New Wicking Approach Protects Cold Pipes From Insulation Failure
Knauf's new glass fiber insulation uses an inner layer of nonwoven nylon fibers to wick condensation away from chilled water pipes. Initially designed to operate at 35-70° F, Hygro-Wick technology is designed to keep pipes dry and prevent water from saturating insulation. It also promises to provide the same benefits for valves, flanges, and other nonuniform shapes.
Commercial Products, Chemical Possibilities
"It's a radical departure from what we're used to doing," says Knauf VP of R&D Glenn Brower. "It's so simple, I've wondered why our industry didn't think of this years ago. But the simple inventions are usually the best, and the ones that always seem to work."
According to Brower, Knauf plans to introduce its first commercial Hygro-Wick systems in late spring or early summer of this year. Initial grades are designed for interior operation at 35-70° F in commercial, institutional, and manufacturing facilities.
New grades, some specifically designed for chemical operations, are likely to follow. Brower says Knauf and DuPont Co. plan to test a new Hygro-Wick insulation system capable of working at below- freezing temperatures. Knauf will test the new system on DuPont brine lines maintained at -20° F.
Brower also thinks there are ways to adapt the insulation for exterior use.
Conventional Problems
Conventional insulation for chilled water pipes always fails, a fact Brower says is acknowledged in the publications of the American Society of Heating, Refrigeration, and Air-Conditioning Engineers (ASHRAE). Failure may occur in as little as one year or as many as 20 years. High-temperature, high-humidity environments usually accelerate the process.
The mechanism is simple. Moisture accumulates within the insulation system. As moisture wets out the surrounding insulation, it also degrades its thermal performance. This allows condensation on insulation jacketing, which may lead to dripping water and possibly mold and mildew growth.
"Imagine a 42° F chilled water pipe and outside conditions of 90° F and 90% humidity," explains Brower, who might be describing conditions on the Gulf Coast. "The difference in water vapor pressure between the pipe and outside of the insulation is 72 psi.
"If you're using a barrier, such as an elastomer that has a permeance rating 0.1, you're letting in about 50 wt% insulation weight in water annually. If you take elastomeric insulation that weighs 1-3 lb/ft3, that means you're bringing in 1-1.5 lb/ft3," says Brower.
Hygro-Wick
Insulation manufacturers have tried a number of different approaches to prevent vapor migration and condensation. These include vapor retarders, foamed glass, and foamed elastomeric systems. They slow but do not stop the problem.
Knauf began evaluating wicking designs first proposed by Vagn Korsgaard, a professor of buildings and energy at the Technical University of Denmark, nearly three years ago. Instead of trying to prevent moisture penetration, he proposed wicking away condensed water.
"It actually works a little like the new stay dry diapers," says Bowers. Typical fiberglass insulation consists of high-density glass fibers (4 lb/ft3 compared to 0.6 lb/ft3 for conventional home insulation) covered with a glass fiber-reinforced Kraft paper-aluminum facing.
The insulation is molded to for specific pipe sizes. It contains a hollow middle to accommodate the pipe. A single slit runs from the inner to outer surface so workers can slip the insulation over the pipe.
Knauf glues the Hygro-Wick nylon nonwoven material along the inner diameter of the insulation and along both sides of the slit. Once installed, the cloth wicks the moisture to the underside of the system where it evaporates. This leaves the pipe and insulation dry, and the insulation's thermal qualities intact.
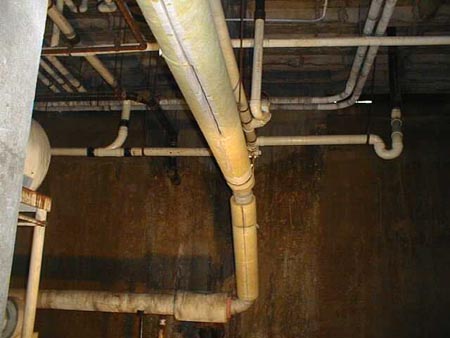
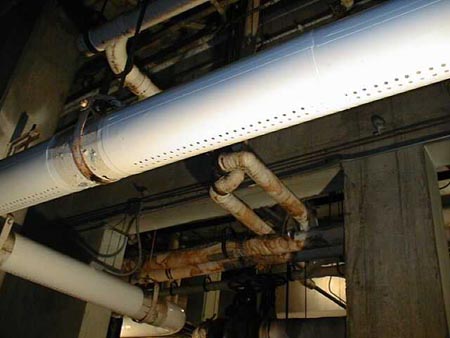
The approach promises to work particularly well with valves, flanges, and other nonuniform piping parts. "There are two ways to do it," says Brower.
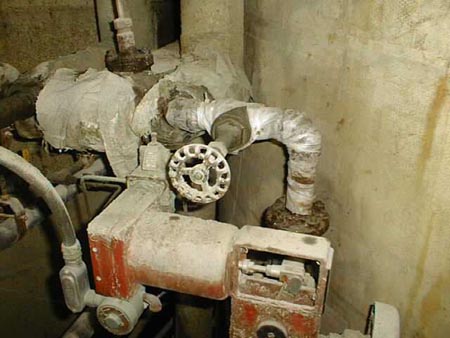
"Contractors can mummy-wrap the valve body up around the stem and down, then continue the cloth out to the pipe insulation on either side of the valve. Any water that condenses on the valve will be drawn to the insulated sections. Or they can cut out a box for the valve using oversized pipe insulation or board material."
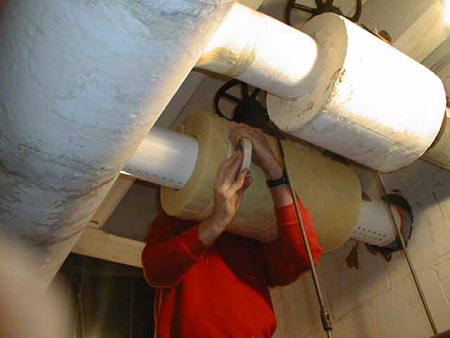
Demonstrations
"We had a number of questions about the system's limits, what it does and doesn't do, the best ways to use it," says Brower. Working with friendly contractors, Knauf installed the new insulation on a number of small and replacement jobs where standard insulation had failed. All its tests were in such high-heat, high-humidity locations as Baton Rouge, La; Boca Raton, FL; Columbia, SC; and Houston, TX.
A test done in a sausage plant highlights the limitations of existing technology. A contractor had installed conventional Armorflex elastomeric insulation. The high humidity levels in the plant soon soaked through the insulation and it began to drip water on the factory floor. "We cut off sections of Armorflex prior to insulation and found it weighted 15-42 lb/ft3 compared to 2.5 lb/ft3 for as-installed Armorflex and 62.3 lb/ft3 for pure water," Brower recalls.
Not only did Armorflex fail to insulate the chilled water pipes, but the dripping made the factory floor unsafe. It also created the potential for mold growth, a serious issue in a food processing plant.
"We installed the wicking insulation in the plant in May 1998," Brower continues. "We came back in June and August 1999, and the pipes where we installed it were bone dry. They want to use Hygro-Wick in an expansion they have planned for this summer."
Knauf also installed the insulation on a chilled water line at Katy High School in a small town west of Houston. "They had installed insulation one year previously," Brower explains. "It looked like a good job from the outside.
"But when we took off the insulation and weighed it, it had gained 20% in one year. We replaced two sections in three different places and came back one year later to cut plugs out from the insulation. I could stick my finger down to the pipe and it was bone dry. When we weighed the plugs, there was no change in weight.
Rollout
"Based on the field trials, we expect this product to provide significant benefits to everyone involved in the design, operation and maintenance of below-ambient piping systems, especially in environments with high ambient temperatures and humidity," says Brower. "It will allow them to capitalize on the low installed costs and thermal performance advantages of fiber glass pipe insulation in these applications without the associated concerns about condensation."
Knauf plans to introduce the new insulation product (and a full line of installation accessories) on a limited regional basis by late spring or early summer. It expects to be able to serve the entire North American market by the end of 2000.
For more information: Glenn Brower, VP, R&D, Knauf Fiber Glass GmbH, One Knauf Dr., Shelbyville, IN 46176. Tel: 317-398-4434, ext. 8801. Fax: 317-392-8181.
By Alan S. Brown