How Active Packaging Systems Can Provide More Than Temperature Control
By Trisha Gladd, Editor, Life Science Connect
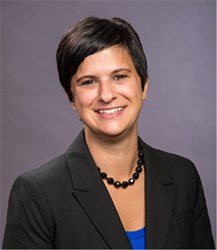
With the cost of cold chain logistics expected to rise from 6.7 billion in 2012 to 10.7 billion in 2017, it is even more important for pharmaceutical manufacturers producing temperature-sensitive drugs to select the most effective packaging solution to ship their product.
It is common knowledge that while passive shipping systems offer a lower price to the pharmaceutical manufacturer, there are risks and limitations associated with transporting a product using dry ice, gel packs, or insulation. “If there is a delay in shipment or an unexpected change in temperature, they are not actively controlling the temperature, so the chance of temperature excursion increases,” says Michael Rosenblum of Cool Containers, a manufacturer of active packaging systems. “If pharmaceutical drugs experience temperature excursion, it could be millions of dollars of product lost in just one container.”
The alternative to a passive packaging system is an active packaging system, which can control the temperature of a drug using a variety of methods, such battery-controlled heating and cooling plates and fans. Because of the technology involved in an active system, the cost can be significantly higher than a passive system. However, the benefits of an active system can far outweigh any related costs and provide advantages to a pharmaceutical manufacturer beyond successful temperature management.
Get unlimited access to:
Enter your credentials below to log in. Not yet a member of Pharmaceutical Online? Subscribe today.