Overcome The Challenges Of Small Batch Production While Maximizing Yield
By Joe Hoff, Automated Systems of Tacoma
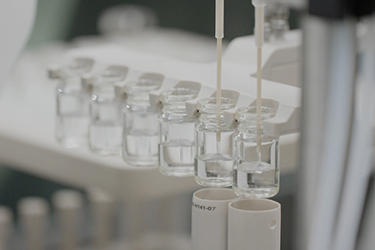
A focus on niche drugs for targeted patient populations has led to an increase in small batch production across the pharmaceutical industry. These products include advanced therapy medicinal products (ATMPs) and high-value biologics that require very complex production processes or the use of expensive active pharmaceutical ingredients (APIs) that are often limited in supply. A minimal amount of available poses major challenges when filling a product, making process efficiency a critical factor in reducing waste and improving the yield for small batches of drug product.
The Manufacturing Requirements For Small Batch Production
Product loss is inherent in biologic drug manufacturing, particularly during sterile filtration when drug substance gets held up in filters and tubing during the final phase of manufacturing. Minimizing loss during this phase is crucial when manufacturing any drug product, but it is especially important in a setting where you are working with a limited amount of product. Yield needs to be considered in every step to ensure you can meet your clinical and commercial demands. Accuracy also plays an essential role, as over- or underfilling vials could result in a shortage of product for proper dosing.
The implementation of automation and robotics is becoming a common attribute of facilities where there is an increased focus on reliability, precision, and process optimization. The flexibility that robots offer can help customer achieve increased speed to market. At the same time, the features of an automated system can also lead to other benefits, such as improved yield and accuracy. The ability to replace manual processing, which is highly laborious, prone to error, and risky from a contamination control perspective, with automated technologies that can execute reliable and repeatable process steps is the key to success in small batch production. Reducing human intervention also mitigates contamination by removing the most common source of it – the operator – thereby protecting the integrity of your product.
Planning For Scale Up
Drug development innovation typically begins in academic or R&D lab settings. Once discovery turns toward testing and animal trials begin, improving quality and documentation and choosing the right dosage format becomes increasingly important. During this stage, it is imperative to plan for future scaling of your process. Drug developers face high pressure to get their products to market quickly. If they wait to invest in automation until their process is fully understood, they will likely slow the process of commercializing a drug product due to long lead times for fill finish systems. Instead, it is important to take steps to prepare for automation by ordering a system that is flexible enough to allow your process to evolve without limitations imposed by equipment that does not easily adapt to process changes.
One commonly leveraged strategy is to purchase less automated machines, available with shorter lead times. This can help increase speed to market and perform stability or clinical studies while you begin planning for future scale up with robotic systems designed for higher volumes, reliability and flexibility but have a longer lead times to be built. This approach allows for better planning and understanding of capacity and timing needs. AST’s systems provide direct technology transfer, meaning if you develop your process on a less automated machine, you can easily transfer that process to a larger, robotic AST platform later.
The Need For Flexibility
Flexibility is a major benefit of automation and robotics during small batch production. For example, as more information about a therapy is collected and analyzed during process development and even clinical trials or new dosing formats become available, the requirements to manufacture that product may change. It is important you have equipment that can adjust to these needs, which often occur in later stages of development where costs and risks are higher. This will help you quickly and efficiently overcome technical and strategic challenges that may otherwise cause costly delays.
During process development, formulation experts and engineers must work together to mitigate any potential risks that could complicate a product’s transition from bench to commercial scale. Many companies opt for strategies that allow them to learn about their new products and dosing systems in parallel with early phase work and while larger investments are being planned to match projected capacity needs. Making sure these small batch systems offer flexibility to adjust to any process changes and packaging materials while achieving a high yield to navigate yield loss via quality sampling, etc. can be very important to ensure you maintain the highest degree of future agility.
Additionally, automated solutions can record and document data during process development steps as well as create electronic batch records (EBRs) during production runs. These features allow you to better understand the critical quality attributes of your product and analyze different variations that can help dial in the process. Once the process is understood, process settings are saved to a controlled recipe. When a batch is initiated, the system will automatically follow the recipe and ensure those parameters are used, and the EBR will document that the set process is followed. The information that is captured documents that manufacturing has followed approved and validated process steps.
When adding automation to your operations, you must find the right balance between equipment, cost, and space. The system you choose should ensure high yield, repeatability of process, quality of product, and reliability of systems. AST offers a perfect fit for all customers as they navigate their needs with their environment and long-term capabilities. For example, AST’s GENiSYS® Lab systems are designed to allow semi-automatic manufacturing, where the machines are performing critical process steps in an automated way, but the operators are still responsible for moving a container between processing equipment.
As an intermediate step up, the GENiSYS C can increase the degree of automation with only a small additional investment in capital and footprint. It is a filling and closing system for automated processing of nested, custom, and ready-to-use vials, syringes, and cartridges that is robust yet small enough to fit into an existing space. The operator leverages a tool to transfer the nest into the filler without breaking any first air principles, but the machine does the filling, IPC, and stoppering.
As regulators continue to push for advanced barriers, such as isolators and restricted air barrier (RAB) systems that prohibit the operator from intervening via open doors, robotics offers an added bonus by reducing human interaction during setup and production. AST also offers two different fully robotic lines that are modular. Both robotic systems are commonly installed in fully integrated isolators or RABs.
Finding The Right Equipment Provider
For small batch production, it is best to collaborate with vendors that are dedicated to the challenges you face. Vendors of highspeed filling equipment inherently struggle to understand the challenges you and your business encounter in small batch. Start first with a team whose equipment is purpose built to your challenges. Initial conversations should include questions from your potential vendor about your existing capacity and resources as well as your manufacturing and product needs. They must understand all aspects of your long-term goals to determine which parts of your process should be automated in order to meet them. Some questions may include:
- What type of products are you working with?
- What size batches will you need to meet clinical demand?
- Do you have a facility already available or will you be building one?
- What type of containers will you be using?
- What is your timeline?
- What is your scale-up strategy?
- What phase of manufacturing are you in?
- What markets are you targeting?
The answers to these questions combined with discussions with experts at AST can help identify the best strategy for your business. This includes whether your system needs to be semi-automatic, fully robotic, or some combination of both as well as understanding when a system needs to be fully flexible or must be designed around a specific schedule and budget.
Many of these projects also have schedule constraints. In those situations, it is important you look for a partner that can offer effective and efficient communication and collaborations. The team responsible for delivering your system is incredibly important, so you need to understand your potential vendor’s communication and project management style. AST’s project management team excels in understanding their customer’s vision and collaborating on the best path to achieve mutual success.
When it comes to installation, your equipment provider must also be able to work within the restrictions from COVID-19 and or have the experience to support you effectively. AST reduces risks associated with the current environment by leveraging a combination of innovation in our standard user interface and with modern collaboration tools. Our system can walk customers through routine processes, such as machine setup, and any issue resolutions, such as troubleshooting error codes. These features provide customers the confidence they need to successfully operate the equipment throughout the lifetime of their product.
Overall, as the pharmaceutical industry continues to evolve, small batch production will serve a critical role in the future of modern medicine. Ensuring you have the right partner and equipment to meet your current needs but also adapt easily to your future ones will serve as a key factor in remaining competitive in this constantly changing market.