GSE Systems Releases BatchCAD 7.0 Process Software
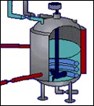
Contents
Introduction
Success Stories
Technical Specifications
About GSE Systems
Introduction (Back to Top)
GSE Systems Inc. (Columbia, MD), which provides real time simulation and process control solutions to the energy, process, and manufacturing industries, announced on October 4 the release of BatchCAD 7.0, its dynamic simulation software for the design and analysis of pharmaceutical, fine, and specialty chemical processes. Release 7.0 upgrades the operating platform from Windows 3.1/DOS to Windows NT, bringing BatchCAD in line with other leading simulation packages. BatchCAD 7.0 also incorporates improvements to the programs toolkit, thermal engine, and other capabilities.
BatchCAD 7.0 combines thermodynamics, reaction engineering, and advanced numerical methods with proprietary kinetic regression algorithms to create a unique modeling environment for chemists and engineers. Already widely used for process scaleup and technology transfer by batch chemists in the fine chemical/pharmaceutical industries, BatchCAD can reduce time to market through effective use of simulation rather than experimentation.
BatchCAD helps process engineers develop new processes and optimize established ones. During the experimentation cycle the BatchCAD accepts data from a limited number of experiments, suggests further in silico experiments, and runs those processes using user-defined inputs. Eventually, data is fed into BSE's VirtualPlant software, which performs scaleup simulations and helps establish process parameters. "Virtual experimentation and modeling sets BatchCad apart from other programs, said Brian Southern, a senior VP at GSE. "BatchCAD assists in simulation modeling at the very early concept and discovery stages, but also enables full-scale production through VirtualPlant."
BatchCAD combines kinetics and thermodynamic functions with a library of reactor models, offering a robust, viable view of how a reaction will take place in a particular piece of equipment. That's important information if process changes are contemplated.
"Many engineers can't really predict the effects of, say, temperature or pressure changes except for what they know from past history," Southern said. "BatchCad opens up the black box, enabling true modeling without doing that many experiments. In other words, you can blow up the simulator 1000 times without hurting anybody."
"BatchCAD is now a key element in our VirtualPlant strategy," stated Chris Carnavos, president and CEO of GSE Systems. "BatchCAD provides an exceptional tool for process development and constitutes an essential component of GSE Systems Virtual Plant. BatchCAD provides a complete understanding of the key unit operations, making the escalation to a complete 'Virtual' operation closer to reality than ever before."
- AGFA Gevaert was manufacturing a new speciality product involving a complex and highly exothermic catalytic peroxidation of mixed thioethers to sulfones. In the past, this reactin was known to runaway. The company was faced with a difficult scale up and control problem, with a requirement to demonstrate to their toll manufacturer that the process could be operated safely. Using BatchCAD simulation, the company achieved safe scale up with substantial cost saving.
Agfa Gevaert's peroxidation process - The Aromachem division of CPL Aromas plc use BatchCAD simulation freely throughout the development of new synthetic routes for fragrance chemicals. Conceptual modelling of reactions is used to give insight into the chemistry of the process, to identify key experiments to promote the desired reaction path and for strategic experimental planning. BatchCAD is used to predict conditions to optimise chemical yield, and identify key experiments. The technique is very effective and the company reports achieving simulated yield improvement in 20 minutes.
- Associated Octel were installing two new multi-product reactor facilities and intended to operate their own processes: bromination reactions in one of the units and hydrobrominations in the other. It was also envisaged that the facility would be used in the future for the company's own processes and toll manufacture. Faced with a classic problem of multi-product batch plant design, the company used BatchCAD simulation studies as part of the design procedure.
- AGFA Gevaert has also applied BatchCAD simulation to a complex reactive distillation, for synthesis of the ethyl ester of pentenoic acid by successive substitution of allyl alcohol for ethanol on triethylorthoacetate, followed by in situ exothermic oxy-Claisen rearrangement of the mixed ortho esters, a total of 10 simultaneous equilibrium and irreversible reactions. BatchCAD simulation was used to increase conversion of starting material from 50% in the laboratory to over 98% in production with a substantial improvement in selectivity and reduction in the excess alcohol required to drive the equilibrium reactions.
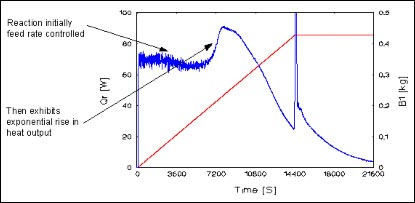
Heat output and mass added vs. time for Agfa Gevaert's peroxidation process
Technical Specifications (Back to Top)
Chemistry and kinetics
- Model complex sets of series, parallel and equilibrium reactions
- Composition, yield, reaction rate, and heat flow calculations
- MTSR calculation
- Rate parameters for multiple reactions from a single experiment
- Full statistical analysis of results
- Kinetic regression using data from routine experiments
- Combine data in objective functioncomposition, reaction heat, temperature, volume
- Impose logged experimental conditions for precision modelling of addition and temperature Index
Thermodynamics
- Physical property database with over 1800 components
- Hyprotech's powerful thermodynamic engine
- Choice of property estimation methods
- Temperature dependence of physical properties
- Regression of properties to user data Index
Reactor model
- Vessel library of over 200 leading manufacturer's standard vessels
- User configurable vessels
- Jackets, internal coils and external coils, service or process side heat exchangers and electric heaters
- Multiple service fluids for heat-cool-chill system configuration
- Reactor thermal mass, heat losses and agitation power input
- Heat transfer coefficients fixed or continuously recalculated throughout the simulation
- F factor for adiabatic operation Index
Operation and control
- Batch, semi-batch or continuous operation
- Multiple feed and product streams
- Full sequential control of reactor operation - reagent additions, pressure and temperature set points
- PID control with safety interlocks
- Vessel pressurisation and pressurisation rate for vent sizing and DIERS calculation
- Control of reactor temperature, jacket temperature or temperature differential
- Cascade control of pressure or temperature Index
Distillation
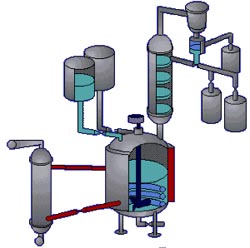
BatchCad models distillation through full and partial condenser models
- Dynamic, multicomponent distillation - batch, semi-batch or continuous operation
- Kinetic and equilibrium controlled dynamic reactive distillation - reactions in reboiler and throughout column
- Rigorous mass transfer based model avoids limitation of equilibrium models
- Column start up calculation
- Choice of condenser model
- Complete column profiletemperature, pressure, liquid/vapour phase composition and density, vapour/liquid flow
- Venting of vapours from condenser
- Condensate collection in multiple receivers with automatic integration of cut composition
- Feeds and reflux return to any tray
- Reflux ratio, column operating and vent pressure sequencing throughout batch Index
Mathematical methods
- Integration
- Solution monitored for physical discontinuities
- Integration step size constrained by sophisticated event manager
- Regression methods
- User configurable objective function
- Automatic perturbation of solution at local minimum
- Algebraic parameter constraints
- Data import transform functions and filters Index
Software engineering
- Fully featured Windows 3.X, 95 or NT product
- Intelligent interactive interface design
- Automatic construction of underlying differential and algebraic equations
- Context sensitive help with choice of language
- Model preparation wizards
- Network versions available
- Extensive choice of engineering units
About GSE Systems (Back to Top)
GSE Systems serves the chemical, food, petroleum refining, pharmaceutical, power generation, metals, and water treatment industry through its software for process control, data acquisition, and simulation. The company is headquartered in Columbia, MD, with offices in Georgia., Louisiana., Maryland, North and South Carolina, Pennsylvania, and Texas, as well as in Belgium, Japan, Korea, Sweden, Taiwan, and United Kingdom.
For more information: Chuck Miller, Simulations Product Manager, GSE Systems Inc., 9189 Red Branch Rd., Columbia, MD 21045. 7133 Rutherford Rd., Suite 402, Baltimore, MD 21045. Tel: 443 436 7500. Fax: 443-436-7502.
By Angelo DePalma