Is Excessive Pressure in The Feed Frame Causing You Problems?
By Fred A. Rowley, Solid Dosage Training
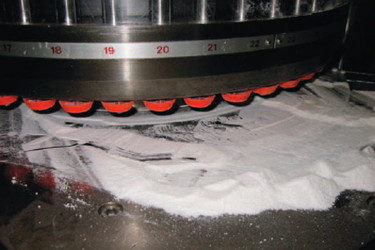
Up until about 1975, rotary tablet presses used only gravity feeders to fill the die with powder. Operators would fill the hopper and use the only control available to adjust the powder flow to the machine speed. Because there was only one control, hopper height, control of the powder flow was limited. In fact, many powder hoppers had dents from frustrated operators who would attempt to improve flow by using a mallet in an oftentimes futile effort to get the powder to flow better. The final setting frequently involved slowing the tablet press down so that the target weight specified on the batch record could be obtained.
With the advent of high-speed tablet presses, free-flowing formulations often achieved heretofore unheard-of turret speeds exceeding 3,000 tablets per minute for single-sided tablet presses.
However, this transition from slow to high-speed tablet production was not problem-free. Two fundamental problems remained: how to match the higher turret speed with powder flow and how to remove residual air trapped from the final powder blending stage. Punch entry (penetration) and pre-compression tablet thickness controls soon emerged to help remove the residual air. Improving powder flow remained a more elusive issue to resolve. This author has published several papers discussing the increased focus on critical process parameters (CPPs) for the modern tablet press.1
Veteran operators noticed that the quantity of powder placed in the hopper, called fill level, frequently improved or negatively affected how powder flowed out of the hopper into the feeder and subsequently into the die. In fact, some alert research departments even specified the fill level required for optimum powder flow on the master batch record.
Manesty developed the first power-assisted feeder a few months later and introduced this concept with its Mark II press; others quickly followed, with some competitors coining the phrase “force feeder”. And while this is true, the force was actually horizontal and not vertical, that is, powder was (then and now) moved horizontally, but it was not “forced” into the die. Figure 1 illustrates the parts of a modern powder feeder.
Figure 1: A basic power-assisted feeder
A concurrent development further complicated the situation in that large tote bins or drums could now be placed directly over the tablet press, allowing fewer hopper charges. Vacuum transfer from the floor-level drum into the tablet press powder hopper also was available. While these developments improved efficient movement of powder, they didn’t necessarily improve tablet weight variation or content uniformity. Photo 1 below illustrates the concept.
Photo 1: Fette tablet press with drum loaded
These developments required better control of powder flow into the feeder. Two primary approaches were the incorporation of a slide gate or a valve. One issue that quickly became apparent was where the best position of these control devices should be in relationship to the powder feeder. A secondary issue was how to instruct the operator in their use.
This issue remains mostly unrecognized today. And all one has to do to better understand why this remains a problem is to tour your manufacturing facility and verify the position of the valves on your tablet presses. I suspect you will find that most of the valves are in the fully open position.
A second look at your master batch record or department SOPs will alert you to the fact that there are usually no instructions in the proper use or setpoint for this important machine setting (sometimes called a CPP). Some authors argue that a specific position less than fully open is not required, while I argue it is in fact a critical operating parameter.
Consider this: The average feeder on a modern tablet press holds from 1.5 to 3.0 kg. of powder blend. Assuming that you are compressing a 200 mg tablet, the feeder holds an equivalent of 5,000 tablets at any point in time. Even at 2,000 tablets per minute press speed, you have 2.5 minutes of run time, even with the valve fully closed. So, the argument that we might run dry of powder in the feeder is a myth and is not based on reality. Further, if there is nothing to reduce (“step down”) the pressure of the powder blend from the drum/bin into the feeder, the result will be excess pressure in many cases. This pressure is significant in that it can cause blend segregation within the feeder and result in both greater weight variation and/or greater content uniformity issues. The danger is potentially even greater with a directly compressible formula or a formula where the active ingredient is micronized.
On balance, there is a valid argument that some powder blends do not flow well, even under otherwise perfect machine settings and require a fully opened feed line. This position should be challenged. The time between final blending and actual tablet compressing as a critical factor is also frequently overlooked as an equally critical factor for success as well as the level of the powder (weight) in the hopper. Optimum tablet weight and content are then a combination of the pressure of the powder blend, the position of the valve directly above the feeder, and the speed of the wheels inside the feeder. These are dynamic settings that may change with different drums of powder within the same batch or between individual batches of product in a manufacturing campaign. Photos 2, 3, and 4 demonstrate the problem.
Photos 2, 3, 4: Feeders over pressured or with valves in the wrong position
In fact, operators often see an unpleasant sight when they remove and begin to clean the feed frames after compressing a batch. They see the larger granules that have been pushed aside by excessive wheel speed and unnecessary pressure. This unreported phenomenon would likely not result in significant content or weight variation in a 1,250 mg tablet. But what about tablets less than 100 mg? Yet this critical parameter is unnoticed and undocumented, even in root cause analyses of content uniformity issues in finished tablets. Photo 5 presents a recent problematic blend segregation in a feed frame.
Photo 5: Large granules and small lumps from a feed frame after batch compression
As another side topic, manufacturing sites that produce MUPS (multiple unit pellet system) tablets were forced to recognize pressure in the feeder very early on in the development of this technology for the tablet press.2,3 With such a large difference between the coated pellets and the other components, very precise blending, holding, and charging of the final blends became an industry within an industry that remains today. Further, customized valves and their specific placement, feeder wheel design, and precise wheel speeds are now common and are even available as retrofit kits supplied by some well-known tablet press suppliers.4 Photos 6 and 7 below demonstrate how much of a pressure reduction and wheel modification might be required to produce a MUPS tablet.
Photos 6 and 7: (L) Bottom of a tablet press hopper used to produce Metoprolol MUPS tablets (R) Modified feeder wheel used to produce MUPS tablets
Pressure from a drum or bin that is not reduced will enter the feeder directly through the powder hopper. If there is a third feeder wheel directly below this entrance, this will more evenly spread the pressure as well as help deal with an occasional avalanche, but it will not reduce the overall pressure. In fact, some firms remove this wheel when compressing large tablets at high speed because the quantity of powder used on a per-minute basis is approximately the same rate as the powder entering the feeder.
In an opposite situation, wherein a small tablet is being produced at a moderate press speed, using an available third wheel is recommended. Even then, if the valve or slide gate is not adjusted to reduce the quantity of powder entering the feeder, shortly after the press goes into operation, pressure will build internally at the inactive parts of the feeder. The operator will usually see this as a necessary weight adjustment or as a shift in the fill level on the screen of the automatic weight control. At times, the corresponding accumulated reject tablet count also begins to rise. Pressure in the feeder is real.
In conclusion, careless setup of a tablet press without a corresponding set of instructions in a department SOP or master batch record is a proven root cause of both weight and content uniformity variation, especially in smaller and MUPS tablets produced at medium to high speed on modern tablet presses.
References
- Rowley, F.A: “Recent FDA Inspections In India Indicate New Focus On Tablet Press Operations”, Pharmaceutical OnLine, April 2023.
- Xu M., Heng P.W.S., Liew C.V. Formulation and Process Strategies to Minimize Coat Damage for Compaction of Coated Pellets in a Rotary Tablet Press: A Mechanistic View. Int. J. Pharm. 2016;499:29–37. doi: 10.1016/j.ijpharm.2015.12.068.
- Łunio R., Sawicki W., Skoczeń P., Walentynowicz O., Kubasik-Juraniec J. Compressibility of Gastroretentive Pellets Coated with Eudragit NE Using a Single-Stroke and a Rotary Tablet Press. Pharm. Dev. Technol. 2008;13:323–331. doi: 10.1080/10837450802089206.
- Rowley, F.A: “A Series of Special Presentations For The Food and Drug Administration Myanmar”, Research Gate, Conference Paper, December 2019.
Recommended Further Reading
- McCormick D. Evolutions in Direct Compression. Pharm. Technol. 2005;29:52–62.
- Schomberg, A.K., et al: “Modeling die filling under gravity for different scales of rotary tablet presses”, Powder Technology, Volume 424, 15 June 2023,118550.
- Xu X., Coskunturk Y., Dave V.S., Kuriyilel J.V., Wright M.F., Dave R.H., Cetinkaya C. Effects of Compaction Pressure, Speed and Punch Head Profile on the Ultrasonically-Extracted Physical Properties of Pharmaceutical Compacts. Int. J. Pharm. 2020;575:118993. doi: 10.1016/j.ijpharm.2019.118993.
About The Author:
Fred A. Rowley has more than 40 years’ experience in the pharmaceutical and nutritional supplement industries in manufacturing, technical services, and R&D settings, with particular expertise in solid dosage manufacturing and training. He has knowledge of the granulating, blending, tablet compressing, and film coating processes for more than 800 API drug substances. He is and has been retained as a subject expert by law firms, equipment manufacturers, international pharmaceutical and nutritional supplement companies, and compounding pharmacies, and has lectured at the FDA, the ISPE, and at many colleges of pharmacy around the world. Previously, he has been director, manufacturing technical support, for Watson Laboratories; plant manager, tablets and capsules, Weider Nutrition International; vice president, operations, Arnet Pharmaceuticals; OROS operations manager, Alza Corporation; and bulk solids manager, Syntex FP, Puerto Rico.