Influence of the Particle Size of the Inert Polymer in a Compression Coated Controlled- Release Tablet

Introduction
Numerous works in the literature have demonstrated the utility of ethylcellulose as a rate controlling polymer in direct compression inert matrix tablet formulations1-3. The drug release rates in these studies were significantly influenced by the ethylcellulose polymer level, its particle size and to a lesser degree, its viscosity grade. A micronized version of Ethocel ethylcellulose, Ethocel FP has been shown to be much more effective than its granular counterpart in these types of applications. In addition to matrix type formulations, reproducible control of drug release can be accomplished by the production of a system containing core tablets surrounded by an inert polymeric coating. The release rates from these systems are affected by the type and amount of polymer used and any defects, i.e., pores, that are intentionally or unintentionally found in the films. These films can be applied by traditional solution techniques or can be formed by the means of compressing dry powder around the core4,5. A recent study6 has addressed the physicochemical properties of the porosity modifiers on the compression coating. This work addresses the effect of the particle size of polymeric film former on the functionality of a compression coating in a model controlled release tablet.
Experimental Methods
Materials
The following materials were used as received:
- Tramadol HCL, (a gift from Ashbourne Pharmaceuticals Northampton, GB)
- ETHOCEL Standard 10FP Premium
- ETHCOEL Standard 100FP Premium
- ETHOCEL Standard 10 Premium (The Dow Chemical Company, Midland, MI)
- Dicalcium phosphate anhydrous A-TAB, granular (Rhone-Poulenc, Cranbury, NJ)
- Magnesium stearate, NF, (Mallinckrodt, Inc., St. Louis, MO).
Tablet preparation
The formulation of the core tablets consisted of 95% Tramadol HCL, 5% Ethocel 10FP and 0.05% magnesium stearate. These components were weighed into a small jar and manually mixed with a spatula for five minutes. The cores were formed on an automated Carver (model C) laboratory press with 1/2 in. concave tooling. The pump speed and dwell times were held constant at 15% of maximum and at five seconds respectively. The applied compression force was 2,000 lbs.
The compression coated tablets were prepared by placing 50% (100 mg) of coating mix, either pure polymer or binary polymer/dicalcium phosphate blends at various ratios, in a 1/2 in. die containing the bottom concave punch. A core tablet was manually centered on the powder bed and the remaining 50% of the coating mix was applied on top of it. The applied compression force was held consistent for all trials at 3,000 lbs.
Drug Dissolution
Dissolution testing of tablets was performed using a Distek dissolution system. The USP Apparatus 1 paddle with sinkers method was used at an agitation rate of 50 rpm. Dissolution profiles were generated at 37.5C, with detection at 230 nm. Tablets were introduced into 900 ml of 0.1N HCL.
Results
The average particle sizes of the three grades of ethylcellulose were five microns (10FP), 40 microns (100FP) and 250 microns (10G). Figure 1 illustrates the effect of particle size of the polymer on release rate in a pure polymer coating system. All of the tablets tested were very hard and maintained their physical integrity throughout the dissolution testing. It was found that as the particle size of the polymer decreased, the release rate slowed (% dissolved/time) and the lag times increased. This suggests that the smaller particle size polymer flows and consolidates more efficiently during the compression process, resulting in a coating with a lower degree of porosity.
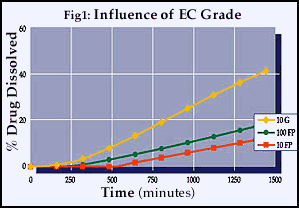
Figure 2 shows the effect of the particle size of the polymer when the coating is formulated to contain 50 wt% for a water soluble porosity modifier. Although, as expected, the release rates were increased and the lag times were shortened by the inclusion of the porosity modifier, the significant contribution that the particle size of the polymer makes to permeability of the coating is still quite profound.
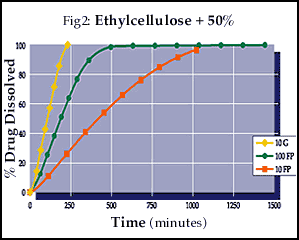
As illustrated in Figures 3-5, the final drug release profiles of a compression coating can be modified by changing the concentration of a porosity modifier even when using a micronized version of the insoluble polymer.
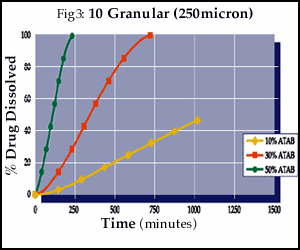
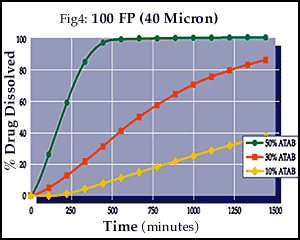
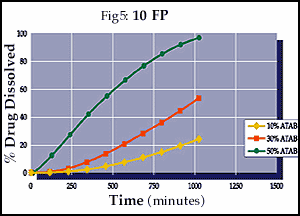
Conclusions
When developing a controlled release dosage form with compression coatings, it has been well demonstrated that the physicochemical properties of added film modifiers can be chosen to yield the desired release profile. The work presented here suggests that another variable that the formulation can manipulate is the particle size polymeric film former. The finer the particle size, the less residual porosity will remain in the coating due to efficient consolidation of the polymer powder. This in turn may allow the formulator to use fillers and/or modifiers not previously available to him to fine tune his release profile.
References
Upadrasta, S.M., Katikaneni, P.R., Hileman, G.A., and Keshary, P.R., "Direct Compression Controlled Release Tablets using Ethylcellulose Matrices", Drug Development and Industrial Pharmacy, 19 (4), 449-460, (1993)
Katikaneni, P.R., Upadrasta, S.M., Rowlings, C.E., Neau, S.H., and Hileman, G.A., "Consolidation of Ethylcellulose: Effect of Particle Size, Press Speed and Lubricants", International Journal of Pharmaceutics, 117, 13-21, (1995)
Pollock, D., and Sheskey, P., "Micronized Ethylcellulose: Opportunities in Direct-Compression Controlled-Release Tablets", Pharmaceutical Technology, 20 (9), 120-130, (1996)
Conte, U., et al, "Press-coated Systems for Drug Release Control.", Polymers in Medicine I. Biomedical and Pharmaceutical Applications., Plenum, New York. (1983)
Verhoeven, J. et al, "The Design of a Dry-coated Controlled Released Tablet for Oxprenolol with Microporous Polypropylene Powder.", J. Controlled Release, 10, 205-217, (1989)
Shivanand, P., and Sprockel, O., "A Controlled Porosity Drug Delivery System.", International Journal of Pharmaceutics, 167, 83-96, (1998)
For more information: Douglas K. Pollock, Global Technical Leader, Ethocell Polymers, Dow Chemical Company, Midland, MI 48674. Tel: 517-636-3938. Fax: 517-638-9836