Ion Optics Developing MEMS-based IR Gas Sensors
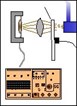
Contents
Introduction
The Competition
Applications
Markets
NIST Award Furthers MEMS Research
Introduction (Back to Top)
Infrared (IR) gas and chemical sensors have historically been reliable, accurate, and the measurement of choice for laboratory and industrial instruments. IR sensors have not achieved appreciable penetration into mass markets because conventional IR devices are expensive, high-performance units custom-built for niche applications. Like computers in the early 1970s, they consist of a cabinet full of discrete components, many of which are custom-made, almost all of which are expensive.
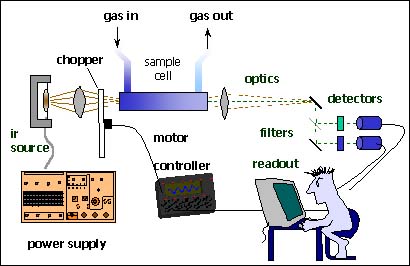
Conventional IR gas sensing uses discreet components connected by cable.
Radically simpler, standardized, IC component technology is needed to lower costs and bring these high quality sensors to the mass industrial markets.
Towards this end Ion Optics (Waltham, MA) is developing an infrared "sensor-on-a-chip" that integrates all the active optical functions of existing IR gas sensors into a micro-electromechanical system (MEMS) device, manufactured in high volumes at low cost. This new approach replaces discrete-component instruments in much the same way integrated circuits have replaced large electronic systems made from discrete components. The device will be more reliable and have greater accuracy than electrochemical sensors, and it will have reduced maintenance requirements over its expected operating life (10 to 20 years). New surface modification technology and semiconductor fabrication methods radically simplify the design and construction of infrared absorption-based gas and chemical sensors. The MEMS gas sensor will be sensitive enough to compete with much larger, more complex equipment, but inexpensive enough to penetrate the mass market applications.
"Standard non-dispersive IR instruments used on manufacturing and process plant floors today cost $500 and up," says Brian Kinkade, marketing director at Ion Optics. "A MEMS-based gas sensor with the same functionality could cost less than twenty bucks. What we're developing is basically a nondispersive IR spectroscopy system on a chip that reports adsorption at specific wavelengths. Conventional sensor do this through [expensive] optical filters. We treat the surface of the MEMS sensor so it only operates at the wavelengths of concern. For example, each sensor will operate at one or two spectral lines, typically for a single gas. Sensors won't be tunable by end-users, but will be during design and manufacturing."
Ion Optics' device will integrate emitter, detector, and filter functions onto a single die (two dimensions) so that the optical functions (third dimension) can be performed with inexpensive, molded, snap-on reflectors. The key to this level of integration is precise control of the infrared wavelengths which are emitted and received so that the device only transmits (and is only sensitive to) infrared light that is useful for the measurement.
Cost and reliability are keys to acceptance of new industrial sensors. "MEMS are cheap enough so end-users can have a bunch of these instruments around and can even network them" Kinkade stated. The low expected cost of MEMS sensors will open up a host of personal-use industrial applications, such as personal exposure monitoring through pager-sized sensor-recorders similar to personal dosimeters used in industries that handle radioactive materials.
The Competition (Back to Top)
Active-surface catalytic and electrochemical sensors have used a MEMS platform for some time. Both use an active metal or ceramic that somehow interacts with the target gaseither transforming it to another material or adsorbing it onto a surfaceultimately causing a change in the sensor's impedance. Active-surface sensors respond and recover slowly from a sensing event, however. They also suffer from memory effects, specificity/selectivity problems, irreversibility, and eventually they wear out. IR sensing operates as fast as its slowest componentelectrons moving through wires. IR detectors are tunable to any wavelength. As long as the optics aren't abused they can make millions of real-time measurements over many years.
Another gas and chemical sensor approach under development is optical detection with diode lasers, but these have problems as well. Diode lasers are difficult to tune and must be cooled. LEDs available at gas-sensing wavelengths also suffer from low efficiency, low output (~5 µW), and are expensive (about $450 per sensor).
Applications (Back to Top)
Portable, compact IR gas sensors will enjoy as many industrial applications as their price permits: The lower the cost, the more uses:
- Gas, emissions, and fuel leak detection in homes, offices, and automobiles.
- Gas leak detection for process industries.
- Quality control in chemical and pharmaceutical plants.
- Air safety/quality monitoring.
- Exhaust monitoring.
- Personal exposure monitoring for airborne chemicals.
- Research instrumentation supporting health, safety, and chemical analysis.
Markets (Back to Top)
Worldwide demand for IR gas and chemical sensors is estimated at 268,000 units annually divided among the industrial (47%), medical (26%), automotive (19%) and environmental (8%) market segments. Based on a 1996 market study by Frost and Sullivan, this market will grow by an average annual rate of about 13% over the next 5-year period. There is evidence of emerging higher volume opportunities for lower cost infrared gas sensors. According to Ion Optics demand for low-cost gas and chemical sensors could reach 90 million units per year if the devices can be made simpler and their manufacturing costs brought down. Conventional IR sensors will always face two fundamental technology limitations: steady power consumption and limited adaptability of chemical reactions for sensing different species.
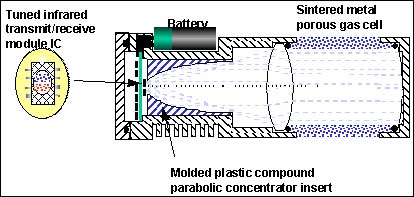
A low-cost MEMS IR gas sensor. The sensor is combined with a molded, low-cost reflective optic, e.g. a compound parabolic concentrator (CPC), which projects a collimated beam of light through an optical cell to another low-cost, plastic reflector that sends the light back toward the CPC, which then re-focuses the radiation onto the emitter. In the absence of an absorbing species, the sensor reaches thermal equilibrium with its surroundings. The introduction of a gas strongly absorbing at the peak emission band will lower the temperature.This temperature change is compared to those for a non-affected reference wavelength to remove changes in average background temperature. Ambient thermal and electrical noise is removed from the signal by observing changes at the correct modulated frequency.
NIST Award Furthers MEMS Research (Back to Top)
On October 28, Ion Optics announced it had received an Advanced Technology Program (ATP) award, from the National Institute of Standards and Technology (NIST), to develop MEMS-based IR gas and chemical sensors. Collaborating with Ion Optics will be NASA's Jet Propulsion Laboratory (Pasadena, CA), which developed the wafer-level technology enabling IR gas sensing. This three-year project should result in an infrared gas "sensor-on-a-chip" integrating all the elements of a high-end industrial gas and chemical sensor onto a single IC that can be manufactured in high volumes at low cost. Core applications for such sensors include environmental gas sensing in homes and factories, automotive exhaust sensors, medical sensors, and industrial process monitoring.
For more information: Brian Kinkade, VP of Marketing, Ion Optics Inc., 411 Waverley Oaks Rd., Suite 144, Waltham, MA 02154. Tel: 781-788-8777, ext. 103. Fax: 781-788-8811.
By Angelo DePalma