Let's Explore Packaging For Aseptic Manufacturing
By Sergio Cuevas, Packaging Materials Engineer, Boehringer Ingelheim
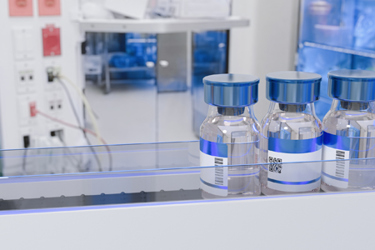
For all pharmaceutical products that cannot be subjected to terminal sterilization, an aseptic manufacturing process is mandatory to minimize the risk of microbial, particulate, or endotoxin/pyrogen contamination. The high level of complexity of the aseptic manufacturing process presents an extraordinary challenge for any pharmaceutical company.
Preventing drug product contamination requires an aseptic manufacturing process that involves everything from plant design, equipment, and processes to raw materials and packaging materials (including personnel, process monitoring systems, etc.).
European Medicines Agency (EMA) guidelines on the sterilization of the medicinal product, active substance, excipient, and primary container define aseptic manufacturing process as: “A process performed maintaining the sterility of a product that is assembled from components, each of which has been sterilized by steam, dry heat, ionizing radiation, gas, or sterile filtration. This is achieved by using conditions and facilities designed to prevent microbiological contaminants.”
Therefore, primary packaging materials, including containers and closure systems, have a fundamental role in preventing contamination, but to fulfill this function, packaging materials need to be sterilized to introduce them into the process. Sterilization is the gateway through which packaging materials access the aseptic manufacturing process. Therefore, sterilization is a key factor in the process of designing and managing primary packaging materials. Packaging design, materials, and setup are all key factors for maintaining sterilization and, thus, assurance of product sterility.
This article describes the role of packaging materials in aseptic manufacturing and the life cycle of these packaging materials from design to production, sterilization, supply chain, quality control, warehousing, staffing in the production line, etc.
The life cycle of pharmaceutical packaging for the aseptic process can be divided into the following stages: unsterile materials, sterile materials, and finished product.
The Unsterile Material Stage
In the unsterile material stage, the packaging materials are manufactured by suppliers. Container and closure system materials must be produced under controlled conditions in a cleanroom to prevent contamination. Once the packaging materials have been manufactured, and quality controls have been performed successfully, the packaging materials are packaged and prepared for the sterilization process. It is important to note that the sterilization process is carried out in sealed containers to prevent contamination and with the proper setup design (shipper box, outer bag, sealed containers, etc.) for pharmaceutical company production lines.
All shipping components involved in the sterilization process (shipper boxes, outer bags, sealed containers, etc.), their structural design (size, opening systems, shipper box layout in the pallet, etc.), and raw materials (plastic, glass, paper, corrugated carton, etc.) must be validated to ensure that they maintain sterilization levels of the primary packaging materials they contain during transport and storage until they reach pharmaceutical filling lines.
A point to highlight in this first stage is the management of materials that is carried out by the supply chain, including warehouse operations. In addition to the containers and closure systems for the filling operations, procurement of sterilized sealed containers, outer bags, shipper boxes, etc., is needed. When scheduling tasks, it is necessary to consider the resources and capacities of sterilization service providers. The shelf life of the materials once sterilized is another important point and constraint in the aseptic manufacturing process. On the other hand, the identification of packaging materials physically (labeling) and in enterprise resource planning (ERP) is very important to avoid material mix-ups among unsterile and sterile materials.
Sterile sealed container and outer bag design has great importance in the aseptic manufacturing process, not only for the sterilization process but also for feeding operations of the filling equipment, whether in a classified cleanroom, RABS, or isolator (but especially in the last two).
The Sterile Stage
In the sterile stage, packaging materials are already sterilized, and they are in the pharmaceutical production plant for employment in production lines. During inspection of the incoming materials, analytical tests are increased as part of the sterilization process, in addition to all tests performed to ensure the packaging material matches material specifications. As part of the incoming analysis, quality control tests are performed to control sterilization process performance and compliance with accepted residual limits of some sterilization processes.
In aseptic manufacturing, the filling process is carried out under controlled and monitored conditions, so the design of the materials must facilitate their machinability to avoid equipment stoppages and interventions that could change the manufacturing conditions. When filling processes take place using RABS or isolators, the rapid transfer system/port technology (RTP) becomes an important factor. RTP provides a quick transfer of materials between sterile equipment and packaging, combining safety and efficiency in the filling process.
The Finished Product Stage
It is from this moment that the sterile stage gives way to the finished product stage where sterile packaging materials (containers and closure systems) contain the pharmaceutical product. Containers, closure systems, and assembly need an accurate design to assure integrity. Integrity problems with packaging material components or assembly adjustment lead to contamination of the drug product within the primary packaging. Once primary packaging has been filled and sealed (with cap, film, etc.) on the production line, it is mandatory to perform specific tests with validation methods to detect problems in production process controls that cause leaks.
Ensuring drug product integrity is not an exclusive role of primary packaging. Secondary and tertiary packaging fulfill this function also, in addition to many other functions. Post-production teams, including shipment, distribution, and dispensing, must design processes that preserve sterility when the product moves through their domains.
Packaging materials for aseptic manufacturing of drug products are extremely complex. For this reason, you must detail in a very precise way the requirements for their production. Packaging materials’ manufacturing specifications, testing specifications, delivery, storage specifications, etc., must be detailed in documents issued within a controlled life cycle system.
The number of variables and the complexity of the process requires an exhaustive validation design to verify the effectiveness and performance of the materials, together with the rest of the factors included in the the process.
Finally, as has been described in this article, there are many issues to keep in mind when designing a packaging material for aseptic manufacturing, but it is also important to consider in the management of packaging materials three fundamental concepts: safety, efficiency, and sustainability. Reaching high values of performance in each of these parameters is necessary for achieving a suitable packaging material for aseptic manufacturing.
About the Author:
Sergio Cuevas is an expert pharmaceutical packaging materials engineer with more than 15 years of experience. He has developed his career at Alcon, Novartis, Sanofi, and Boehringer-Ingelheim. His supply chain and production department roles in those companies have provided him with a wide expertise in the pharmaceutical and medical devices industry. He specializes in packaging projects coordination thanks to a broad vision of the entire packaging life cycle (quality assurance, validation, production, etc.). He has carried out numerous studies related to chemistry, design, production, and management of packaging.