Meet The Demand: Doubling Capacity At Two 503B Manufacturing Sites
By Jason Merryman, Senior Director, Automation, Kymanox Corporation
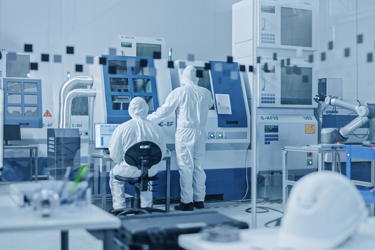
The FDA designates an outsourcing facility that produces sterile injectable medication as well as other sterile medical products as a 503B compounder. Working with 503B compounding facilities requires special attention to the associated regulations, including commissioning and qualification of equipment and clean room facilities, to maintain cGMP and drug supply chain security compliance. This case study examines a 503B compounder with two facilities that required support for doubling manufacturing capacity, which entailed designing and managing the buildout, commissioning, and qualification of new ISO 7 clean rooms for sterile and parenteral injectable manufacturing and general operations expansion. Additionally, assistance for Active Pharmaceutical Ingredient (API) scaleup, clean room recertification project management and leadership, quality system workflow management, and process/facility validation were required.
An undertaking of this size demands an experienced, cross-functional team to address the project’s complexities while navigating the associated 503B regulatory landscape. Learn more about the extensive expertise, adaptability, and skillful project-management team necessary to successfully guide a project of this magnitude to fruition.
An undertaking of this size demands an experienced, cross-functional team to address the project’s complexities while navigating the associated 503(b) regulatory landscape. Learn more about the extensive expertise, adaptability, and skillful project-management team necessary to successfully guide a project of this magnitude to fruition.
Get unlimited access to:
Enter your credentials below to log in. Not yet a member of Pharmaceutical Online? Subscribe today.