Plug And Play For The Future
By Daniel McCarthy, Principal Automation Engineer, Pall
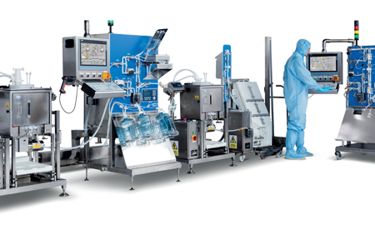
Single-use biotech process equipment is already making use of technology to automate processes and the level of complexity is increasing. As companies try to bring together a growing number of disparate process elements, integration becomes key to unlocking the full cost and efficiency gains of digitalization or Industry 4.0. For example, individual pieces of equipment generate important data related to the quality of the product they are manufacturing, but unless that data is comparable across different unit operations and accessible from different technology layers and systems, it cannot inform users about important performance insights of the process.
Traditionally, companies would opt for system integration to ensure that all of their processing equipment was able to share data and communicate with one another seamlessly, but this is time consuming and expensive, especially when you consider the level of customization and range of software platforms that pharmaceutical companies often want. For example, some companies may favor a site-wide Distributed Control System (DCS), while others may opt for a different automation architecture, perhaps one where autonomy is given to the local control system on the equipment. The second option permits the equipment supplier to leverage their expertise in exactly how best to operate the equipment. Differences in approach tend to come down to philosophy, which is often a function of size: larger companies, producing the same product in large batches might favor a more centralized system; while smaller companies may require greater flexibility, which can make integration especially difficult. Even within the same company, no two plants will have the exact same automation architecture.
Get unlimited access to:
Enter your credentials below to log in. Not yet a member of Pharmaceutical Online? Subscribe today.