How A Global Pharma Manufacturer Reduced Line Stops And Increased OEE Up To 11%
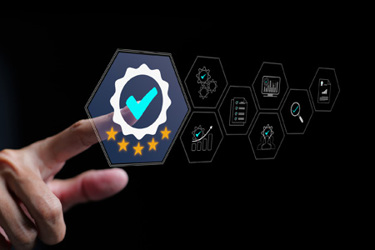
A leading pharmaceutical company encountered a major challenge with one of its most advanced packaging lines, which was responsible for assembling and packaging insulin pens in high market demand. Despite the high level of automation and efficiency, ongoing issues with the line led to significant delays in production, with missed targets, high scrap rates, and frequent unplanned stops. Uncovering the root causes proved difficult, as operators, IT staff, and mechanics each pointed to different factors, and the complexity of the line and fragmented data sources further complicated efforts to analyze and optimize performance. This situation underscored the need for a comprehensive solution to improve overall equipment effectiveness (OEE) and address capacity limitations amid growing market demand. Gain insight into how the root cause of long-standing inefficiencies was identified and how performance and productivity were optimized with unprecedented speed and accuracy.
Get unlimited access to:
Enter your credentials below to log in. Not yet a member of Pharmaceutical Online? Subscribe today.