Implementing Predictive Maintenance Practices For Better, Faster Manufacturing
By Wahab Mahmood, Asahi Kasei Bioprocess America
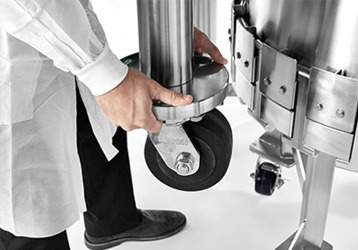
While reactive maintenance was the status quo for decades, the pitfalls inherent to this approach have only increased as pharmaceuticals have become more complex. Many organizations may fall into the trap of trying to postpone scheduled maintenance, hoping to continue operating well beyond the prescribed timelines for a particular system or component. This can result in catastrophic delays and cost overruns in the current landscape, as procuring replacement equipment can take weeks or months. Many drug manufacturers are contract development and manufacturing organizations (CDMOs) working on several client programs simultaneously. Losing one piece of equipment can create cascading impacts for the timelines of not just the involved project, but of other projects waiting for the same equipment or diverted in order to meet deadlines for other projects.
In order to mitigate the issues that attend reactive maintenance, many organizations have embraced routine maintenance as part of their overarching manufacturing strategy. While this approach offers numerous advantages over reactive maintenance, manufacturers can realize even greater productivity and uptime by incorporating predictive maintenance practices in their processes.
Get unlimited access to:
Enter your credentials below to log in. Not yet a member of Pharmaceutical Online? Subscribe today.