How To Select The Ideal HPAPI Manufacturing Partner
By Karel Vervisch, Ph.D., Research and Development Manager, Ajinomoto Bio-Pharma Services
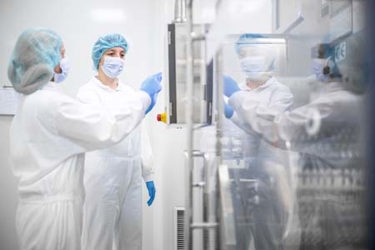
Highly potent active pharmaceutical ingredients (HPAPIs) now account for a major portion of the drug development pipeline, thanks to benefits including innovative therapeutic potential, reduced side effects, and high specificity. However, their potency poses risks to manufacturing personnel throughout the bench to commercial scale-up process. To ensure safety during HPAPI production, manufacturers must have the knowledge to effectively use containment and design high-quality equipment. As drug companies seek the most compatible HPAPI manufacturing partner to meet their goals, it is critical to understand the offerings synonymous with ample experience and safety expertise to ensure efficient timelines.
Safely manufacturing HPAPIs begins by employing an occupational exposure banding (OEB) system to designate the risk associated with a specific product. From there, containment, process analytical techniques (PATs), and personal protective equipment (PPE) are leveraged according to proven protocols associated with each band. An adept contract development and manufacturing organization (CDMO) will plan a process and equipment setup to safely and efficiently manufacture your HPAPI at-scale; the key is knowing how to recognize the partner who is most qualified to deliver your product.
A Refined OEB Strategy
To manufacture an HPAPI safely, experts must designate an OEB tier that accounts for a product’s potency and cytotoxicity. Though every company takes a unique approach to this methodology, generally, an OEB protocol consists of a series of “bands” that designate the degree of exposure to a chemical that is hazardous for personnel, known as an occupational exposure limit (OEL). When a manufacturing partner has an in-house toxicologist, they will determine your product’s OEB level during intake and the corresponding degrees of containment and PPE needed, speeding up the proposal process and ensuring proper protocols. Alternately, a CDMO would have to ship samples to a lab and await test results to be returned, delaying the manufacturing timeline and speed to patient.
Once an OEB level is established, employee training begins. In an efficient system, personnel will immediately understand the appropriate protocol to follow based on a product’s OEB tier and its previously defined procedures. From there, employees are trained in each process step prior to production. High-quality training protocols might entail hands-on simulations for employees, including the performance of lab work and handling in a containment area with a surrogate low-potency substance. This allows employees to gain comfort with the protocols without endangering their health and safety.
Placing Safety at the Forefront of Process
So, what does HPAPI handling and production look like in practice? Generally, HPAPI handling consists of a variety of activities, including repacking in warehouses, handling products in labs, placing HPAPIs into reactors, discharging HPAPIs from isolators, and taking samples of reaction mixtures within contained conditions. There are three defined tiers of HPAPI containment:
- Primary containment, which includes reactors, isolation equipment, sampling systems, scavenging units, and PATs
- Secondary containment, which is the location where primary containment is held and includes labs, warehouses, and sampling areas
- Tertiary containment, which consists of PPE worn by employees
When working with a high-risk product that has a high OEB tier, employees follow a dressing procedure for entering a containment lab. They should always be aware of the status of the containment area, i.e., if it is free to walk in, if operations are underway, or if there is a spill. Within the containment area, employees should have a set of best practice techniques that describe how to handle the product. For example, if a certain amount of product has to be weighed, best practice guidelines would provide suggestions on how to safely and practically conduct that procedure.
There should also be an outlined protocol in the event of an accidental spill. Prior to conducting any contained activities, a trained employee would verify that all necessary spill response tools are available, including appropriate absorbents and cleaning wipes. Many HPAPIs have inhalation risks; a knowledgeable employee would ensure access to a spray that prevents the product from remaining airborne. Even if a spill doesn’t occur, an area must be swabbed and tested by quality control to assess for any unseen hazards. Once that process is complete, the area can be released for another project.
Though containment is perhaps the most obvious mechanism for ensuring HPAPI safety, there are a variety of other safety techniques that CDMOs use. Prior to forming an outsourcing partnership, take an assessment of what your prospects are doing in terms of process safety. Internal atmospheric monitoring is critical to ensure that a containment lab is safe for employees to be in and to help mitigate risk. Beyond that, some CDMOs conduct regular health examinations to ensure that employees are being properly protected from HPAPIs. A trustworthy partner emphasizes a culture of safety by encouraging incident reporting, in which employees file reports to ensure that corrective actions are implemented. In the case that there is a safety incident, employees will be able to reference previous accidents to make informed decisions about how to correct a situation.
Experienced manufacturers conduct task risk analysis wherein a safety department observes handling by a lab technician working with HPAPIs. The safety reporter then describes the handling, evaluates potential risks, and suggests actions to avoid said risks. From there, the safety reporter would provide a work instruction report with visual aids on how best to conduct the handling or associated action. A consistent maintenance schedule is also vital; filters and gloves must be changed on a regular basis while air flows and circulation loops need to be continuously monitored.
Notable Process Analytic Techniques
Offering a variety of different analytical techniques reflects a CDMO’s robust HPAPI handling capacity. There are both offline and online monitoring methods, but offline monitoring requires significant amounts of sampling. As a result, online PATs are safer for employees to use. Some of the relevant and appealing online PATs include:
- Near infrared (NIR) spectroscopy, which is used for the gas monitoring of the headspace of the reaction mixture or to measure the reaction mixture within the liquid
- Fourier-transform infrared (FTIR) spectroscopy, which is used to assess the environment, or the air that the operator breathes outside of the reactor
- Ramen spectroscopy, which assesses reaction mixtures
- Focused beam reflectance measurement (FBRM), which is used for monitoring particle size distribution during crystallization
Common offline techniques include gas chromatography (GC), HPLC, and ultra performance liquid chromatography (UPLC). When you work with a partner that conducts analytical development in-house, you avoid the miscommunications and timeline delays that might pop up with a third-party lab. As a result, you establish a more efficient process to ensure timely material release.
Choosing the CDMO Best Suited for Your Needs
As you begin your search, determine which qualities and offerings are most critical for your HPAPI. The following questions are recommended jumping off points:
- How many years of experience does your team have working with HPAPIs?
- What are your methods for containment and what protocols are in place in the event of a safety incident?
- What does your atmospheric monitoring program consist of?
- Is your analytical development conducted in-house?
- Do you have in-house toxicologists and hygienists?
- What expert teams do you have in place to respond to process complexity (this might include experts in crystallization, technology development, organic chemistry, continuous improvement, analytical techniques, and process development)?
- How is your technology development team investing in innovation to meet market demands?
- Are you capable of designing customized reactors and equipment?
Once you’ve established that they have the capacity to meet your needs, request an audit of their facility with both teams’ subject matter experts present. During an audit, your team can determine whether their personnel, safety measures, equipment, and infrastructure are suited to work with your HPAPI, and they will be able to demonstrate the procedures and in-depth strategies they’d use for your product. Experienced partners will offer highly coveted handling techniques, including micronization, wet milling, and preparative HPLC. They should also have International Organization for Standardization (ISO) certificates and safety audit results to demonstrate their safety and quality track records. In response to your questions, a skilled CDMO team will request greater insight into your team’s needs, struggles, and goals to provide solutions.
A Vital Decision
Take your time and explore your options to meet the partner most qualified to achieve your HPAPI scale-up and manufacturing goals. As you shop options, look for a CDMO that leverages a risk-based approach to HPAPI manufacturing, hosts a reliable OEB protocol, and has the technology and equipment to accommodate your product. The right partner will have thoughtful recommendations on process, equipment design, and employee training, ensuring that your HPAPI production maintains quality and efficiency en route to the patient.
About the Author
Karel Vervisch, Ph.D., currently leads Ajinomoto Bio-Pharma Services’ R&D labs for scaling late-stage small molecule projects, including (photo) flow chemistry, biocatalysis, PAT, membrane technology, etc. Previously, he was the lead production engineer of one of the HPAPI production units, which makes him highly knowledgeable and insightful in the manufacturing of HPAPIs. As such, he has practical experience in both labs and scaling from pilot to production.
About Aji Bio-Pharma
Ajinomoto Bio-Pharma Services is a CDMO leading the way in research, development, and manufacturing of high-quality chemicals and pharmaceutical products for our customers. Our mission is to improve the health of humankind by being a trustworthy and innovative partner for our customers and our employees. Our contract manufacturing services have three branches: small molecules in Belgium and India, large molecules and aseptic fill/finish on the U.S. West Coast, and oligonucleotide and peptide synthesis in Japan and Belgium. We are a diversified, global customer service company focused on quality, safety, and sustainability, which supplies up to 1 billion dosages’ worth of APIs or API compounds per year. Recently, we have conducted major facility expansions across three manufacturing sites to provide increased capabilities for HPAPI production.