Is Your Lab Ready For A LIMS Implementation?
By Paul Allen, Clarkston Consulting
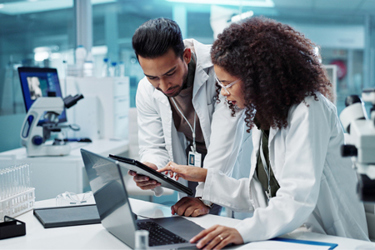
Deploying a laboratory information management system (LIMS) can boost your quality control (QC) lab's productivity. However, you should keep in mind the adage that automating bad processes will only give you bad results faster. Undertaking a LIMS initiative requires effort and will change the way your organization works. Prior to setting up the system, there are things you can do to prepare your project for success, including the space in which you will be operating.
Below, we outline the key steps for setting up your physical lab and how to optimize your lab space for a LIMS implementation.
Setting Up Your Physical Lab
Below are some questions to consider as you set up your physical lab space:
-
Does your lab layout allow for optimal workflow?
Addressing workflow issues now will be easier than after the LIMS is deployed. Think about the volume of each type of sample that comes into the lab and which instruments are required. Having all your balances in one area and particle size analyzers in another area might make sense on paper but could lead to a lot of walking for the analysts. Could this be improved by grouping instruments that are commonly used together? An interesting way to analyze this is by following an analyst for a day and marking with a line on a diagram of the lab everywhere they go. If you end up with what looks like a pile of spaghetti, think about reorganizing. - How well are your storage areas organized?
Consider this for all the areas that house samples and supplies. To effectively manage inventory, your LIMS solution1 will need to know where things are stored and how much there is. Are your storage areas well-defined, and is it clear what should be in each area? Are there old/excess samples or materials that can be disposed of? If this seems like a big effort, put together a schedule to address it over time. A series of “5S” events is a lean tool used to gain visual control over an area; its components are “Sort, Set in Order, Shine, Standardize, and Sustain.” This is a great way to get the team involved so they have ownership over keeping the space orderly in the future.
- Is the workspace prepared for the technology to be deployed?
Ensuring your workspace is prepared for deploying the LIMS solution2 is key. Some things you might want to consider before deployment include:- Workstations: Identify the places where workstations will need to be deployed for access to the LIMS. This should include an analysis of the available space and the types of equipment to be deployed (e.g. PCs, tablets, etc.).
- Printer locations: Determine how many printers you will need in the lab and the footprint they will occupy. If you intend to introduce barcoding, think about where the barcode printers will need to be located. As part of this analysis, you should consider the workflow and layout of the lab.
- Network / Electrical: Make sure the infrastructure is in place to provide network access and electricity for the workstations and printers. If you intend to use a wireless network, evaluate the signal strength and address areas with weak coverage. You may need to install additional access points to improve coverage.
Addressing these items in advance of your project will allow you to focus on the deployment of the LIMS solution instead of worrying about workflows, storage spaces, or network access. Once you’ve taken the necessary steps to prepare your physical lab space, it’s important to now turn your focus to inventory management.
Next Steps: Controlling Lab Inventory With LIMS
Deploying inventory control functionality in your LIMS can boost your quality control (QC) lab's productivity. LIMS inventory control functionality provides better visibility into your supplies and will notify you when it’s time to reorder. In advance of deploying technology, you should invest time in establishing foundational inventory management practices. This will save considerable time during the LIMS project. In addition, this process will allow you to gain insights into your spending and where you may be able to eliminate waste.3
So, what actions do you need to take to ensure you have a handle on inventory control? Below, we outline four steps to controlling lab inventory with LIMS.
1. Develop a List of Inventory Items
As a first step, develop a list of your inventory items to be tracked in LIMS and categorize them by type. For example:
- Reagents
- Solvents
- Standards
- Controlled substances
Make sure you capture everything. While you may not inventory all these things in LIMS, you will still benefit from performing this exercise on all items (e.g. glassware, disposable, PPE). When you think you have a good list, validate it against your purchasing records and what you see in your storage areas.
2. Document Your Physical Inventory
Your next step is a physical inventory of all the items you identified. Things to document during this inventory include:
- Quantities on hand (Does it seem like the right quantity?)
- Lot numbers
- Expiration dates (both manufacturer’s expiry and use-by date
- Storage location
- Date each container was opened
- Manufacturer name
- Material ID
3. Confirm Storage Areas
After taking inventory, you should decide if reorganization of your storage areas is necessary. Make sure everything has a designated place and that it’s properly labeled.
4. Consider a Laboratory Inventory Management System
Now you should think about an inventory management system.4 A Kanban system is an easy way to do this in advance of the LIMS deployment. This system has cards in each of the storage areas. Once the inventory gets below a certain level, the card is moved to a different location to indicate reorder is necessary. The beauty of establishing this system upfront is that it can live on after the LIMS deployment for those items you will not track in the system.
Gaining control of your inventory in advance of your project will allow you to effectively leverage all of the benefits of LIMS inventory management.
Next Steps: Organizing Your Operational Data
Now that your physical lab space is optimized for a LIMS implementation and you’ve gained control of your inventory management, what’s next?
From here, we advise taking time to organize your operational data. Organizing your operational information (master data) is one of the most underestimated tasks associated with a LIMS implementation. Reorganizing this information in advance of your project will greatly reduce the project effort and the stress associated with meeting timelines.
To prepare for this effort, it’s important to focus on the core master data types in a LIMS:
- Batch Records
- Test Methods
- Specifications
LIMS likes to have these data elements separated. Frequently, we see labs have combined this information into a single work instruction for each material that has the data elements interspersed. While this approach makes sense from the perspective of a human reading the document, it needs to be transformed into the information the LIMS needs. Some reorganization of the work instruction layout can greatly reduce the transformation effort5 and may actually simplify things for the human reader.
Organizing Your LIMS Operational Data
Here is a closer look at each of the types of governing documents that will be necessary to establish your LIMS master data:
Batch Records
This is the information about the material to be analyzed by the lab. Generally, this is information about the raw material, in-process material, or unreleased product. It includes the material ID, name, sampling plan, and what tests are to be performed. When evaluating this data, think about what information will need to be captured for the individual samples that are processed in the lab. These would be things such as batch number, relevant dates, etc.
Test Methods
These are the analyses that need to be performed on the sample (e.g., loss on drying, dissolution, gas chromatography, etc.). These records should include instructions for performing the analysis with any calculations clearly called out. The methods also need to identify all the data points that are to be captured. This is only the data points to be captured — not the values indicating in/out of specification. Data points to be captured vary by the complexity of the master data,6 ranging from final results only to calculated components.
Specifications
Specifications establish the criteria that will be used to determine if the material is within acceptable limits. These should be identified for each material with the limits for each data point identified in the method.
Ensuring Consistency And Accuracy
With the above in mind, can each of the master data types be easily distinguished on the work instructions? Has all of this information been thoroughly and consistently captured? A LIMS implementation7 is a great time to review procedures for consistency and accuracy. This could include aligning on a new common format for work instructions and starting an initiative to align them all.
One strategy could be to put these elements on separate pages, and another could be to create multiple columns on the page. You will need to figure out what works best for your organization. Whatever the approach, it’s important to start early to avoid costly delays during your LIMS implementation.
Moving Forward
Taking time to prepare your lab for digital transformation in a strategic and intentional manner is vital to the transformation’s success. From setting up your physical lab space to ensuring efficient inventory management to organizing your operational data, beginning sooner rather than later can save time, effort, and resources down the line.
A portion of this piece originally appeared on Clarkston Consulting’s website here. Republished with permission.
References
- Jones, L.L. (2020, September 1). Achieving LIMS Design Optimization. Clarkston Consulting. https://clarkstonconsulting.com/insights/achieving-lims-design-optimization/
- Jones, L.L. (2020, May 8), Moving From a LIMS Assessment to a LIMS Deployment. Clarkston Consulting. https://clarkstonconsulting.com/insights/lims-assessment-to-a-lims-deployment/
- Allen, P. (2023, July 27). Eliminating Waste Through Visual Controls in Lab Operations. Clarkston Consulting. https://clarkstonconsulting.com/insights/visual-controls-in-lab-operations/
- Allen, P. (2023, August 29). Establishing a Laboratory Inventory Management System. Clarkston Consulting. https://clarkstonconsulting.com/insights/laboratory-inventory-management-system/
- Jones, L.L. (2020, August 12). LIMS: The Center Piece of the Laboratory Digital Transformation. Clarkston Consulting. https://clarkstonconsulting.com/insights/lims-the-center-piece-of-the-laboratory-digital-transformation/
- Yauger, T. (2023, March 24). Best Practices for Managing the Complexity of LIMS Master Data. Clarkston Consulting. https://clarkstonconsulting.com/insights/lims-master-data-best-practices/
- Adams, G. & Jones, L.L. (2020, August 6). LIMS Implementation: Everything You Need to Know. Clarkston Consulting. https://clarkstonconsulting.com/insights/lims-implementation-everything-you-need-to-know/
[Editor’s Note: You may also like: 2024 LIMS Trends.]
About The Author:
Paul Allen is a senior manager at Clarkston Consulting working with clients in the life sciences and consumer product industries. He drives client success by leading high-performing teams that execute a variety of strategic initiatives, including operational excellence and technology deployment. Allen is a certified Project Management Professional (PMP) and volunteer for the Project Management Institute. He earned his B.S. in management science from Virginia Tech and is a Lean Six Sigma Blackbelt.