Introduction To Laser-Based Headspace Inspection And The Application To 100% Container Closure Inspection
By D.I. Duncan and J.R. Veale
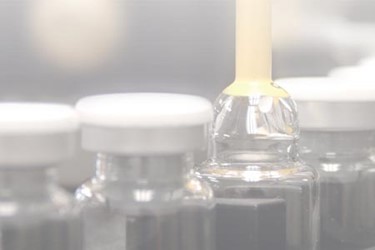
Laser-based headspace inspection is a method used for the inspection of finished sterile product. Quantifying the physical conditions in the headspace of sterile containers enables the monitoring of critical quality parameters and gives detailed insight into the process. Container closure integrity in particular can be monitored rapidly and non-destructively by headspace gas analysis. Changes in the headspace gas pressure or gas composition are leak indicators for sterile product packaged under modified atmosphere conditions. For containers stoppered under vacuum, a leak causes a rise in headspace pressure towards atmospheric levels. For containers stoppered at or near atmospheric pressure of an inert gas and exposed to air, a leak causes oxygen ingress into the headspace. The leak rates that result in pressure rise or oxygen ingress are dependent on container volume and pressure differential for a given hole size. In general the headspace pressure and oxygen concentration of small volume parenterals (e.g. 2-10mL) packaged under vacuum rise more quickly than the headspace pressure and oxygen concentration of large volume parenterals packaged near atmosphere. Detectable changes in the headspace conditions of a gross leaker occur within minutes. A micro-leak (< 1 micron) will exhibit detectable changes in the headspace after a few hours to a few days depending on the initial headspace conditions. Automated laser-based headspace inspections systems are now implemented and validated for 100% container closure inspection of sterile pharmaceutical containers at production speeds. Such implementations give insight into the process, ensure the maintenance of sterility for finished product after capping, and can be seen as a tool for meeting current regulatory guidance.
Get unlimited access to:
Enter your credentials below to log in. Not yet a member of Pharmaceutical Online? Subscribe today.