1 More Year For DSCSA Prep: Pros, Cons, & What To Do Next
By Michael Rowe, director, DSCSA/Serialization Services, Two Labs
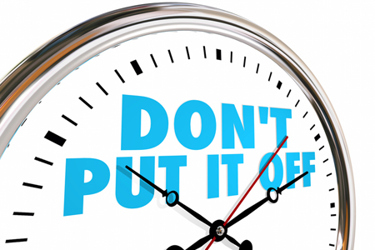
In my previous article, Practical — And Crucial — Actions To Take Now For DSCSA Compliance, I shared my perspective on how manufacturers can proactively prepare for when the FDA fully implements the November DSCSA track and trace requirements. Four months later, we are having a different discussion around the one-year reprieve the FDA has since announced.
At the end of August, the Two Labs DSCSA Serialization team and I attended the HDA Traceability Seminar in Washington, D.C. What our team did not expect was that four days before the conference, we would have to pivot our talking points and reassess the guidance we would provide clients. On August 25, the FDA announced that they do not intend to take action to enforce drug distribution security requirements under section 82(g)(1) of the Federal Food, Drug, and Cosmetic (FD&C) Act until Nov. 27, 2024. To say this announcement came as a shock is an understatement. However, the writing was on the wall when Congress wrote a letter to the FDA.
Since the announcement, you may be wondering what are the pros and cons of this announcement and what should we do now? Below, I will share my perspective on these questions and provide guidance on how to navigate the next year appropriately.
What Are The Pros Of The One-Year Reprieve?
1. Companies Have 1 More Year To Be Compliant
One notable conversation during the HDA conference was that FDA attendees emphasized that the reprieve is not a hold or stop but an opportunity to develop and validate interoperable systems and processes. Also, the FDA intends to have continuous conversations with players along the supply chain to emphasize this message and coined the term “stabilization period” to further reinforce that they don’t want the industry to delay. The FDA also has publicly communicated that they “expect trading partners to have the systems and processes to meet these requirements as of November 27, 2023”. So, the FDA still envisions that companies are fully connected and passing data by this November.
The fact that companies have time to make progress is a big “pro” in my book, but it doesn’t come without nuances, which I will dive into later.
This stabilization period serves as a great opportunity to finally reach our goal of a safe and secure supply chain to ensure there are no interruptions of product to the most important party in the equation: the patients. This period should not be used to justify any trading partners delaying their implementation efforts. Instead, it should be used to implement, troubleshoot, and mature systems and processes while supporting product availability to patients. Given that the industry still does not have a good handle on the volumes and types of clerical data, errors, or exceptions that will occur, this means that if there was no enforcement discretion, a lot of products could have been put into quarantine. Some pilot studies have found exception rates as high as 10%. That is a lot of products that, based on a flip of a switch, couldn’t make their way to patients in need. Since the legal source of transaction data will still live with the legacy lot-level data feeds (commonly called T3 data, which stands for Transaction Information, Transaction History, and Transaction Statement), if there are serialized data errors, the product does not need to be quarantined.
Immediately following the guidance from the FDA regarding the enhanced distribution requirement enforcement delay, the FDA also extended enforcement discretion on the wholesaler saleable returns verification requirements (this was simply extending existing enforcement discretion for another year to align with the Nov. 27, 2024, date). Making these essential requirements go live in tandem vs. sequenced makes sense.
2. Products Already In The Supply Chain At 2024 Deadline Can Continue To Be Distributed
Another big pro from the guidance is how the FDA addressed “transitional inventory” concerns. The way the DSCSA reads is that the Nov. 27, 2023, deadline impacted all trading partners at the same time. It did not consider product inventory already in the supply chain before the deadline (which may not have had data attached). So, that was forcing the industry to push for deadlines before November, which simply was not happening at a fast enough rate. The FDA did iterate in the guidance that any product purchased before Nov. 27, 2024, and in the commercial supply chain before that date, can continue to be distributed until that product expires. That is a good thing because it doesn’t create artificial deadlines. It also lets products that may not have data “attached” still make their way to patients. That all sounds good in theory, but once you drill down into a warehouse's operational processes, it becomes more convoluted, which I will address in the “cons” section next.
This period to work out the kinks was sorely needed by the industry. It is up to trading partners not to squander it, but it’s not that easy.
What Are The Cons Of The One-Year Reprieve?
1. Lack Of A Phased Approach
OK, so we were all happy that the FDA listened to us and moved back the deadline, giving us more time, but it seems that the FDA didn’t hear our call for a phased approach, which would hold the various trading partners accountable based on their role in the supply chain.
This phased approach, supported by various stakeholders and industry groups, proposes a two-year rollout of enforcement deadlines among the different sectors of the supply chain. These phases aim to enhance the capacity for serialized data within the supply chain, establish a stable and interoperable exchange of precise serialized data, ensure the continuous flow of essential medicines to patients, and uphold current protective measures. This strategy ensures the uninterrupted delivery of quality products to patients while simultaneously encouraging unprepared trading partners to meet the required standards without imposing excessive burdens on those already prepared. This is because the flow of data is not a “big bang.” We need manufacturers to pass data consistently and reliably first before wholesalers can intake and output data.
With the way the enforcement discretion is structured, it does not hold trading partners accountable to get the implementation done in waves. So, in some cases, it can be construed as a total delay for some for the whole year, essentially kicking the can down the road and just perpetuating the problem.
So, where does the proposed phased approach stand? The answer is currently unclear, but members of the HDA recommend attempting a condensed phased approach within the yearlong stabilization period. However, suppose the FDA does not announce its support of a phased approach within this one year or beyond it. In that case, this frontloading approach allows the remaining time to focus on system refinement, gathering feedback on data quality and accuracy throughout the supply chain, and acquiring the necessary skills to handle expectations that may arise ahead of Nov. 27, 2024, the conclusion of the stabilization period.
Transitional difficulties will persist even with the FDA enforcement discretion, including how to keep the lot-level tracing systems in production and “activate” serialized inbound and outbound scanning running in parallel…but not causing product quarantine. The only way the stabilization period will be successful is if the industry provides real-time feedback around the frequency and types of errors so we can assess readiness and put in fixes. For many companies, this may mean developing new code and “bypass” functionality not originally envisioned to log exceptions or account for transitional inventory but allowing products to ship and not get pushed to quarantine. While the transitional inventory makes sense on paper, all the serialized products in a warehouse look the same. But operationally, they behave differently when there is EPCIS data associated with that product inventory. So, there could be a period well after Nov. 27, 2024, where companies may have to segregate products with and without data and keep lot-level tracing systems operational for longer than they had planned, which means taking up more space, more IT strain, and less consistent processes for the distribution center employees and pharmacists that are handling the product. And anytime there is variability in the process, that increases the chances for defects.
2. No Insight Into Execution Of Tracing Requests
Another con, in my view, is that the FDA did not signal or provide insight into what process or “system” they would use to conduct tracing requests. This is a big question in the industry. Suppose we will use the stabilization period to ensure the industry can effectively and efficiently leverage the serialization data to identify counterfeiting or diversion. In that case, we need to know more about how the FDA is planning to execute these requests.
3. Metrics For Being “Ready” Not Specified
Lastly, the FDA has never specified what “ready” means for the industry regarding DSCSA. What metrics should the industry be using to help inform the FDA? Is it the number of connections? Exception rates? How quickly can the industry perform a trace? Without clear measures, I worry that nine months from now, we could have the same situation we are in now, where it becomes who has the loudest voice asking for yet another delay.
What To Do Next?
So, what should you do for the next 13 months? As evidenced by the FDA and the assembly at the HDA Traceability conference, do not stop! Keep pushing forward as if the deadline is this November to complete and test all data connections. In particular, take the following actions now:
- Be sure that your leadership is aware that the FDA is still expecting serialized data exchange to be in place by this November.
- Ask trading partners about their readiness plans and timelines. Ask them about what they can onboard and what their processes will be for auditing data quality. Ask also about their plans for how they will handle exceptions.
- Plan for additional testing.
- Take advantage of the stabilization period by keeping detailed records of issues, how long they took to resolve, who was needed to resolve them, and the root causes.
- Get involved in industry work groups to collaborate and test.
- Cross-train employees.
- Evaluate whether system upgrades or new partnerships would benefit your company vs. what may have been “hurried” decisions.
For companies that still don’t feel prepared:
- Secure resources and funding for finalizing.
- Take stock of inventory within your control and out in the channel that doesn’t have serialized data “attached” to identify risks.
- Develop an onboarding/testing plan and manage it closely.
- Audit existing "promoted" connections to see if they work as expected.
- Review DSCSA SOPs for completeness and enhance and/or build out work instructions.
- Seek counsel from trusted advisors.
In closing, as the industry pushes forward to a Nov. 27, 2024, deadline, there will undoubtedly be more learnings and insights that come out. The question now is whether there will be a large enough pool of companies to move the needle.
Now is the time to press forward and stabilize, not delay.
About The Author:
Michael Rowe is director of DSCSA/Serialization Services at Two Labs. He leads a team of DSCSA experts and has supported over 45 pharmaceutical companies in their DSCSA compliance efforts. Prior to Two Labs, he came from a major wholesaler (Cardinal Health), where he worked on DSCSA projects related to all sectors of the pharmaceutical distribution model. Rowe is also a certified Lean Six Sigma Black Belt.