Is Pre-Compression Tablet Thickness A True Critical Operating Parameter?
By Fred A. Rowley, Solid Dosage Training
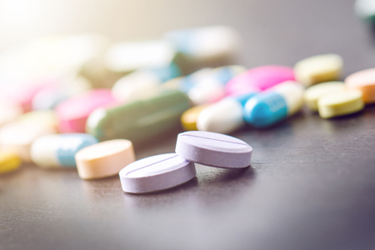
As recently as November 2023, the topic of how pre-compression tablet thickness is viewed raised its head once again in an FDA inspection at a generic pharmaceutical company in India. This control is available on all modern tablet presses, yet instructions for its use are vague.
At least three widely used tablet press manufacturers only state that the control is available for use by the operator. Further, many companies do not list this among critical tablet press control settings as critical process parameters (CPPs) on a master batch record and leave the setting to the operator.
In fact and in practice, some companies do not even provide space for the operator to write down the actual setting used during tablet compressing, while other companies require a full validation study and a subsequent control range on their manufacturing documents.1
To use this control correctly and to be better prepared for an agency inspection, a full understanding of the purpose of this key machine setting is required.
Pre-compression tablet thickness became a standard control in the mid-1970s on tablet presses manufactured in Europe. Indeed, as seen in photo 1 below, older press manuals and control labels sometimes use the term “tamping” in place of thickness when describing the control itself. An examination of this term helps to understand the intention of this critical setting.
Photo 1: A pre-compression thickness setting on a 1980 tablet press. Note that the label states “tamping”.
What exactly is a tamp, anyway? A tamp is a device used to compact or flatten an aggregate or powdered/granular material, typically to make it resistant to further compression or simply to increase its density.2 In many countries the term is also described as pre-compression tablet thickness for clear understanding.
Note the language used in a typical operation manual:
“Pre-compression is the preliminary compression force that tablet presses apply prior to the main compression. Operators often unknowingly set compression levels improperly, utilizing a percentage of the final compressive force, and this isn’t a recommended practice. Precision in pre-compression is crucial.
If an operator applies excess pre-compression, chances increase that tablets will fracture. On the other hand, if operators do not apply sufficient pre-compression, there will be increased air entrapment in the formulation. In the presence of fractures, the top of a pre-compression tablet, or its cap, may break away from its main body. This occurrence is tablet capping, and it most often happens as a result of trapped air in the powder material during pre-compression.”
— Fette Tablet Press Operation Manual
In the larger picture, pre-compression tablet thickness is part of the pre-compression station that is used to remove residual air left in the powder blend after final powder blending. Part of our understanding must include a review of the blending step, specifically, powder behavior after blending is completed and before tablet manufacturing begins.
During component blending, air is trapped between the various particles of a complex formula (often with six or more separate components, including the active ingredient). This air is a result of many factors, including the number of components, the morphology of the individual components, the type of blender used, relative fill level in the blender, length of the blending time, the manner of powder evacuation, and static electricity generated.3-6
In addition, a basic understanding of the nature of the powder percolation pattern immediately after blending stops is critical for both obtaining reliable blend samples used to defend blending parameters and for the optimized hold time of the blend before tablet compression.7
Once we have this information, we are better prepared to set relevant control settings for the pre-compression thickness control. In the absence of this information and without significant operator training and guidance, we are to some extent “guessing” what control setting is best.8-12
There are three possible control setting procedures:
- Use a mathematical ratio/percentage of the final tablet thickness setting.
- Guess based on experience.
- Manually set the pre-compression thickness based on observation with the main/final tablet thickness control disengaged.
As seen in the manual instructions above, using a straight percentage of the final thickness value or setting (the final “compressing force”) is not recommended. Doing this negates the inherent difference between individual batches of the same product.
Guessing based on experience is even worse as this again negates the inherent difference between batches or changes in component vendors or grades of raw materials.
And here we arrive at the central issue. Firms either don’t know or are not aware how to properly set this control. Operating staff frequently duck the issue by not including this control on their master batch records and leaving it up to an operator to adjust the setting.
The accepted method of setting this important control can be described in simple terms:
- Increase (“back off”) main/final thickness until the pressure rolls do not move.
- Decrease tablet thickness at the pre-compression station until you barely make a tablet. See photo 2 below. Tablet thickness can be determined either by physical measurement or visually comparing the tamps to the finished tablets at target thickness stated on the batch record.
Photo 2: A visual comparison between a tamp and a final tablet.
In many cases where physical measurement is possible, the tamp should be at least 150% of the final tablet thickness target and may be even thicker in some cases. Further, although not seen in our photograph, most tamps will fall apart with even minimal mechanical agitation. It may not be possible to measure tamp thickness. In this case, a simple photo attached to the batch record will provide adequate documentation. Remember that our goal is to remove excessive air trapped in the powder, not to make a tablet.
As agency inspectors focus on tablet press operation, it is then only a matter of time before the lack of attention to the importance of the pre-compression thickness control becomes an issue. All an inspector has to do to justify a 483 observation is ask: 1) how many batches have an investigation for capping; 2) what are the recognized settings to control/eliminate capping; and 3) what controls do you have on your current master batch record?
In conclusion, companies that recognize the new FDA focus on tablet press operation are preparing for the future now rather than waiting for regulatory action to prompt them into action later.
References
- F. A. Rowley: “Recent FDA Inspections In India Indicate New Focus On Tablet Press Operations,” Pharmaceutical Online, April 2023.
- Dictionary definition
- Kaerger, JS, Edge, S, Price, R: “Influence of Particle Size and Shape on Flowability and Compatibility of Binary Mixtures of Paracetamol and Microcrystalline Cellulose”, Eur. J. Pharm. Sci., 22, 173-179, 2004.
- Egermann, H, Kamptner, J, Pichler, E: “Effects of Interparticulate Interactions on Mixing Homogeneity”, Drug Dev. Ind. Pharm., 11: 663-676, 1985.
- Chowhan, ZT, Linn, EE: “Mixing of Pharmaceutical Solids I: Effect of Particle Size on Mixing in Cylindrical Shear and V-Shaped Tumbling Mixers”, Powder Technol. 24, 237–244, 1979.
- Velasco, MV, Munozruiz, A, Monedero, MC: “Study of flowability of powders – effect of addition of lubricants”, Drug Development And Industrial Pharmacy., 21 (20): 2385- 2391, 1995.
- Luenberger, H: “The application of percolation theory in powder technology”, Advanced Powder Technology, 10(4), 323-352, 1999.
- Ruegger, C, Celik, M: “The influence of varying precompaction and main compaction profile parameters on the mechanical strength of compacts”, Pharm. Dev. Technol. 5, 495–505, 2000.
- Vezin, WR, Pang, HM, Khan, KA, Malkowska, S: “The effect of precompression in a rotary machine on tablet strength”, Drug Dev. Ind. Pharm. 9(8), 1465–1474, 1983.
- Bateman, SD, Rubinstein, MH, Thacker, HS: “Properties of Paracetamol Tablets Produced Using High Precompression Pressures", J. Pharm. Pharmacol. 41S, 32P, 1989.
- Rowley, FA: “Preventing air entrapment and capping in a tableting Process”, Tablets and Capsules Magazine, 2015.
- Mann, SC, Roberts, RJ, Rowe, RC, Hunter, BM: “The Influence of Precompression Pressure on Capping”, J. Pharm. Pharmacol. 34, 49, 1982P.
About The Author:
Fred A. Rowley has more than 40 years’ experience in the pharmaceutical and nutritional supplement industries in manufacturing, technical services, and R&D settings, with particular expertise in solid dosage manufacturing and training. He has knowledge of the granulating, blending, tablet compressing, and film coating processes for more than 800 API drug substances. He is and has been retained as a subject expert by law firms, equipment manufacturers, international pharmaceutical and nutritional supplement companies, and compounding pharmacies, and has lectured at the FDA, the ISPE, and at many colleges of pharmacy around the world. Previously, he has been director, manufacturing technical support, for Watson Laboratories; plant manager, tablets and capsules, Weider Nutrition International; vice president, operations, Arnet Pharmaceuticals; OROS operations manager, Alza Corporation; and bulk solids manager, Syntex FP, Puerto Rico.