Hazards, the Safety of Reactive Chemicals, and Adiabatic Calorimetry
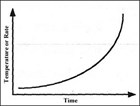
Stelios Mores, Thermal Hazard Technology
Critical Self-Heating
Multi-Faceted Approach to Hazards Evaluation
Examples
The chemical industry has become increasingly more hazardous. Since the 1950s chemical companies have made larger quantities of more dangerous and more reactive materials. Furthermore, the huge increase in the number of different chemicals produced demands rapid, inexpensive production methods.
Chemical industry hazards are nothing new. During the 19th century, when chemical products were for the most part inorganic and coal-based, most accidents occurred in the manufacture of explosives. By the 20th century, large-scale chemical production had begun in earnest. One of the earliest tragedies occurred in Germany in 1921, when an explosion of 4500 tons of fertilizer (which was being blasted with dynamite) left 509 people dead. This process may seem dangerous today, but it had been carried out 30,000 times without incident.
A great change occurred in the 1950s and 1960s, after the chemical processing industry began using oil as its basic feed stock, leading to the great diversity in chemical production we know today. The larger companies recognized the hazards and, since commercial safety equipment was unavailable, developed their own in-house safety tests. Nevertheless, instrumental techniques for testing safety were crude or inappropriate.
The most serious hazards associated with chemical processes include flammability, oxidation, toxicity, shock and friction sensitivity, dust explosions, and, of course, self-heating. These hazards may be caused by a wide variety of problems, including equipment failure, poor material evaluation, mischarging of materials, bad process design, lack of process knowledge, etc. The hazard may result from the intended reaction, during distillation, drying, or mixing, or it may present itself during storage and transportation.
Critical Self-Heating (Back to Top)
Self-heating is the most serious hazard in the chemical industry. Assessing reactive chemical hazards falls within the domain of adiabatic calorimetry because this technique alone allows safe simulation of the hazard using laboratory scale testing. Self-heating is unique in that the energy involved is solely available from the material, chemical or chemicals themselves. No other species is required. Also when self-heating occurs the entire mass increases in temperature at a uniform rate. Of course, many chemical reactions release energy (i.e., are exothermic), though in most cases that energy is easily dissipated.
Self-heating occurs with a temperature rise if the heat produced is not removed more quickly than it is generated. Early methods used to assess self-heating included simple oven tests, tests with vacuum containers or Dewar flasks, and differential thermal analysis (DTA). Because these techniques are limited, some large companies designed and developed their own test equipment. What was needed was to simulate on the small (but safe) laboratory scale what can happen on the large industrial scale.
That need was fulfilled by the adiabatic calorimeter, which measures heat under conditions where no heat is lost or gained from the sample. Most important: Data from an adiabatic calorimeter may be extrapolated from bench scale to any larger real-life scale.
During the 1970s Dow Chemical Co. (Midland, MI) developed an "accelerating rate" adiabatic calorimeter, which will be described in further detail in an upcoming article.
Multi-Faceted Approach to Hazards Evaluation (Back to Top)
The first mention of accelerating rate adiabatic calorimeters occurred in 1976 in a report from the UK Health and Safety Executive. According to the report, safety assessments for chemicals and chemical reactions must be multi-faceted, depending on whether the material presented flammability, oxidation, or other sensitivity hazards.
Initial assessment of safety or hazard potential may be gained from non-experimental investigation such as a literature search or hazard-rating scheme. Two such schemes are the CHETAH hazards evaluation software and the Reaction Hazard Index, both of which are valuable but not without limitations. The CHETAH program is purely thermodynamic, while the Reaction Hazard Index links thermodynamics and kinetics.
After this initial paper investigation, screening tests may be used to quickly gain an insight into exothermic reactions. For example, DSC with closed pans and other in-house tests may be carried out to study the hazard. After these tests, adiabatic calorimetry is carried out to give a full simulation of the hazard and the data of time, temperature, and pressure. Adiabatic calorimetry data allows easy determination of onset of reaction, magnitude of the hazard, number of reactions (whether it was a simple or complex process), speed of rise of the reaction, reaction rate at any temperature, time to maximum rate, and all associated pressure information.
Pressure data is important because pressure causes explosions. If the exothermic reaction is simple, it will be easier to get a full thermokinetic evaluation. By comparing the adiabatic calorimetry data with the information on the process vessel, it is possible to get information specifically for real-life optimization, e.g., maximum safe temperature or maximum safe size. However, a strategy for testing of self-heating hazards is normally employed.
Self-heating exothermic reactions, which are for the most part easily controlled, are needed to initiate some chemical reactions. The hazard potential is described by the speed of the reaction, the kinetics, and the amount of energy released, the thermodynamics.
When a thermal energy starts the heat generated is greater than the heat loss, the system is past its "temperature of no return." The heat generation is a property of the material; the heat loss is a property of the vessel. The latter will change depending on ambient temperature and other considerations.
Examples (Back to Top)
An elegant way to visualize runway reactions is through Semenov plots, which represent the mathematical theory of adiabatic reactions.
Figure 1 illustrates how the rate of a reaction varies with temperature or time if the situation is adiabatic. The rate increases exponentially as described in the Arrhenius theory, but the heat loss from the vessel (Figure 2) will increase linearly with temperature.
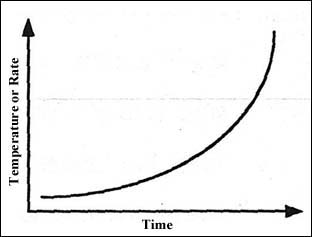
Figure 1: Self-heating for a reaction obeying Arrhenius kinetics.
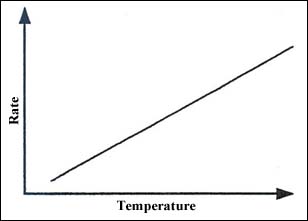
Figure 2: Heat loss from a vessel increases linearly with temperature.
We see in Figure 3 that the material in this vessel has an equilibrium temperature at A. If the material was charged into the vessel at any temperature below T, the temperature would fall to A. Filling at any temperature above T will lead to runaway and possibly explosion.
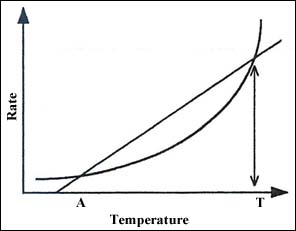
Figure 3: Self-heating and heat loss from a vessel.
But the same vessel may be subjected to another ambient temperature. In Figure 4 we see that the heat loss line will move in a parallel direction. As the ambient temperature increases, the equilibrium temperature increases and the maximum safe temperature decreases. If the ambient temperature rises to B, both temperatures are the same and this critical equilibrium temperature is called the "temperature of no return." Temperature B is called the self-accelerating decomposition temperature.
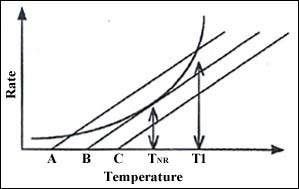
Figure 4: Self-heating of a reaction and heat loss from a vessel at three ambient temperatures, A, B, and C.
At temperatures above B this mass of sample is not safe in this vessel. This therefore defines the maximum safe storage temperature or critical operating temperature.
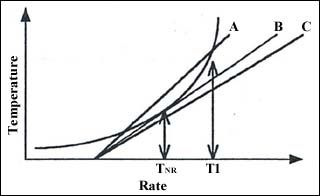
Figure 5: Another look at self-heating of a reaction and heat loss from three vessels.
In Figure 5 three vessels A, B, and C are considered at the same ambient temperature. Vessel B can lose less heat than A, and C less than B. Maybe C is better insulated or it is larger. Alternatively A might be a storage drum, B might be a 2 two-dimensional packing of drums and C a three-dimensional packing. Quite simply as the vessel becomes more adiabatic its heat loss line swings, the equilibrium temperature increases, and the maximum safe temperature decreases until again the critical temperature of no return is reached. This state illustrates the maximum pack size or critical radius of vessel that may be used.
Thermal Hazard Technology provides consulting, products, and services related to adiabatic calorimetry.
For more information: Telios Mores, Technical Director, Thermal Hazard TEchnology, Ltd., 1 North House, Bond Ave., Bletchley MK1 1SW, England. Tel: +44-1908-646-8000. Fax: +44-1908-645-209.