Frequent Deficiencies In GMP Inspections, Part 3
by Lea Joos, The Government of Upper Bavaria
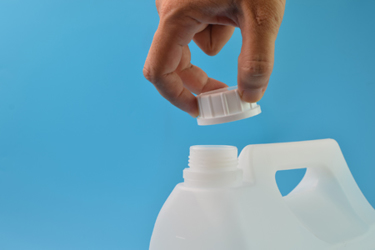
Part 1 of my article series dealt with inadequate handling of deviations and changes. Part 2 discussed deficiencies in cleaning validation. In this article, I share insights on frequent deficiencies regarding labeling of cleaning materials.
Inadequate Cleaning Materials Labeling Can Lead To Contamination Risks
The deficiency: The change management procedure specified that changes had to be approved before implementation. In accordance with the procedural instructions, a so-called Change Control Committee (CC Committee) should be convened for a decision. The exact composition of this CC Committee was not specified. According to company information, the composition varied depending on the change request. It was therefore unclear how to ensure that the necessary persons were involved, e.g., qualified person, head of production, or responsible person for wholesale distribution. Furthermore, the implementation of the measures defined by the CC Committee could not be traced from the change documentation viewed, although the change request had already been completed at the time of the inspection. An inspection of the effectiveness of the change also was missing.
(Ref.: EU GMP Guide Part I No. 1.4 xii, xiii and Annex 15 No. 11.5 and 11.7)
What Was The Problem?
Cleaning and disinfection procedures must be effective. For this purpose, suitable materials are selected and the procedures are validated. Cleaning and disinfection must not in themselves be sources of contamination.
In the present case, use of detergents and disinfectants continued after they were opened. The date of opening was not indicated. The shelf life of these cleaning and disinfecting agents after opening was only partially known to the company. Therefore, it was not always possible to verify whether any shelf life was observed after opening.
If cleaning agents or disinfectants are reused after opening or used beyond the shelf life specified by the manufacturer, even though reuse involves the risk of germ contamination, for example, this can contribute to the contamination of surfaces or personnel instead of cleaning.
The situation is similar with the use of cleaning materials. If contaminated cleaning materials such as wiping cloths, brushes, or sponges are used in the cleaning process, they also represent a source of contamination. It must therefore be ensured that there is no danger of confusion between cleaned and contaminated cleaning materials, but that they are clearly labeled and can be identified as cleaned or contaminated.
The Most Common Pitfall
Setting different use-by periods for each cleaning and disinfection agent is often perceived by companies as a challenge and, sometimes, e.g., in the production of non-sterile drugs, also as not necessary. Especially in the non-sterile sector, the effort involved is often perceived as much greater than the possible benefit.
The labeling of cleaned and contaminated equipment is often performed for production equipment but not for cleaning equipment. This is because it involves additional documentation and organizational effort, which would be performed mainly by external personnel who frequently change out and would have to be paid for by the company because of the time involved — without the company recognizing the direct benefit of this measure.
How To Avoid This Error
The cleaning process is subject to a wide range of influencing variables, especially when performed manually. In order to reduce the variability, these influencing variables are defined in process instructions and checked for effectiveness in the cleaning validation.
Variables are often regarded as givens, which are not sufficiently defined.
For example, if you need to use a recycled wipe or brush in the validation, the individual recycled wipes or brushes may not be comparable in terms of cleaning power.
Before using recycled wipes, the risks associated with reprocessing must be identified and assessed in a risk analysis. Possible risks are shown in Figure 4.
Figure 4: Risks of reuse of cleaning materials already used and contaminated
Some of these risks can be reduced by validating the reprocessing process, e.g., microbial contamination. However, the loss of cleaning properties, for example, through abrasion, is a risk factor that cannot be minimized by a validated reprocessing process. It must therefore be considered in the context of cleaning validation: Does my cleaning material always clean equally well after the first, sixth, or umpteenth reprocessing or reuse?
When you then check the cleaning power of the reprocessed or reused cleaning material, you may find in the cleaning validation that you can reprocess or use it 10 times before the cleaning power decreases too much and impairs the cleaning success. This validated condition must then be monitored.
You may also find that monitoring of reprocessing cycles is not necessary for the cleaning step being checked.
Nevertheless, you will probably perform cleaning as part of cleaning validation with clean materials and not with contaminated ones. This means that you must also ensure that the validated condition, cleaned cleaning material is used for cleaning, can be met.
Let your imagination run wild in monitoring compliance with the validated conditions:
- We need a separation of cleaned and contaminated cleaning material — how is this most pragmatically possible?
- We need to monitor the number of cycles of the wipes — what are the options and what is practically feasible?
Also, talk to the personnel involved: the cleaning staff, the reprocessing company, and the people in the company who are directly involved.
You will certainly find a creative solution that keeps the time involved within limits, e.g., the use of adhesive dots to monitor the reprocessing cycles or different colored boxes for pure and impure wipes.
You should ask yourself similar questions for cleaning and disinfecting agents that are to be used after opening: If the manufacturer does not provide any information or you want to use the cleaning and disinfecting agent after the specified use-by period, does the cleaning and disinfecting agent clean and disinfect equally well after opening, after six weeks, or after 12 months?
And if you have determined effective disinfection up to four months after opening during the cleaning validation process, then monitor compliance with this validated condition using the most practical solution for you.
Figure 5: Traceability of the status labeling of cleaning material
This article is an excerpt from GMP knowledge contained in the online portal GMP Compliance Adviser, which provides in-depth information about GMP best practices and regulations with a focus on Europe, but also referring to the U.S., Japan, and international organizationsPIC/S, ICH, WHO, etc.
About The Author:
Lea Joos has worked as a GMP inspector for the government of Upper Bavaria since 2012. Her tasks include the monitoring of GMP and GDP operations as well as tissue facilities for pharma companies. After studying pharmacy, Joos initially worked as a research assistant at the Ludwig Maximilian University in Munich. In 2012, she began her career with the authorities. Since 2015, she also has acted as a speaker on GMP and GDP topics. She can be reached at lea.joos@gmx.de.