. When a discrepancy is found, a technician is deployed to address the issue. This has saved Gilead an estimated $400,000 in energy costs and decreased its annual energy waste by approximately 2%. “It goes back to the notion that good environmental hygiene is good for business,” says Ganguly.
These technologies can also be applied at a macro-level. “Within a global network of sites, you are able to very easily compare the same process at different sites,” Ganguly explains. This allows companies like Gilead to establish equivalence among its different manufacturing sites. “Eventually, I see these kinds of tools driving location strategy,” he says.
The Way Forward Is Collaborative, Not Competitive
It shouldn’t come as a surprise that pharma is being outpaced by other industries on the sustainability front. “Because we have a patient at the end of our supply chains, we kind of feel as though we already have a social impact, and we don’t focus on sustainability with as much vigor as we do drug supply,” Ganguly muses. Obviously, drug supply is imperative, “but that cannot be the excuse for having a complete operational network design that is creating more problems.”
Like anything worthwhile, transforming pharma into a more sustainable industry will take time and resolute commitment towards numbers, says Ganguly. It will certainly take more than a few green initiatives at a handful of companies. As a whole, Ganguly believes the industry needs to have more authentic conversations around sustainability. Too often, the dialogue is superficial and focused on recognition — corporate virtue signaling and flaunting green initiatives. “Let’s have more practical use-case based discussions,” he says.
Ganguly thinks real change can be achieved through collaboration across the industry. “This is not something we should compete on,” he says. “We compete on commercialization and innovation, but in the end, the planet’s not going to care who came first in net-zero emissions.” The way forward is by sharing best practices, innovations, and infrastructure — and the time is now. I think most would agree with Ganguly that, “If in 2030 all we’re doing is revisiting our pledges, that would be disappointing.”