How A Top Biotech Achieved Right-First-Time Batches For Increased Process Robustness And Lower Cost
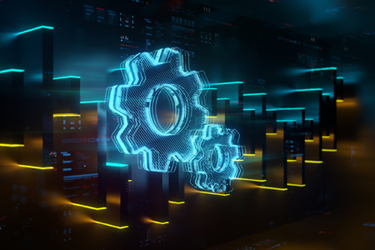
A global leader in pharmaceutical manufacturing faced significant challenges in improving operational efficiency and reducing costs due to issues with their ultrafiltration process. Frequent recirculations in the downstream process were negatively impacting the efficiency of their flagship product. Complicating matters further, essential data was spread across multiple disconnected systems, making it difficult to streamline the ultrafiltration step.
With merely half of the batches reaching the target concentration for the critical quality attribute on the first attempt, the process became unnecessarily complex. Numerous iterations and disorganized data led to wasted time, undermining productivity and putting the quality and consistency of the product at risk. Read on to learn how this ultrafiltration challenge was addressed and the resulting impact on the process.
Get unlimited access to:
Enter your credentials below to log in. Not yet a member of Pharmaceutical Online? Subscribe today.